Food producers, grocery stores, and restaurants are increasingly concerned about traceability in the food industry for two big reasons: they want to be able to assure customers that products are safe if an outbreak of foodborne illness or contamination occurs, and they need to be able to quickly remove unsafe food from their shelves and recall unsafe products that have been sold. At the same time, regulators are creating new food safety rules and enforcement procedures like the Food Safety Modernization Act (FSMA), while consumers are interested in knowing whether their food was sustainably sourced and ethically grown.
The problem for each of these parties is that the integration of technology into the food supply chain is occurring slowly and food traceability at levels smaller than a truckload is relatively new. Implementation of tracking in the food supply chain has been spotty, and while it’s possible to trace units of food back to their previous location in the supply chain, tracking food all the way back to its source is neither quick nor easy. Increasing traceability in the food industry requires developing tracking methodologies and enabling technologies that can improve transparency and communication.
5 Ways to Increase Traceability in the Food Industry
- Coordinate With Suppliers
- Communicate With Customers
- Develop a Transparent Database With Affiliated Information
- Create a Reporting System
- Leverage Existing Technologies
1. Coordinate With Suppliers
In order to ensure food traceability, your suppliers must know where the ingredients they use came from and which ingredients went into which products. For instance, to enable full traceability, a manufacturer of premade bagged salad mixes would need to keep track of where each lot of produce arrived from and when they were used. Doing this would create a link between farm produce lots and the final stock-keeping unit (SKU) used at the retailer.
Tracking in the food industry requires communication at every level.
While this level of tracking and record-keeping isn’t uniform across the food industry yet, it is becoming more common as regulators push for greater transparency. Communicating the need for this type of tracking to your suppliers can encourage them to implement changes and can also help you coordinate tracking with your suppliers. Tracking in the food industry requires communication at every level. Suppliers may track their product inventory diligently, but it will not improve food traceability if they fail to track it in a format that you and others can make use of. Communicating and developing common standards and practices with your suppliers is a vital first step to improving traceability in the food supply chain.
2. Communicate With Customers
Communication with your partners and customers further down the supply chain is also key. Ideally, the food tracking procedures you implement should be available to those at the end of the supply chain, whether they are a grocery store or the end consumer. When dealing with a retail partner, ensure that important data about your products and the lots used in production are shared with them.
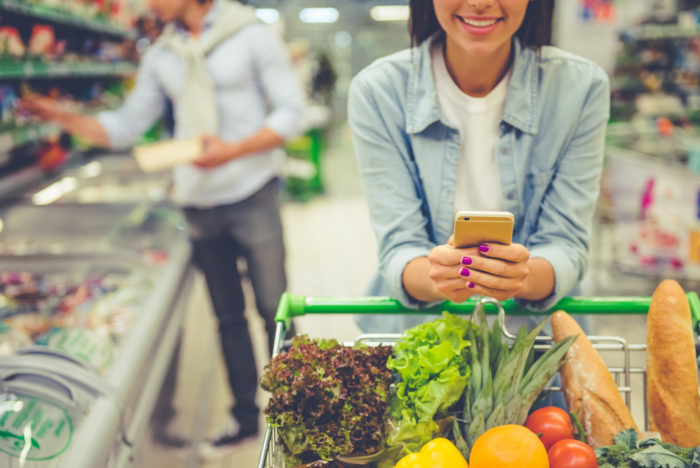
For consumers, knowing the story of their food–where it came from and how it was made–is more important than ever. Improved technology now makes it possible to share the complete story of a food item with consumers through apps and websites. Not only can this make recalls quicker and less damaging, but it can also be a means of consumer engagement. However, its effectiveness depends on having a well-developed database of information in place as well as a communication network through which information can be shared.
3. Develop a Transparent Database With Affiliated Information
Nearly every warehouse and processing center in the modern food supply chain is equipped with either a Warehouse Management System (WMS) or an Inventory Management System (IMS) that tracks inventory and throughput. However, many of these systems and the standards they use were adopted before the nationwide networking of systems was common, and, as a result, food producers, carriers, and retailers may lack a record-keeping system that all can access.
Greater transparency of information concerning food sources and handling is needed to increase traceability in the food industry.
