Plastic Pallet Pooling Benefits for
Pharmaceuticals
Pharmaceuticals are a modern miracle. Ethical pharma, i.e. drugs available with written instructions from a doctor or dentist, have made it possible for billions of people to live healthier, happier, longer lives. And, thanks to the pharma supply chain, it’s possible to make life-saving medicines accessible whenever—and wherever—patients and doctors need them most.
In that way, the pharma supply chain is a kind of modern miracle as well. Pharmaceuticals are made by manufacturers, travel to wholesale distributors, and are then stocked at retail stores and pharmacies before making it into the hands of patients. It’s a highly efficient process that saves lives—if you have the right technology at your disposal.
Medical products are indispensable; pharma manufacturers have a big responsibility to the public. Should pharmaceutical companies fail to deliver products in a timely manner or ship medicines that are contaminated or expired, the consequences can be extremely serious, for patients and the pharmaceutical industry.
Is there a supply chain solution that can give patients and ethical pharma companies the assurances and reliability they demand? The answer is yes. The answer is the iGPS plastic pallet pooling system.
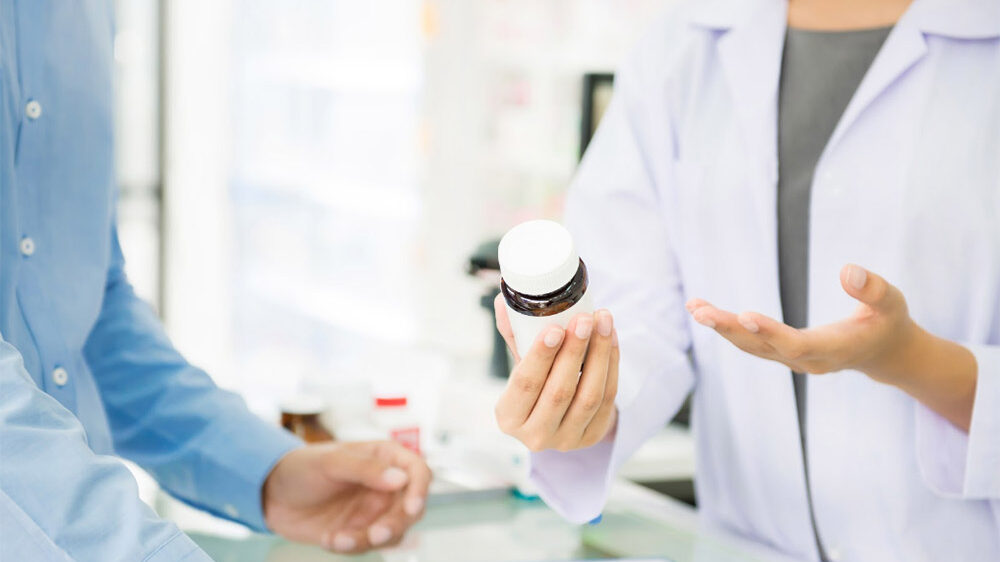
Delivering Miracles: Why Shipping Pharmaceuticals Is a Big Responsibility
Everyone in the pharmaceutical industry is aware that wood shipping pallets have been behind some of the biggest medical recalls in history. The McNeil Consumer Healthcare recall of Tylenol tablets that began in December of 2009 is a prime example. Consumers reported that the product had an unusual odor and that they experienced unpleasant gastrointestinal symptoms when consumed. The products were found to have trace amounts of a chemical called 2,4,6-tribromoanisole (TBA)—a chemical used to treat wood pallets.
The contaminated pallets originated in the Dominican Republic before being shipped to the United States. They had been treated with a fungicide that degraded into TBA, which contaminated containers and the products. By the time the recall ended, over 54 million bottles of Tylenol were recalled. Johnson & Johnson reported losses of $900 million in 2010 due to the recall, according to the Wall Street Journal, as well as diminished public trust.
The vulnerability of wood pallets to contamination is not the only challenge facing the ethical pharma supply chain, though. Biologics must be stored at colder-than-average temperatures at every point along their journey to consumers. This increased demand for cold chain logistics raises expenses and lowers profit margins as these unique cooling requirements result in exceedingly high inventory costs.
The pharma shipping industry must pay particular attention to the pallets that pharmaceutical products are exposed to. They must be hygienic, support increasingly long supply chains, and help to lower pharma’s Total Cost of Business (TCOB).
