A plastic pallet is a flat platform made from durable plastic, used for transporting, storing, and handling goods. Unlike wooden pallets, plastic pallets are resistant to moisture, chemicals, and pests, making them ideal for hygienic environments.
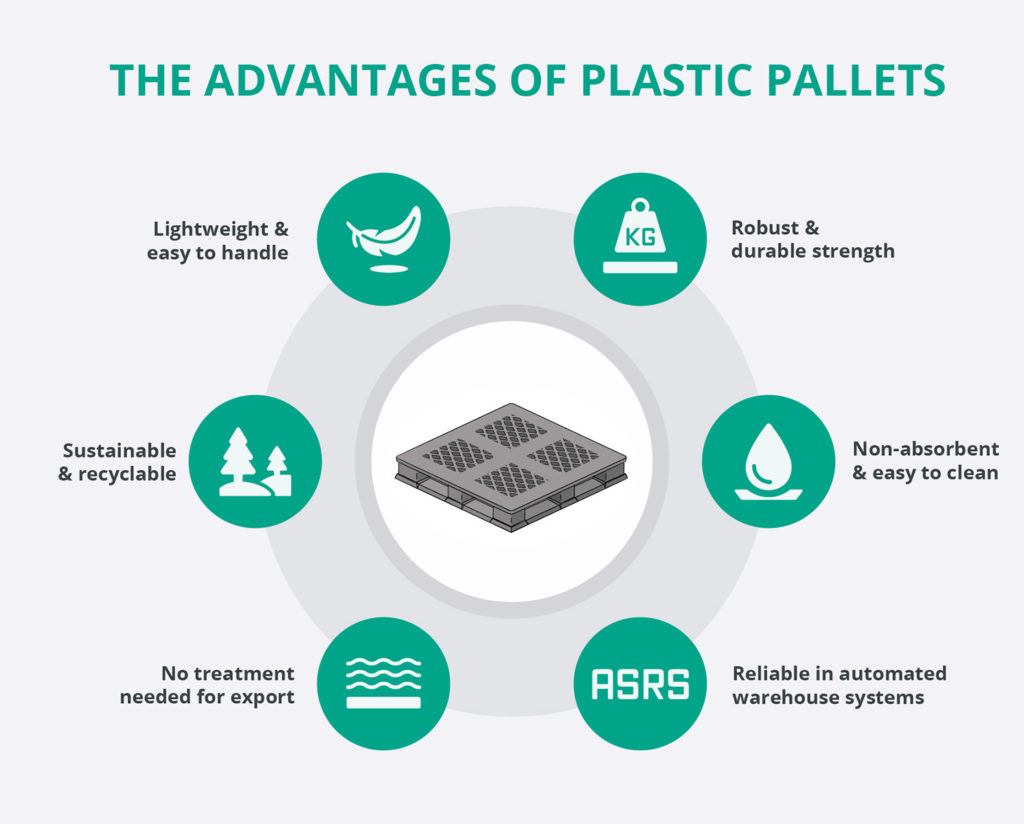
There’s a reason companies are switching from wood to plastic pallets — and there’s a reason so many retailers are asking them to switch. Plastic pallets are the next evolution in unit-load level shipping platforms. Companies that have adopted plastic pallets as their primary shipping platform have lowered their Total Cost of Business (TCOB) and increased the sustainability of their supply chain thanks to the many quantifiable advantages of plastic.
To help you determine what kind of plastic pallet you need, we’ve prepared a definitive guide. Clicking on a pallet below will take you to a description of that pallet type and how it’s used in the supply chain:
Are sanitary enough for bagged lettuce but strong enough for bagged concrete.
Allow you to easily track shipments through RFID technology.
Meet the highest standards of platform hygiene, according to the FDA’s Food Safety Modernization Act.
Are compliant with Consumer Brand Association (CBA) specs.
