Choosing a Hygienic Plastic Pallet for Cleanroom Applications
Many of the products that make modern life possible have exacting standards of production. The microprocessors that power the phones and computers we use every day depend on connections smaller than the human eye can see to do their calculations. A microscopic dust particle introduced in manufacturing will sever the connection and create a faulty product. The medicine that cures us when we are sick and the vaccines that keep us from becoming ill in the first place can also be ruined by minuscule amounts of foreign material.
The exacting necessities of pharmaceutical, electronics, and other cleanroom manufacturing are, of course, a logistical challenge. The manufacturing environment must remain clean, but the constant coming and going of components and products provides an avenue for contaminants to enter the cleanroom. A wood pallet that has been stacked outside on loading docks doesn’t begin to come close to meeting cleanroom pallet standards.
Cleanroom manufacturing requirements mean that many companies use a set of cleanroom pallets and then transfer loads to external pallets for shipment outside of the cleanroom. This is an interruption that slows down supply chain operations and can compromise product safety during transportation—as companies like Johnson & Johnson, Depomed, and Pfizer have discovered. Their use of wood pallets for transport caused costly recalls due to chemical contamination. Plastic shipping pallets, which do not absorb chemicals or need to be treated with pesticides, are the clear choice within a cleanroom environment and are also a safer and more hygienic solution for transporting products produced in cleanrooms to storage facilities and end retailers.
The Basics of Cleanroom Classifications
The type of cleanroom pallet you need depends on what level of cleanliness your product requires for manufacturing. There are nine levels of cleanroom designated by the International Organization of Standards (ISO). Each grade of cleanroom has set criteria for the size of particles per cubic meter allowable in the room (as measured in microns (μ) or one-millionth of a meter). The standards allow only certain amounts of particulate above a certain size. In some cases, the size rating is not applicable as a particle of that size in the cleanroom would either represent a violation or would be irrelevant. A table listing all of the ISO grade cleanrooms and their standards—giving NA when particle quantity would not apply—is included below:
* MAXIMUM PARTICLES (by cubic meter)
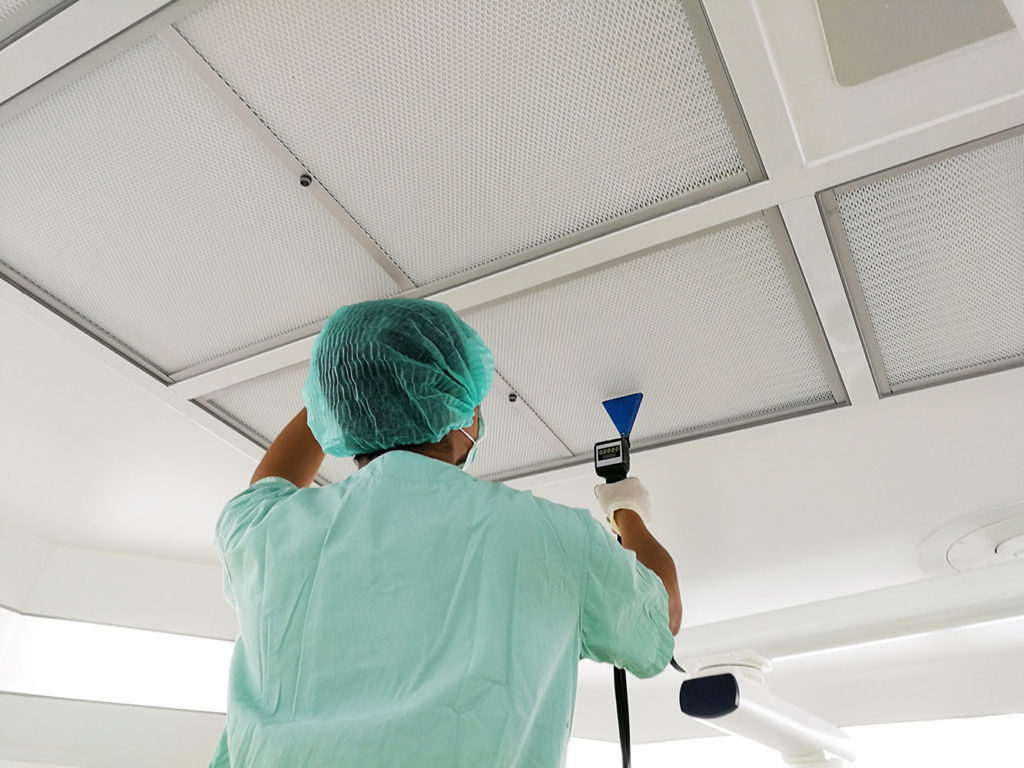
An ISO class 9 cleanroom is the equivalent of a regular room, albeit one with basic precautions such as hairnets, gloves, and lab coats. An ISO class 1 cleanroom only allows for ten particles per cubic meter. Given that human exhalation produces anywhere from 0.1 to four particles per cubic centimeter, an ISO 1 cleanroom is effectively a completely sealed environment and it is likely not feasible to bring a plastic pallet into the room. In situations like this, there must be a process to transfer products from cleanroom-only pallets onto exterior pallets in gray areas (areas that are cleaner than the uncontrolled areas outside but which don’t meet cleanroom specifications). This sort of transfer loading can be a time-consuming and cumbersome operation.