The iGPS plastic pallet pooling system provides the technology and service that can meet those goals. To get started with iGPS, reach out to our logistics experts today at 1-800-884-0225 or email us at info@igps.net. Our team will walk you through how our innovative shipping options can drastically lower your total cost of business.
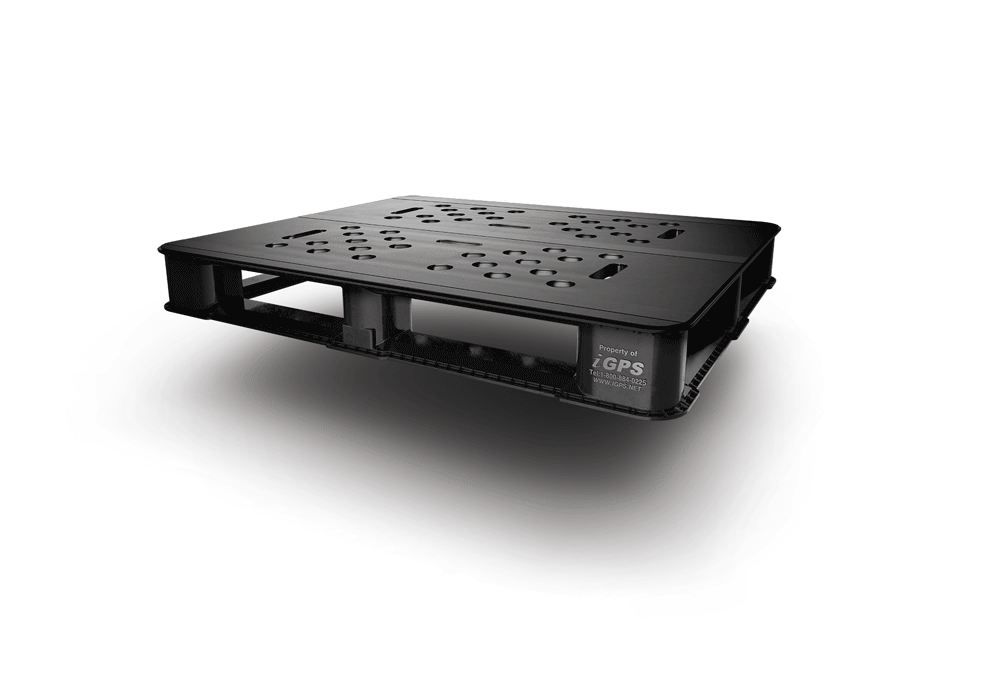
Ethical Pharma Shipping with the iGPS Plastic Pallet
The seven top competitive advantages that iGPS plastic pallets offer the ethical pharma industry are:
- Unprecedented Safety and Hygiene: It’s imperative that pharmaceuticals are shipped on plastic pallets that do not require chemical treatments of pesticides or fungicides. Wood pallets harbor bacteria, fungus, and pests. Plastic pallets are impervious to parasites and do not require the preventative measures of chemical treatment. They will not rot or absorb moisture.
- Lower Transportation Costs: Biologics kept on dry ice can be heavy loads, but iGPS plastic pallets help reduce your shipments’ total weight. At around 50 pounds, iGPS platforms are up to 35% lighter than standard wooden pallets. The result is lower costs when transporting your products from the warehouse to the retailer.
- Reduced Product Damage: Pharmaceutical cargo will be rejected by the retailer if it has been punctured or damaged as environmental exposure can lead to contamination. The iGPS plastic pallet is sturdy, uniform, and has no protruding edges or parts, reducing the chance that your packaged products will be damaged during transport. Additionally, iGPS plastic pallets for pharmaceuticals can stand up to cold packs or dry ice of temperatures as low as -109.3 degrees Fahrenheit without cracking or breaking.
- Increased Automation: Pharma manufacturers must ship products on hygienic pallets compatible with the automated systems used by many vendors. The iGPS plastic pallet is ideal for automated systems as each is a standard 48 x 40 inches in dimension. Its uniform design will not cause errors in automated systems and eliminates unwanted product overhang. Shrinkage and warping are also not a concern with iGPS platforms, ensuring compatibility with automated guided vehicle (AGV) technology.
- Industry-Leading Sustainability: Part of ethical pharma’s commitment to consumers is delivering products via a greener supply chain. iGPS plastic pallets eliminate the need for wood platforms, reducing the industry’s consumption of trees, and are reusable and recyclable. They also require less fuel to transport, which reduces carbon emissions during transit. To estimate the amount of carbon emissions iGPS plastic pallets can reduce for each of your shipments, try our greenhouse gas calculator.