Guide
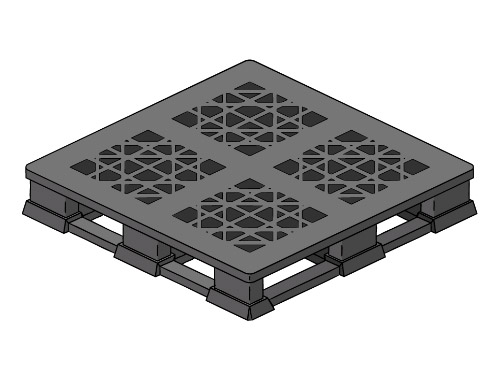
CBA Pallets
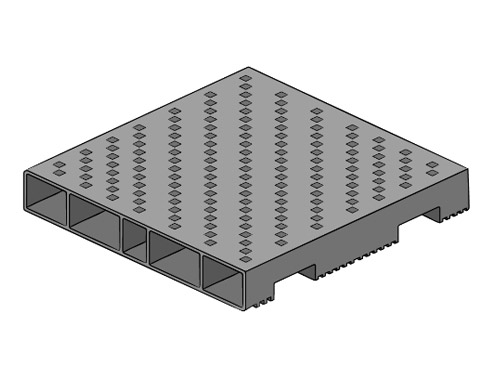
Australian Pallets
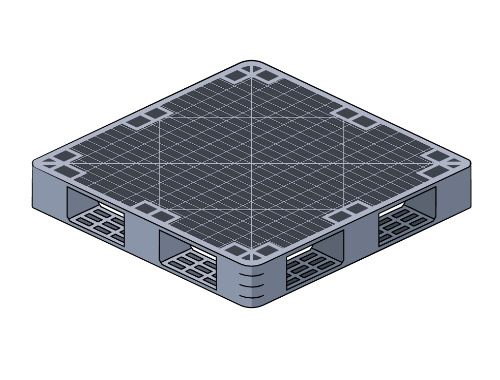
Asian Pallets
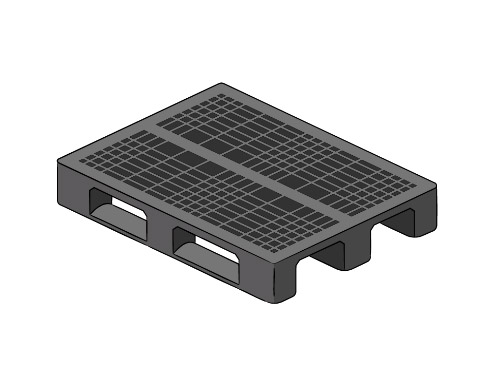
Euro Pallets
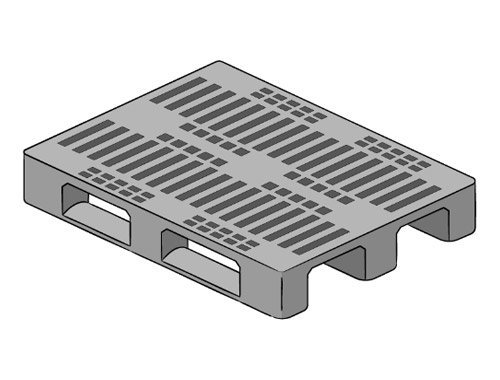
1200×1000 (Euro 2)
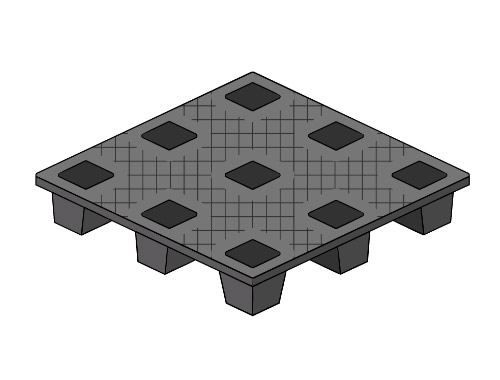
International 1067 Pallets
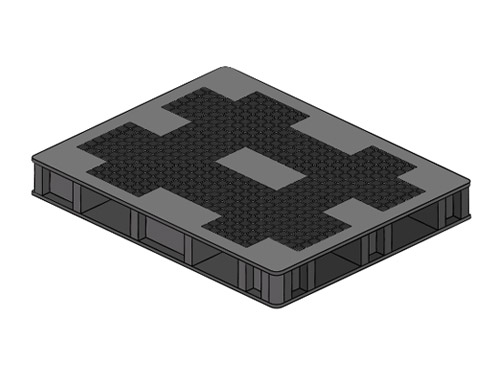
Beverage Pallets
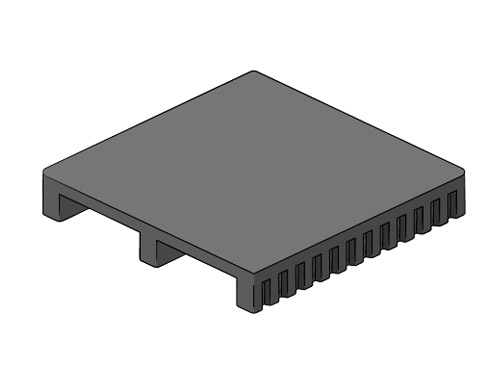
Dairy Pallets
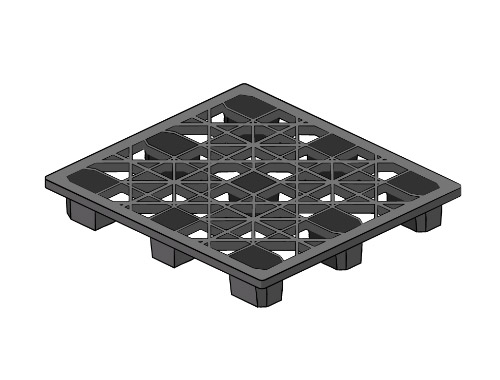
Automotive Pallets
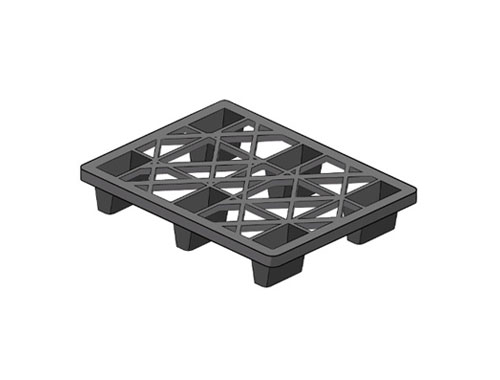
Half Pallets
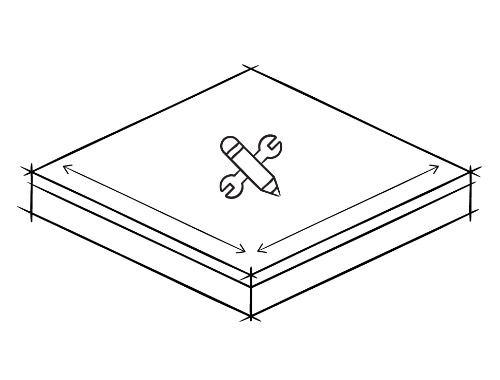
Custom Pallets
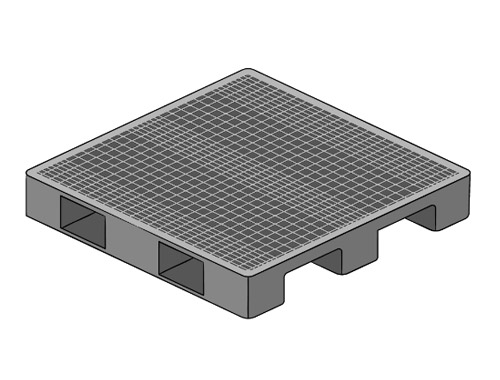
Three-Runner Pallets
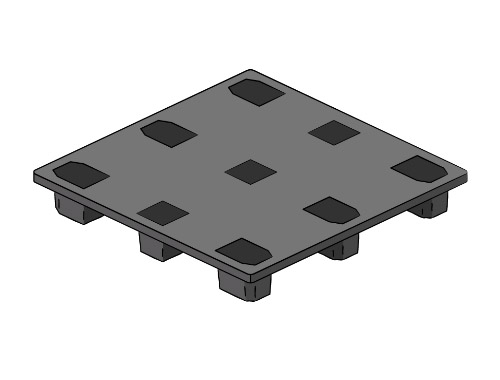
Nine-Legged Pallets
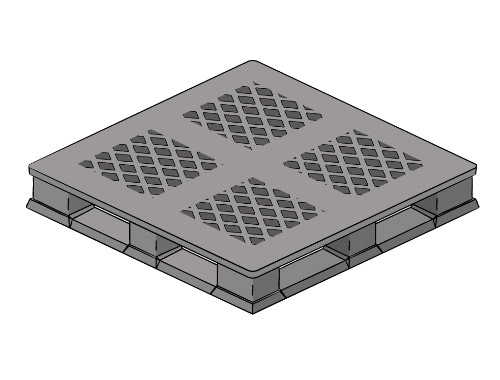
Six-Runner Pallets
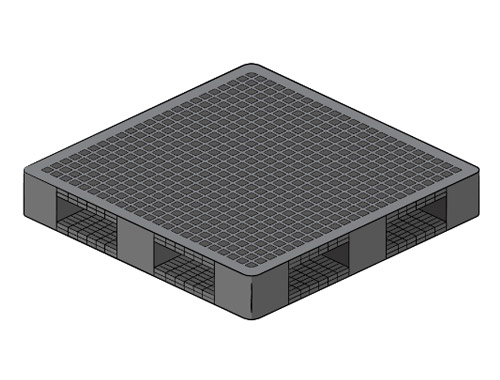
Double-Sided Pallets
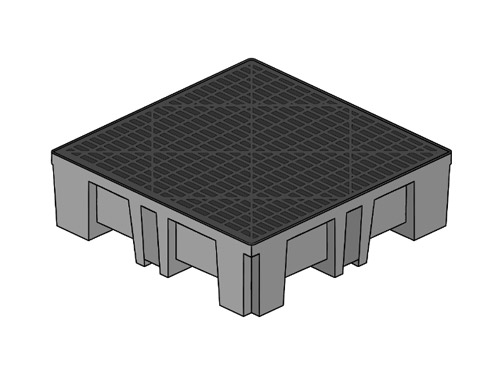
Drum Pallets
Each type of plastic pallet has its strengths, which are adapted to the industry in which it is meant to work. Some pallet types also have specific weaknesses that make them unsuitable for use outside the industry or region for which they were designed. Choosing the right plastic pallet for your business drives supply chain efficiencies that can reduce your TCOB and make your business more environmentally friendly.
What Kinds of Plastic Are Used to Make Pallets?
The type of plastic a pallet is made of affects how it is used, how many times it can be reused, and whether it can be recycled economically. It’s important to understand some basic facts about plastic before you choose the plastic pallets your company will be using over and over again.
Plastic is really a catch-all term for a synthetic polymer, which is formed of repeating strings of smaller molecules — called monomers — bonded together to form long molecular strands. The polymers used to make plastic pallets are synthetic and fall into the two broad categories below:
Thermosets
These plastics can be melted once and then are permanently set into form once cooled; they cannot be softened if they’re reheated. The advantage of thermoset plastics is that their ignition point is very high, making them a very low fire risk. However, this property means they cannot be easily recycled and in some cases may not be recyclable at all.
Thermoplastics
Plastics in this category always soften when heated and resolidify. Thermoplastics can be recycled many times over. As a result, even if a thermoplastic pallet receives severe damage, it won’t end up in a landfill. These pallets can instead be recycled directly into new pallets for true cradle-to-cradle reusability.