However, technology makes it relatively easy to share specific batch or lot information with the next organization in the supply chain. Food producers and carriers can implement procedures that make sharing selected lot information an automatic part of the custody chain for food. Third-party WMS and IMS service providers may also have a unified database that producers, carriers, and retailers can access as needed. Regardless of the method, greater transparency of information concerning food sources and handling is needed to increase traceability in the food industry.
4. Create a Reporting System
Access to data concerning how a food item was handled, its ingredients, and the source of those ingredients isn’t useful with regard to food safety unless issues can be seen and rapidly shared with the company or other organization that currently has custody of the food. If these organizations share a database, then software can be used to compare recorded variables in order to determine if safety lapses have occurred and to issue an alert.
A reporting scheme for these alerts should also be implemented so that managers who receive alerts are able to easily contact other organizations in order to intercept compromised food before it makes it to consumers. In theory, with adequate testing, data recording, and a rapid method of reporting issues, it may be possible to keep most instances of compromised food from ever reaching consumers.
5. Leverage Existing Technologies
The basic technology needed to increase traceability in the food industry already exists in the form of the SKUs used by grocery retailers. Food producers also track the source of their food and associate the source with outgoing batches. The issue is keeping track of these associations as food is transported by carrier and moves from one system into another. However, an established and widely available technology offers one solution to this problem.
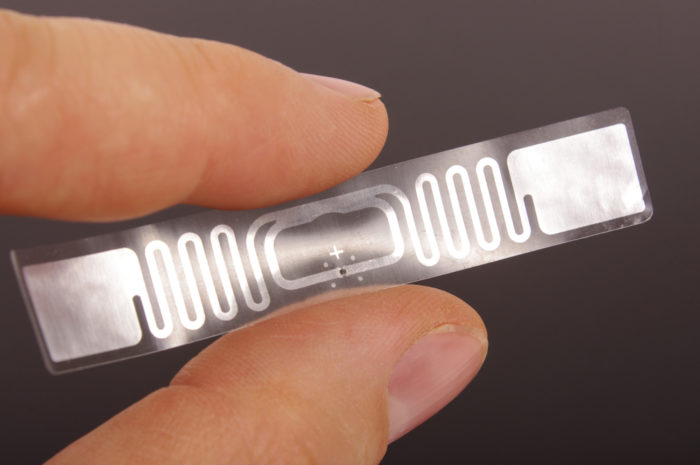
Radio Frequency Identification (RFID) has been available since the Second World War. Small RFID chips can be used in the food supply chain to broadcast a Global Standard 1-compliant number that acts as a unique identifier just like a SKU. When food packaging is equipped with one of these chips, it makes an excellent bridge for data association between different inventory systems. Yet, as anyone working in the food supply chain knows, equipping individual product packaging with these chips would be an expense that exceeds the narrow profit margins of the food industry. A workaround is to use RFID to track food products at the pallet level.
Increasing Food Traceability Using Plastic Pallets
Attaching RFID chips to pallets enables food traceability across different organizations and allows the tracking of food in amounts smaller than an entire batch. RFID chips can also be read remotely with the proper equipment, so they make data capture far quicker than the traditional method of scanning each individual carton. However, not all pallets can be reliably outfitted with RFID tracking. In fact, it takes a specific type of pallet to economically enable this method of food traceability.
High-quality plastic pallets with embedded RFID chips provide a nearly foolproof means of tracking.
Plastic pallets have a unique advantage over wood shipping platforms in that an RFID chip can be embedded in the pallet where it cannot be easily damaged or removed. In comparison to wood pallets, which frequently lose boards and can easily lose the board to which the RFID chip is attached, high-quality plastic pallets with embedded RFID chips provide a nearly foolproof means of tracking. When RFID-enabled plastic pallets are used in conjunction with a pallet pooling service, they make increasing traceability in the food industry an efficient, economical proposition.
iGPS rents RFID-equipped GMA spec plastic pallets that can be used to increase traceability in the food industry and other sectors where tracking is a priority. To enjoy the benefits of a superior shipping platform, give our team a call at 1-800-884-0225, email a specialist at switch@igps.net, or visit our contact page.