However, it isn’t necessary for all cleanrooms. ISO 6 cleanroom standards can usually be met by using hairnets, face masks, and special clothing for personnel. By washing pallets beforehand and taking other sanitization measures, it is possible to bring plastic pallets that will be used for shipping into the cleanroom itself, removing the need for transfer loading in gray areas and saving both time and money.
Cleanroom Biocontamination Protocols
None of the above ISO categories are rated for microbes. While bacteria and viruses do count as particulates and are filtered out with other particles (an ISO 5 cleanroom or above already has a significantly reduced bacteria population, and an ISO 1 cleanroom has removed some larger viruses), biocontamination is an additional level of control separate from the designation for a cleanroom under international standards.
Biological contamination protocols are listed as ISO 14698-1 and are criteria for determining a safe microbial level. Biocontamination protocols apply mainly to pharmaceutical manufacturing and to some food processing and are aimed at keeping viruses, bacteria, fungi, and chemicals out of pharmaceutical products. The actual requirements of ISO 14698-1 are non-specific and can be summed up as described below:
Identification of potential hazards to process or product, assessment of the probability of these hazards occurring, and identification of measures of control.
Designation of risk zones and determination of points, procedures, environmental conditions and operational steps that can be used to eliminate the hazards or limit the potential for them to occur.
Establishment of limits in order to maintain controls as well as the establishment of monitoring and observation to ensure controls are being implemented and are effective.
Creation of a corrective action plan to be implemented if monitoring shows that a point, procedure, or operational step is out of control.
Documentation and establishment of training procedures for all of the above.
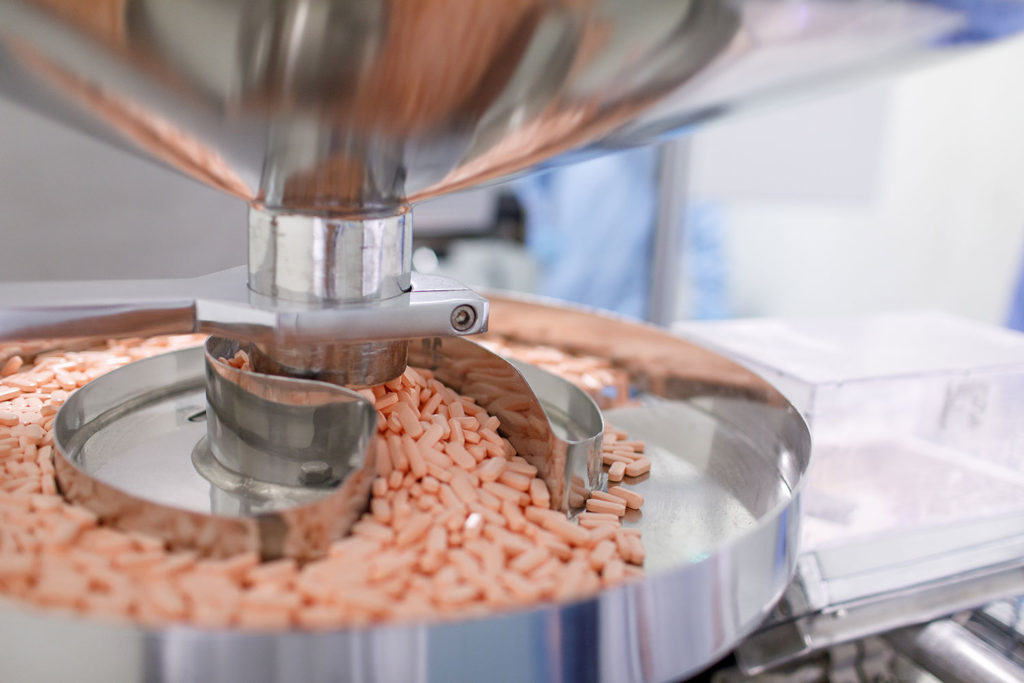
Although non-specific, these standards allow companies and organizations to tailor their cleanroom procedures in order to eliminate the biocontaminants that are of particular concern to their products. Facilities processing produce, meat, and other foods may have cleanrooms with particulate standards that are essentially the same as any other room but will have implemented procedures to remove E. coli, Listeria, salmonella, and other pathogens that can cause illness along with biocontaminants and chemicals that can render food unfit for consumption. A pharmaceutical company making vaccines, on the other hand, will have cleanroom controls that remove particulates and will also be engaged in a multistage process to keep potential pathogens out of their processing areas. Electronics manufacturers aren’t concerned about anything other than particle counts.