Of the two types of plastics that can be used to make pallets, thermoplastics are preferred and far more common. Their ease of recyclability ensures a supply of materials for reuse and helps companies create a sustainable closed-loop, or circular, supply chain. The three most common types of thermoplastics used to make plastic pallets are:
Polyvinyl Chloride (PVC):
PVC is one of the world’s most popular thermoplastics. It is very dense, very hard, and has excellent tensile strength. It is also very modifiable–adding different chemicals into the mix changes its properties, making it rigid or flexible as needed. This alteration makes recycling a challenge, though. PVC also tends to grow brittle at low temperatures, so plastic pallets made of this material are unsuitable for use in the cold chain. PVC is used in construction, household applications (shower curtains are often made of PVC), and in the healthcare industry.
Acrylonitrile Butadiene Styrene (ABS):
Used to create everything from car bumpers to keyboard caps to LEGO blocks, ABS is strong for its weight, as anyone who has stepped on a LEGO can attest to. It has a wide variety of applications, including pallets. ABS has the drawback of being prone to light damage, as well as being hazardous when burned. It is also unsafe for food contact. While technically recyclable, ABS requires specialized recycling equipment that isn’t widespread, so it often ends up in a landfill.
Polyethylene (PE):
This is the most popular plastic in the world and is used to make shopping bags, water bottles, and toys. It is one of the simplest plastics there is and its properties depend on its density. Low-density polyethylene (LDPE) is used for plastic bags and laboratory tubing. High-density polyethylene (HDPE) makes everything from milk jugs to industrial-strength plastic pallets. Polyethylene is strong, stable at temperatures from high to low, and its different densities can be recycled together to easily create useful new products. HDPE is the preferred material for high-quality pallets such as iGPS pallets due to its strength, stability in all temperatures, and true cradle-to-cradle recyclability.
Another issue for both PVC and ABS plastic pallets is their vulnerability to deformation by common solvents. ABS shows some degradation with exposure to common food products like citric acid and milk, and severe degradation when exposed to common industrial solvents like acetone. PVC has fewer vulnerabilities but can also degrade with exposure to acetone. The reactivity of these two plastics and the potential for chemical leaching and physical degradation when exposed to common substances make them unsuitable for use as plastic pallets in the food industry and other sensitive industries.
PE plastics, in comparison, have a wide range of compatibility with solvents and are the preferred choice for use as plastic packaging for food. HDPE also has the strength for heavy-duty industrial use. Of the three types of thermoplastics that can be used to make plastic pallets, HDPE is by far the most versatile option. When HDPE is used to make plastic pallets in a standardized size, the result is a pallet that can be used in nearly any industry without difficulty.
What Sizes Do Plastic Pallets Come In?
Just as different languages are spoken in different countries, some pallet sizes are used only in certain countries or industries. This means that moving a pallet load of product from one stage of the supply chain to another, or from one country to another, isn’t always simple. Differences in product packaging may mean that products don’t fit efficiently on a pallet and different transportation methods might mean that pallets don’t easily fit into containers, which can lead to wasted space and product damage.
In order to ensure a measure of uniformity among pallets, local trade associations standardized sizes and specifications. Later, six of these national standards were adopted as international specifications by the International Organization for Standards (ISO). The full six, their measurements in metric and American Customary Units, and their region of use, can be seen in the following chart:
ISO Standard Pallet Sizes
Trading Name | Dimensions in Inches | Dimensions in Millimeters | Region |
---|---|---|---|
Consumer Brands Association (CBA) (formerly GMA) | 48×40 | 1016×1219 | North America |
EURO | 31.5×47.24 | 800×1200 | Europe |
1200×1000 (EURO 2) | 39.37×47.24 | 1000×1200 | Europe, Asia |
Australian Standard Pallet (ASP) | 45.9×45.9 | 1165×1165 | Australia |
International Pallet (no official name) | 42×42 | 1067×1067 | North America, Europe, Asia |
Asian Pallet (no official name) | 43.3×43.3 | 1100×1100 | Asia |
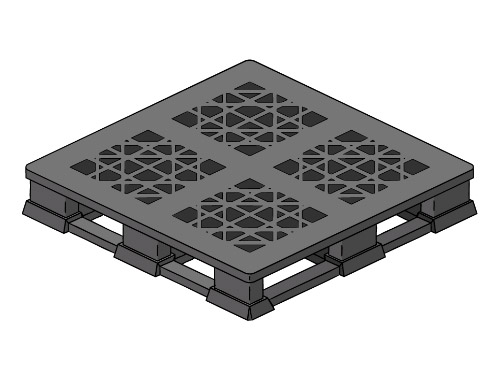
CBA Pallet: In North America, pallet standards were first set by the Grocery Manufacturers Association (GMA), now rebranded to the Consumer Brands Association (CBA). The CBA settled on a 48×40-inch pallet as the standard for the grocery industry. These pallets went on to become the most commonly used pallets in North America across many industries.
