Shipping pallets make it possible to quickly deliver products in the volume needed for modern life. Reducing the weight of these platforms has countless benefits, including lowering the fuel cost of transporting products and allowing the delivery of more products with every load.
Lightweight plastic pallets from the iGPS pallet pool offer companies substantial weight savings over traditional wood pallets, which can improve efficiency on every leg of a company’s supply chain. Lightweight pallets that allow businesses to ship more products per truckload can reduce the number of trips that need to be made to meet demand, and, over time, those savings add up to reduce your Total Cost of Business.
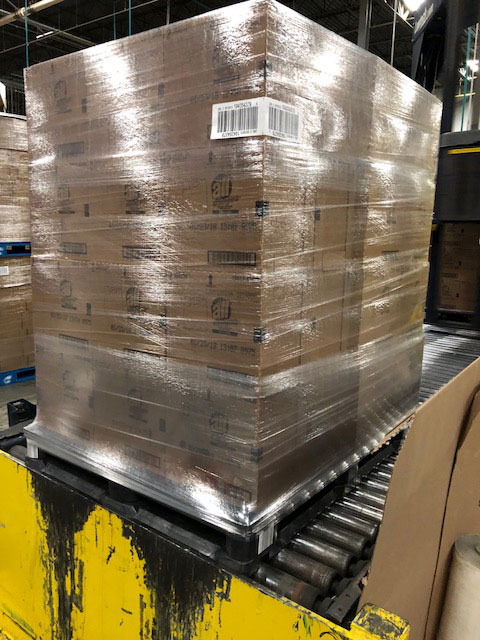
The Problem with Heavy Wood Pallets
The most basic wood pallet—the stringer pallet—is actually fairly lightweight, but it comes at the cost of being flimsy. Stringer pallets are made of half-inch thick boards nailed to three two-by-fours, and the boards can pull loose or break when handled by a forklift, and this can result in product damage. To better protect products during transport, the shipping industry started using a more robust block pallet. It uses nine four-by-four-inch blocks instead of stringers, adds more deck boards, and uses more nails to hold the pallet together. Block pallets are much sturdier than stringer pallets, but they have a trade-off: they weigh significantly more, and their weight can increase under certain environmental conditions. Wood is an absorbent material and wet wood block pallets can weigh up to 80 pounds. A 53-foot trailer holds about 26 pallets; block pallets may make up as much as 2,000 pounds of its weight—a full ton. If a trailer is cubed out and filled vertically, pallets may make up an even greater proportion of the weight of the load.
Shipping pallets are necessary to move and store products on their way to the retailer or end consumer, and supply chains would struggle to meet demand without them. However, unlike the products that pallets carry, pallets themselves cannot be sold for profit. Extra energy spent moving pallet weight is an additional cost that doesn’t offer a return. Reducing a shipment’s weight saves on the fuel costs needed to transport it, and reducing the portion of that weight that is attributed to pallets maximizes profits.
How Lightweight Plastic Pallets Save Weight and Money
The lightweight iGPS plastic pallet is an alternative to the block pallet that weighs around 50 pounds. This translates to a weight savings of approximately 700 pounds on a single layer trailer load and about 1,400 pounds on a trailer that cubes out. Removing extra weight on loads that weigh out is the best way to maximize profits, and it can reduce fuel mileage for loads that cube out. Reducing energy use and carbon dioxide emissions is good for business and good for the environment as well.
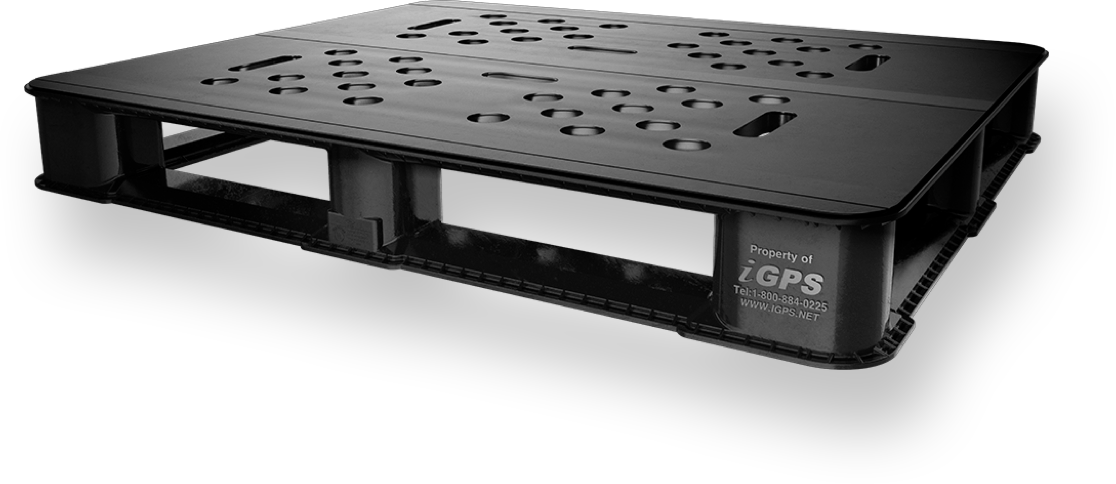
Evenly distributed, an iGPS plastic pallet can support up to 30,000 pounds of static load, 5,000 pounds of dynamic load, and 2,800 pounds in a warehouse racking system. In fact, their edge-rackable load limitations have more to do with the strength of racking designed for wood pallets than the strength of an iGPS plastic pallet. One of iGPS’ rugged CBA-spec plastic pallets can even make 100+ trips through the supply chain, a long lifespan compared to a wood stringer pallet’s three-trip maximum or a wood block pallet’s 15-20 trip lifespan. Compared with wood pallets, lightweight plastic pallets can offer these benefits:
- Uniformity: Lightweight plastic pallets are manufactured to uniform dimensions. This means they are consistent in both size and weight. Since plastic is non-absorbent, plastic pallets will remain stable in both weight and dimensions across most environments in the supply chain.