All three facilities, however, can benefit from choosing a high-quality plastic shipping platform for their products regardless of their cleanroom’s ISO standard level. A durable plastic pallet is more hygienic than a wood pallet and can be sanitized and kept in nearly microbe-free storage during transportation. This can make transfer loading unnecessary for some types of cleanroom and can make maintaining the sanitary standards of the cleanroom easier. Whether it is used in the cleanroom itself or in the gray areas outside of the cleanroom, a plastic pallet makes controlling both particulate and biological contaminants a much easier job.
Why Cleanroom Pallets Should Be Made of Plastic
Type | Advantages | Disadvantages |
---|---|---|
Plastic | – Non-absorbent surface – Non-conductive material – Lightweight for easy handling in cramped conditions – Available in a variety of sizes and designs – Gentle on floors and other surfaces–won’t scratch – Doesn’t conduct electricity – Can be used in an “open loop” setting outside the cleanroom | – Surface can be scratched and material can accumulate in scratches – May have hollow areas that can retain particulates unless proper procedures are followed |
Aluminum | – Very lightweight – Very strong for its weight – Additional coatings can be applied by electroplating to make it even smoother and more hygienic | – Very expensive – If dropped or damaged, pallets can’t be quickly replaced or repaired – Due to cost, aluminum pallets are generally for internal use only and require transfer loading – Conductive to electricity – If coating is damaged during use, corroding aluminum may create a source of particulate in the cleanroom |
Stainless Steel | – No additional coatings are needed overtop stainless steel – More durable than aluminum, plastic, and nearly any other pallet material | – Like aluminum, stainless steel pallets are very expensive – Extremely heavy – Strictly for internal use–transfer loading is required – Conductive to electricity – May scratch or damage floors |
Plastic pallets are standard for use in cleanrooms. They offer advantages over any other type of pallet in a controlled environment, particularly wood. Wood pallets absorb moisture, including chemicals and other contaminants, and damp wood pallets create a friendly environment for bacteria, mold, and mildew. Wood pallets also create particulate contamination in the form of sawdust, splinters, and other wood debris. Add to these issues the fact that wood pallets are nearly impossible to thoroughly clean and it’s clear that wood pallets are unsuitable for cleanroom use. Other materials, such as metal, are occasionally used to make cleanroom pallets but tend to be appropriate only for specific niche applications.
Plastic pallets are the clear choice both for cleanrooms and for shipping products produced in them. Plastic is both nonabsorbent and easy to clean and sanitize, and high-quality plastic pallets have a unitized construction that prevents the splintering and fragmentation seen in wood pallets. This makes plastic pallets an excellent choice for use in a cleanroom and for reducing the particulate level in adjacent gray areas and the supply chain as a whole.
Using the iGPS Pooled Plastic Pallet in Your Cleanroom
The type of plastic pallet you choose for your cleanroom will depend on your cleanroom’s classification. Some cleanrooms will require a plastic pallet with an entirely solid deck, but the majority of cleanroom environments merely demand a durable plastic pallet that’s easy to clean. The iGPS plastic pallet is a perfect fit for this type of cleanroom, offering:
Unitized Construction
The iGPS plastic pallet is a fused whole with no individual boards that can pull free and it does not create or leave behind sawdust, splinters, or nails.