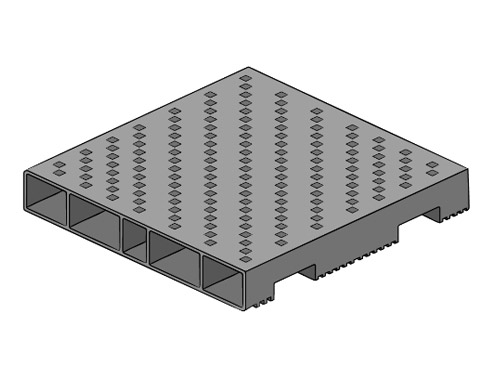
Australian Standard Pallet (ASP): The ASP evolved in the aftermath of the Second World War from pallets left behind by the U.S. military, which were also perfectly square. The size was modified from the original 48×48 inches to a slightly smaller 1165×1165 millimeters (mm) to make the pallets easier to handle, and later Australia developed the specialized RACE railway container to fit two ASP pallets side-by-side. This size of pallet has been retained despite being particular to Australia and complicating international trade.
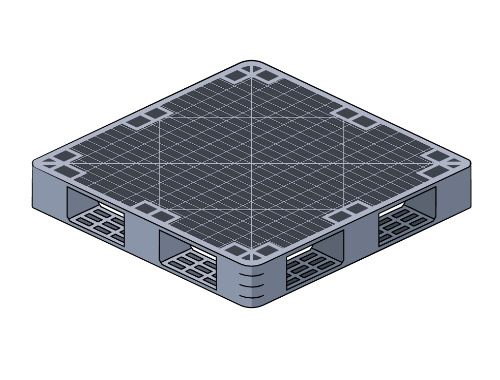
Asian Pallet: This pallet came into common use in Japan and Korea after the Second World War, and in China somewhat later. Australian industries transfer their products to these pallets for international trade. At 1100×1100 mm, they are incompatible with pallet racking systems in Europe and North America and are losing share to the type one Euro pallet in the region for international trade.
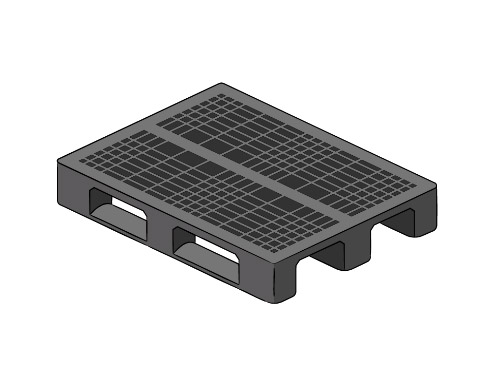
Euro Pallet: The original 800×1200 mm Euro pallet was standardized in 1968 and predates the body that is now responsible for standardization and licensing. Its smaller size in comparison to other pallet standards enables it to fit through standard door openings. However, it does not fit well into ISO standard shipping containers and increasing global trade beyond Europe has contributed to a decline in its use. It is compatible with North American pallet racking systems, however.
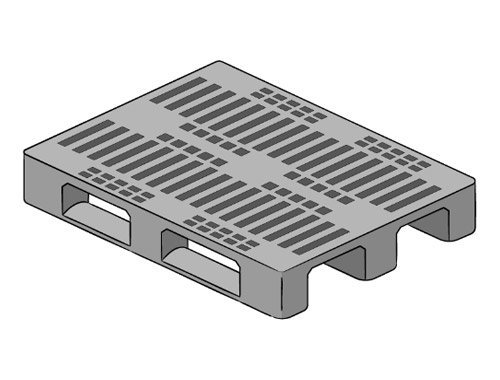
1200×1000 (Euro 2): The type two European pallet — of a total of six standard European pallet sizes set by the European Pallet Association — is a close equivalent to the North American GMA pallet and largely compatible with North American pallet racking systems. This has helped it find increasing use in North America and Asia as well as in Europe.
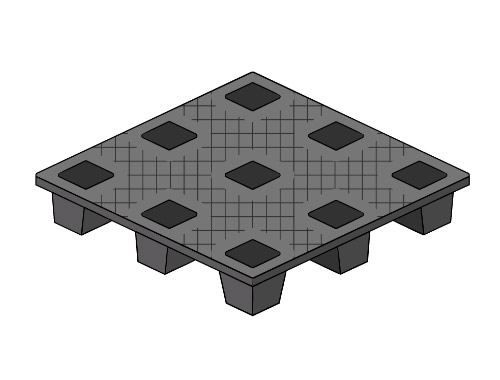
International 1067: The 1067×1067 mm pallet is a bit odd. Despite its metric sizing, it originates with the U.S. military and was originally designed for efficiently transporting ordnance. It is also incompatible with North American and European racking systems and fits poorly into ISO shipping containers. Despite these issues, it is still widely used in Asia, America, and Europe in the paint and telecommunications industries.
These six standardized pallet sizes are interoperable for international trade, but only to a certain extent. While all of these pallet types can be used with material handling equipment like forklifts and ISO standard shipping containers — at least to a degree — not all of them are compatible with regional storage systems. Pallet racking systems in Europe and North America are designed to hold pallets that measure approximately 1200 mm in width. Pallets with shorter dimensions will simply fall between the rack rails. ASP, Asian, and 1067 International square pallets are all too small for North American and European racking systems, yet they are still recognized as international standards for trade.