- Superior Worker Safety: The iGPS plastic pallet is safer for employees to work with than wood pallets, making handling pallets easier. Durable plastic eliminates gaps, broken boards, protruding nails, and splinters that can injure warehouse workers. The lightweight feature of the iGPS pallet also means a single worker is able to lift individual pallets.
- Efficiency via a Pooling System: Renting, versus buying, a fleet of sustainable, hygienic, durable pallets means your logistics energies are spent more efficiently than if you were to try to maintain and manage an in-house fleet of shipping pallets.
How the iGPS Plastic Pallet Pooling System Works
How does the iGPS plastic pallet pooling system work? iGPS delivers quality pallets, on time, as required by the manufacturer. The manufacturer then ships it’s products on the pallets to their distributors, who may store the products in warehouses or may immediately ship them out to grocery retailers throughout North America.
Once the pallets have been unloaded at a retail outlet, iGPS arranges for the return of the empty pallets back to one of their many depots throughout North America for inspection, cleaning, and, if required, repair. They are then reissued to another manufacturing customer. The iGPS pallet pooling system is seamless, easy, cost-effective, and ensures that operations run more smoothly for its ethical pharma clients.
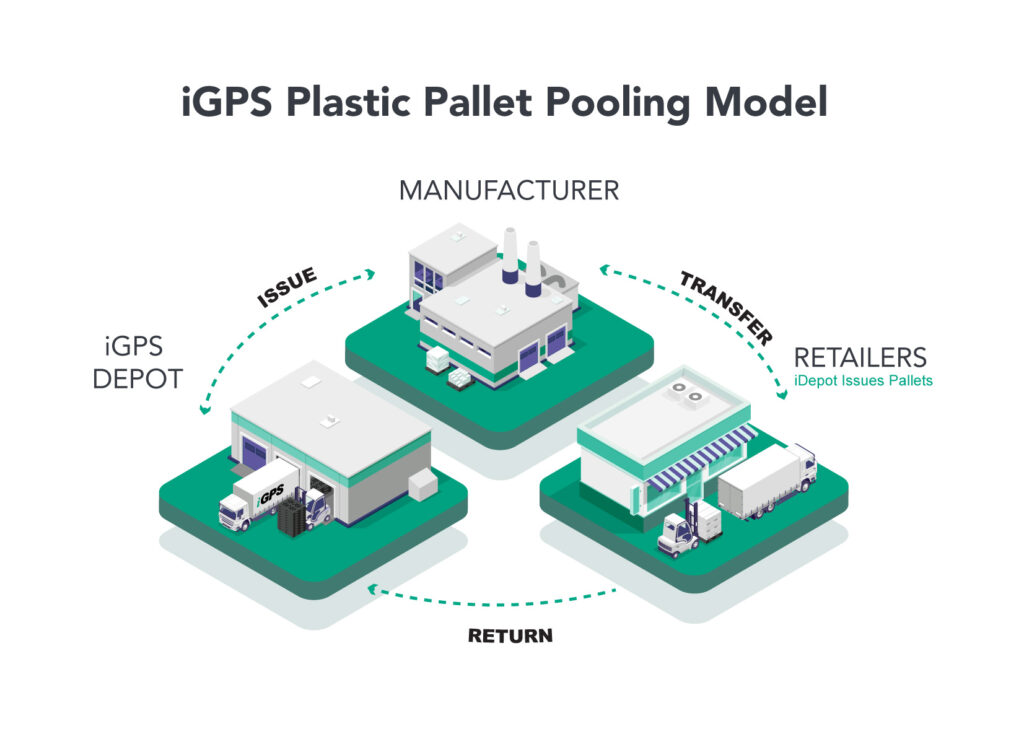
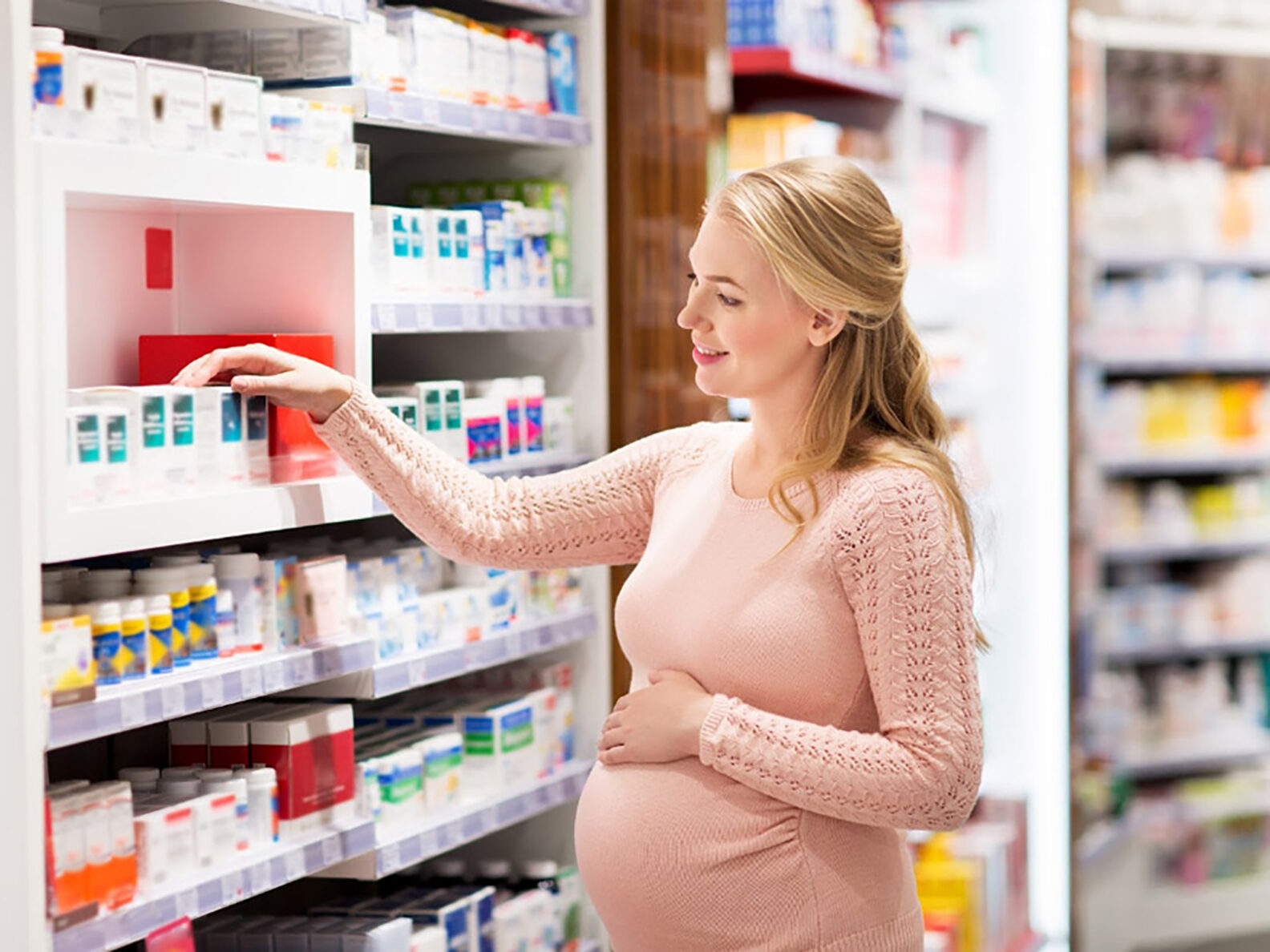
Inoculate Your Supply Chain from Contamination Risks with iGPS
Plastic pallets for the pharmaceutical industry offer manufacturers, retailers, and consumers alike an extra layer of protection from potential product contamination crises. And, the iGPS plastic pallet pooling system makes your supply chain more efficient, which in turn makes deliveries more reliable and lowers your TCOB.
Only iGPS Plastic Pallets:
Are sanitary enough for bagged lettuce but strong enough for bagged concrete.
Allow you to easily track shipments through RFID technology.
Meet the highest standards of platform hygiene, according to the FDA’s Food Safety Modernization Act.
Are compliant with Consumer Brand Association (CBA) specs.
Ethical pharma manufacturers and retailers are the bedrock of the healthcare industry, giving doctors and pharmacists the medications and products they need to save lives. Patients are counting on you. Make sure you come through for them with help from iGPS. Empower your supply chain—while lowering your TCOB—with the iGPS plastic pallet pooling system.