Washable
Since plastic pallets are nonabsorbent, they can be washed and dried thoroughly using a power washer or automated pallet washing machine. Any particles or debris that a pallet may pick up during processes or transportation can be removed this way, making the pallet safe for use within the cleanroom and outside of it.
Sanitizable
iGPS plastic pallets can be rendered a step beyond clean by contracting with a third-party sanitization service. Generally, this process kills more than 96 percent of microbes on the pallets and keeps them sanitized while they are transported to their end user.
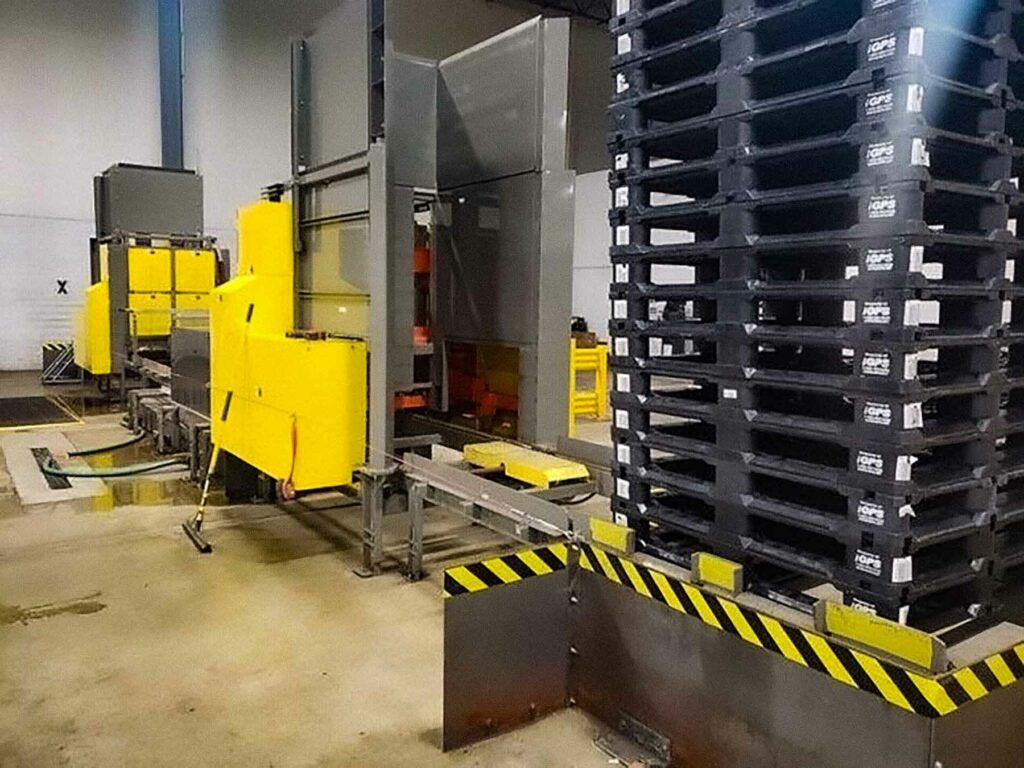
Since the iGPS pallet complies with standard Consumer Brands Association (formerly GMA) pallet specifications and can be stacked, racked in a warehouse, and shipped to end retailers, companies that use the iGPS plastic pallet in their cleanrooms can avoid transferring their products from cleanroom pallets to shipping pallets. The result is an efficiency gain that reduces your company’s Total Cost of Business (TCOB) and creates savings that can add up substantially over time.
Whether or not you choose to use iGPS pallets in your cleanroom, choosing to ship on iGPS plastic pallets rather than wood platforms also has many advantages. Transferring products to a hygienic iGPS plastic pallet in the gray area transition zone reduces the potential for particulate or biological contamination to find its way into the area. In turn, this reduces the likelihood that contaminants will find their way into the actual cleanroom. Transporting your product on plastic pallets also keeps your products safer during their journey to the end retailer by reducing instances of product damage, contamination, pest infestation, and pallet failure.
The goal of a cleanroom is to reduce or eliminate particulates that could render your products unsafe or inoperable. Choosing the hygienic iGPS plastic pallet as a cleanroom pallet or to transport product outside the cleanroom is a smart choice that supports your supply chain processes and ultimately lowers your Total Cost of Business (TCOB).
iGPS Logistics
Is the market leader in plastic pallet pooling.
Provides pallets compliant with Consumer Brands Association (CBA) specs.
Provides an industrial-strength pallet that is both durable and hygienic.