Pallets measuring at least 1200 mm (47 inches) are standard for consumer-facing supply chains in North America, Europe, and, increasingly, in Asia. Smaller pallet sizes are confined to internal markets in Asia and Australia or used for industry-to-industry trade. Industry-to-industry shipments use non-standardized pallets in a dizzying array of sizes, types, and forms. Some industries, such as the beverage industry, use a non-standard pallet size for their internal logistics but pack their products onto a CBA standard pallet for shipments to grocery retail partners. When choosing plastic pallets for your company, opting for a standard-sized pallet and using equipment that works with it at every point in your supply chain can simplify your company’s logistics operations.
Industry — Specific Pallets and Pallet Forms
Within industries, there’s a pallet for every purpose. There are so many, in fact, that an exhaustive list isn’t possible. However, industry-specific plastic pallet types that are common and often used across multiple industries do bear mentioning.
Plastic Pallet Types by Industry
The type of plastic pallet that an industry uses is often determined by the specific operational requirements of that industry. The most common industry-specific pallet types can be found below:
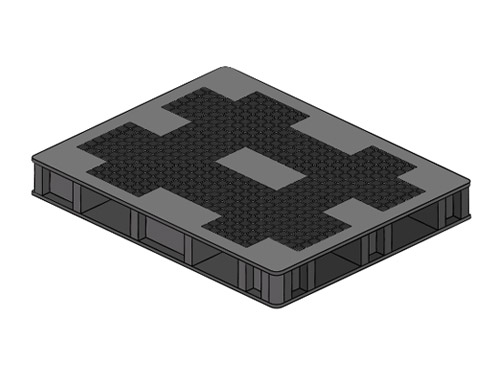
Beverage Pallets: The pallets used by the beverage industry have a smaller size than is typical of most industries. This lets the pallets fit into the smaller loading bays on beverage and beer trucks as well as the doors found at convenience stores and corner shops. There are several sizes of beverage pallets, including 36×36 inches, 37×37 inches, and 36×48 inches. The beverage industry also utilizes a bulk beverage pallet size to move empty bottles and cans between container manufacturers and the bottling plants where they will be filled. These larger beverage pallets typically measure 44×56 inches.
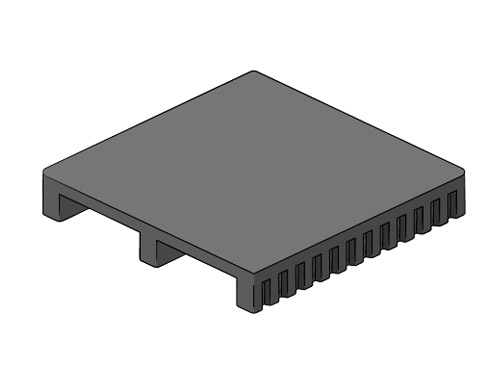
Dairy Pallets: The packaging of dairy industry products dictates the size of dairy pallets. Gallons of milk come four to a 13×13-inch crate, which fits in a layer of nine crates on a 40×40-inch dairy pallet with only about half an inch of wasted space on either side.
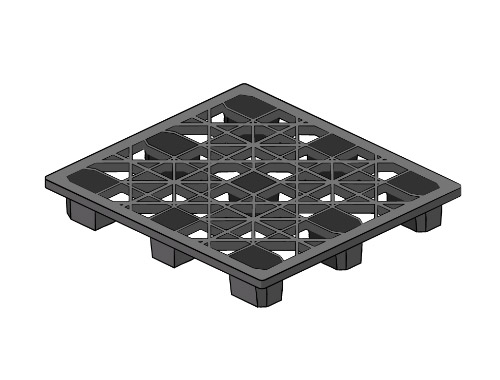
Automotive Pallets: Parts for automobiles ship on pallets that measure 48×45 inches because the plastic totes that many automotive parts ship in can fit neatly on a pallet of this size with little wasted space.
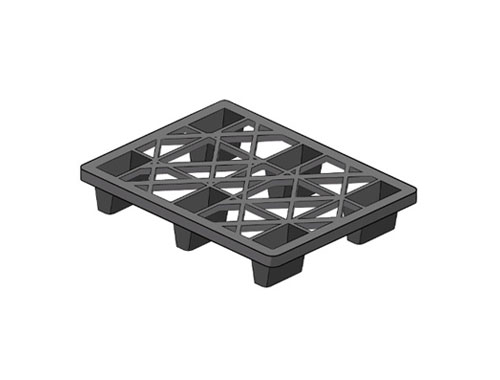
Half Pallets: Smaller 48×20-inch or 40×24-inch pallets are an ideal size for displaying products in store aisles without obstructing customers as they move around the store. The larger size of these–the 48×20-inch pallet–is also wide enough for edge racking, which makes it more versatile.