- Automation Friendly: The uniform construction of plastic pallets makes them easy for warehouse automation like Automated Storage and Retrieval Systems (ASRS) and Autonomous Guided Vehicles (AGVs) to handle.
- Recyclability: When an iGPS plastic pallet is at the end of its lifespan, it can be directly recycled into “new” plastic pallets. This reduces the need to extract and transport resources just to replace a used pallet and keeps plastic pallets out of landfills, making them part of a closed-loop supply chain system.
- Hygiene: Due to the nonabsorbent nature of lightweight plastic pallets, they are less likely to be colonized by bacteria and can be easily cleaned by a wipedown or even fully sanitized for use in a cleanroom facility.
The efficiencies that lightweight plastic pallets bring to the supply chain result in substantial savings over time and these benefits can be further optimized through pallet pooling.
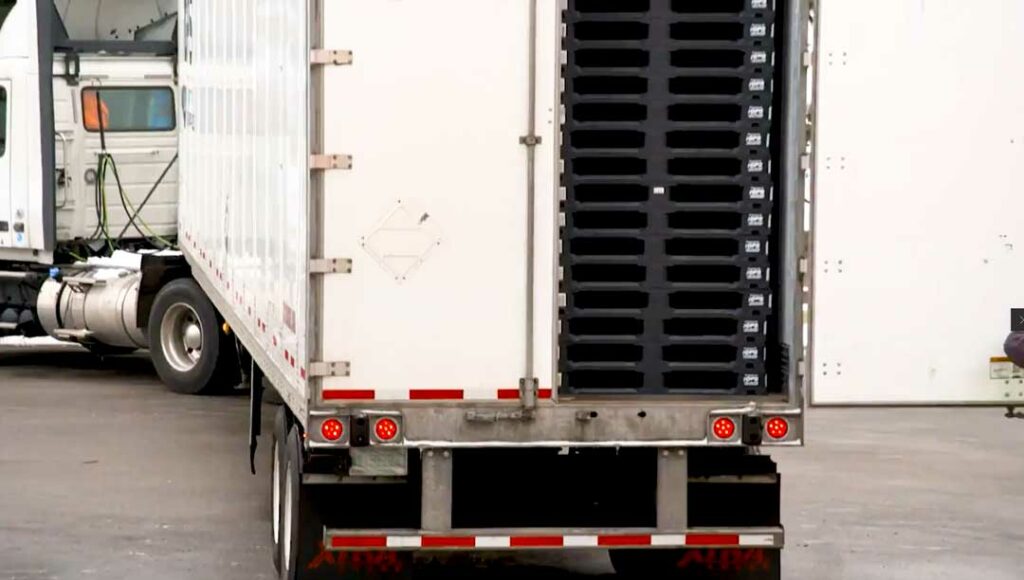
Why Choose Lightweight Plastic Pallet Pooling?
Pallet pooling allows businesses to avoid the hassle of procuring and managing an internal inventory of pallets. Instead, pooled pallets are provided by a company whose customers draw the pallets they need from a shared pool. Since this network of customers stretches nationwide, pallet pooling keeps pallets in near-constant use and optimizes their transportation, reducing empty transportation legs. The robust nature of pooled lightweight plastic pallets also means they undergo less damage and require fewer repairs than wood pallets, minimizing the warehouse space needed to inspect and sort pallets. Since plastic pallets remain in good shape and don’t absorb moisture, they can be sent directly from the receiver who unloads them to a nearby product manufacturer to be loaded with goods after just a simple wipe-down.
The iGPS pallet pool offers lightweight plastic pallets made of food-safe, temperature-stable, durable HDPE plastic. With a nationwide network of depots, the iGPS lightweight plastic pallet pool provides a superior shipping platform that helps to reduce the weight of product loads, improve supply chain efficiency, reduce operational costs, and lower greenhouse gas emissions. Over time, switching to iGPS pooled plastic pallets can reduce your Total Cost of Business and protect your company’s profits.