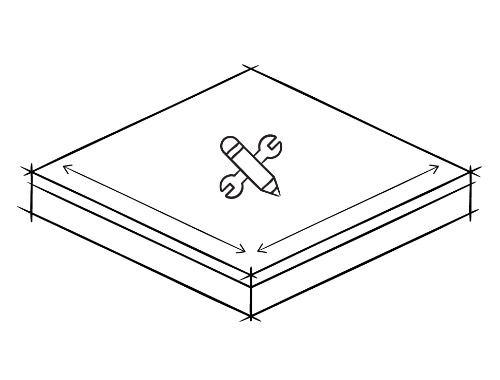
Custom: Heavy goods like automotive engines, drivetrains, and even whole motorcycles don’t fit on pallets of the usual size and proportions. The solution is to have a custom pallet built to properly support the unusual shape of the product. Traditionally these custom platforms have been made of wood, but plastic is increasingly being used in the form of PVC planks cut and fastened together. Occasionally ABS is injected into a custom pallet mold, though this limits utility and recyclability.
Frequently, industry-specific pallets like those listed above are used only at certain stages of the supply chain, while ISO standard pallets are used at other points in the supply chain. Auto parts, for instance, may ship from one factory to another on an automotive pallet, but those same parts will be shipped to a retail store on a more common 48×40-inch pallet designed to fit neatly into a truck.
Plastic Pallet Forms:
Simply put, a plastic pallet’s form is its shape, which affects how the pallet is handled and used. Pallets may be designed to be stacked on top of each other when they are fully loaded to make efficient use of transportation or may be designed to nest inside each other so that they take up very little space when empty. The most common types of pallet forms are listed below:
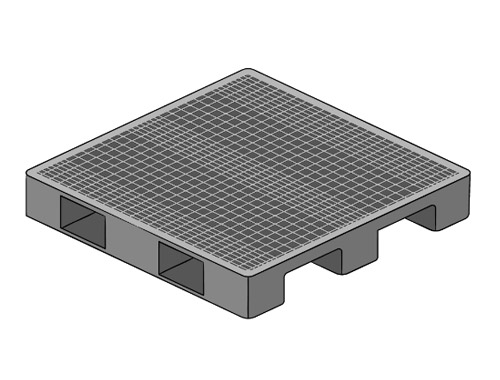
Three-Runner Pallet: Deriving their name from the three parallel structures underneath the top deck, three-runner plastic pallets are technically skids due to the lack of a bottom deck. The three runners may either be notched to enable four-way entry or left solid, in which case only two-way entry is possible.
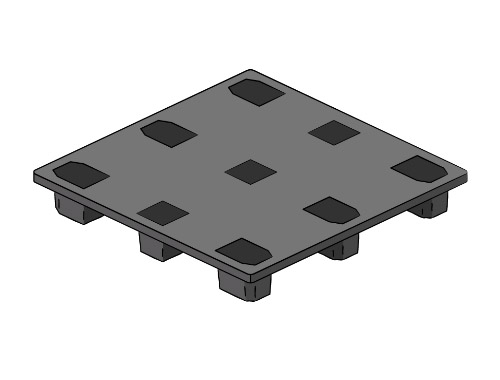
Nine-Legged Pallet: These common plastic pallets are also technically skids. Nine-legged pallets have nine evenly spaced legs instead of runners that allow the pallets to nest inside each other. The legs are formed by creating a depression in the pallet’s surface when it is manufactured.
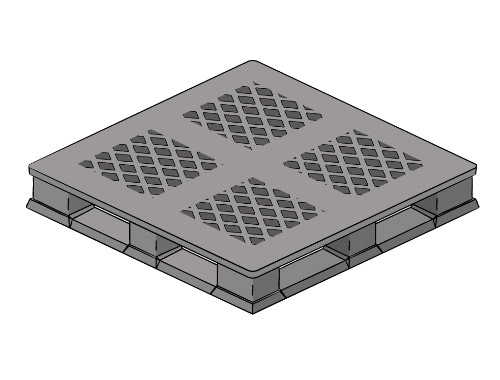
Six-Runner Pallet: Also called cruciform or picture frame pallets, six-runner pallets can be thought of as having two sets of three runners beneath the deck, which run perpendicular to each other. This strengthens the pallet, creates a partial bottom deck, and allows these plastic pallets to be racked and stacked on top of each other when they are empty or when the load beneath can support the weight of a fully loaded pallet.
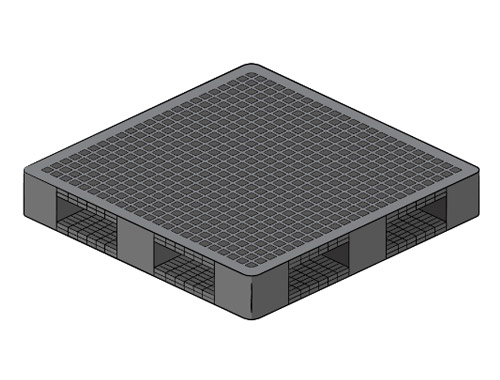
Reversible Pallets: This is a broad category of pallets that have both top and bottom decks. The bottom deck of a reversible pallet may be a full deck that is identical to the top of the pallet or it may merely have enough surface to connect the vital support points of the pallet. Six-runner and picture frame pallets are types of reversible pallets, but they are not the only types.
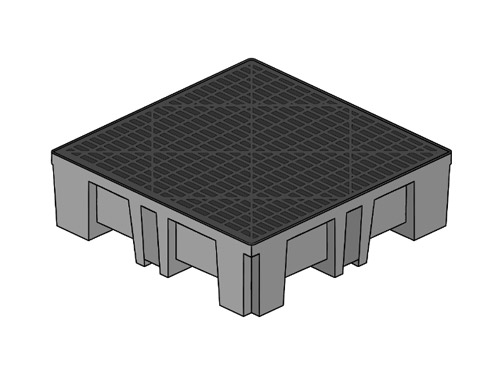
Drum Pallet: These pallets are uniquely designed to carry product that is shipped in fifty-gallon drums. Their decks often feature recesses that match the circumference of the drums and help to hold them in place. They may also have slots in the top deck that allow spills to drain into a compartment within the pallet. Their form factors vary depending on the needs of the product being shipped. Hazardous chemicals ship on pallets designed with an emphasis on containment, while dry goods like seeds or grains ship on lighter-weight drum pallets.
The form of a pallet gives it certain features. When empty and full pallets need to be carried on the same truck at the same time, a nestable pallet like the nine-legged pallet is a great advantage as empty pallets can nest within each other to take up as little room as possible. Since transportation legs from local bottling plants to local stores and back again often carry both empty and full pallets, nine-legged pallets are frequently used by the beverage industry. Features like these can protect profit margins by eliminating dead legs.
Features of Common Pallets and Skid Types
Pallet features are directly related to their form. Nestable, rackable, and stackable pallets have these characteristics because of their shape and design. Stackable plastic pallets can be stacked because they’re double-sided and are usually—but not always—edge rackable as a result as well. Due to their shape, nestable plastic pallets can’t be stacked or racked. Three-runner pallets are inexpensive and durable, but because of their two-way entry may create awkward situations where a pallet cannot be retrieved. Six-runner pallets have greater flexibility but also have a more complicated form and a higher price.
Other pallet features aren’t dependant on a pallet’s shape. How a plastic pallet is recycled and whether it is suitable for transporting food depend on the type of plastic out of which it’s made. How a type of plastic is formulated determines how well the pallet resists fire and how hot it burns. A plastic formulation is important because without additives plastic can melt and spread fire further and may require more water to suppress a fire. A majority of iGPS plastic pallets have received either UL 2335, FM 4996(1), or both fire performance ratings, demonstrating that their formulations help to prevent the spread of fire if ignited and that they exhibit burning characteristics equivalent to or better than wood. Pallet manufacturers may add other features to their pallets as well; some plastic pallets offer trackability through embedded RFID chips.
But which of these features is most important for your industry? The chart below shows which features matter most for common consumer goods industries.
(1) Gen 1 pallets(manufactured by Schoeller Arca Systems Inc.) received UL 2335 listing on July 20th, 2007 and FM Approvals 4996 listing BiPP4840 HR 6R on September 8, 2008 to September 25, 2012.
Once you’ve decided what features you need, you can use the chart below to find out which of the most commonly used plastic pallet types and sizes will support those features.
When it comes time to choose a plastic pallet, you’ll want to pick one that offers the features your particular industry needs. For instance, if your company harvests and ships fresh produce, it’s important to use a pallet that’s easy to clean and sanitize. You’ll also want to consider whether or not a pallet’s dimensions and weight function with existing equipment and storage systems used by the facilities and retailers in your supply chain. An example would be using a pallet with dimensions that fit the pallet racking at all locations through which it will travel. A pallet with a consistent handling profile that works smoothly with storage and transport equipment throughout the supply chain saves time and energy and reduces margin compression for all parties. It may also help your company cement a lasting and profitable relationship with retailers at the end of your supply chain.
A pallet management solution such as pallet pooling makes it possible to use one type of high-quality pallet throughout the supply chain. Pallet pooling services provide pallets when they are needed and arrange for their retrieval and reuse, taking the hassle out of pallet management.
Choosing the Right Plastic Pallet for Your Company
Perhaps the single most important aspect of a pallet is compatibility with existing storage and handling equipment. For example, the beverage and dairy industries use proprietary pallets because most dairies and bottling plants serve a local area. They manage their fleets of specially adapted trucks to deliver their products. However, when these same products travel through the grocery supply chain, they ship on standard CBA spec pallets so that grocery distribution centers can easily handle them. The automotive supply chain works similarly, repackaging auto parts for delivery to stores on CBA spec pallets. There is a good reason for this.
The CBA spec pallet is the preferred choice of the world’s largest economy and one of the most versatile pallets there is. It is compatible with North American and European standard racking, fits with minimal wasted space in ISO standard shipping containers, and has dimensions that are appropriately sized for everything from oil drums to automotive parts. Even in an industry with its own uniquely sized pallet, it’s likely that products will ship on CBA pallets to customers at the end of the supply chain. If your company ships to retailers in North America, then a CBA-spec plastic pallet will work seamlessly within your logistics system. For these reasons, it is the pallet size of choice for pallet pooling, and the one offered by iGPS through its pallet pooling service for companies across North America to use and reuse.
The iGPS pallet pool rents the highest quality CBA spec plastic pallets made from high-density polyethylene. They are rackable, trackable, compatible with all standard material handling equipment in North America and Europe, and accepted throughout North America. To enjoy the many benefits of a superior shipping platform compatible with nearly every supply chain worldwide, give our team a call today or email: info@igps.net.