In September 2018, an annual survey by Modern Materials Handling of companies using pallets to ship their goods revealed that the price of pallets is a top factor for CEOs and logistics managers shopping for pallets. This isn’t a surprise at all, of course; the cost per unit of a pallet has been the biggest worry of most logistics decision makers for as long as anyone has been keeping track. What did come as a surprise to many was that pallet strength finally tied with cost as the most important factor in pallet decision making for those surveyed.
Supply chain trends are part of the reason for this. Logistics systems are getting more efficient and relying on ever greater levels of automation. As a result, tolerances are tightening. Cheap but flimsy used wood pallets cause downtime and expensive machinery damage if they come apart in an Automated Storage and Retrieval System (ASRS) or palletizer. Strong plastic pallets are more durable than wood pallets of any kind and ideal for the automated systems and high storage racks that maximize efficiency in modern logistics systems.
How Cheap Wood Pallets Cost You Money
A single-use stringer pallet may at first seem like the least expensive pallet option, but is more expensive in the long run. These pallets are simply deck boards nailed to two-by-fours with notches cut out to allow forklift access. There isn’t a lot of material giving these pallets their strength, and while they can support a surprising amount of weight, they can’t do so over and over again. They are built for a single use and are capable of only two or three trips through the supply chain before they need repair or retirement.
However, since second-hand or repaired stringer pallets are cheaper than new ones, management may decide that used pallets make the most cost-effective choice. Warehouse personnel must then deal with the reliability issues and interruptions that arise from these used pallets. In other words, while their initial purchase price is low, a more holistic consideration of the costs of single-use pallets reveals that they tend to increase the total cost of doing business.
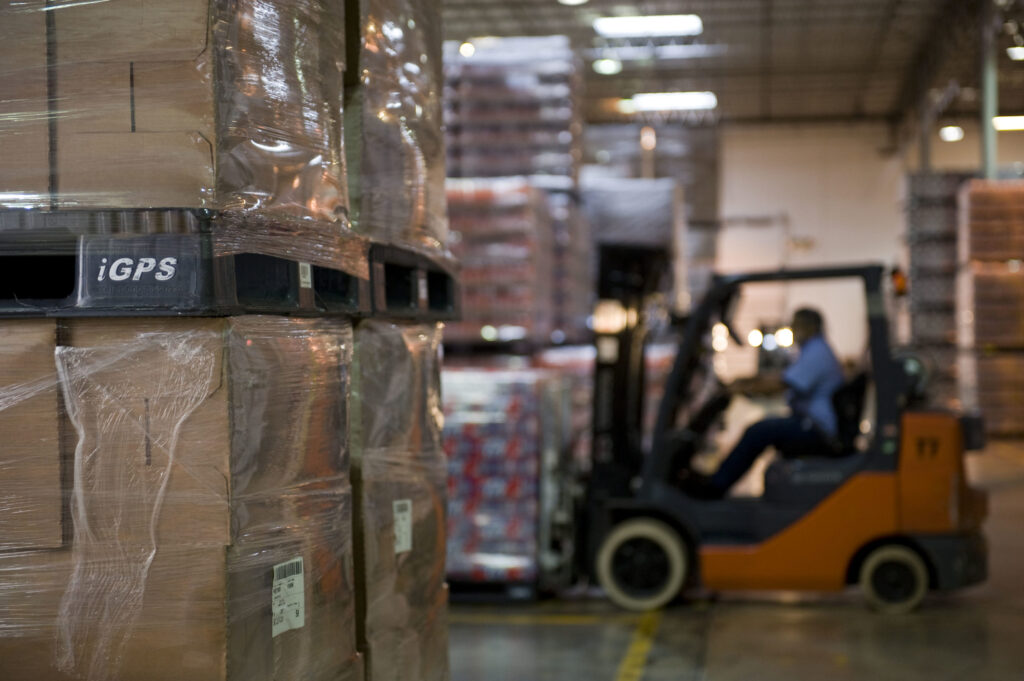
Strong Plastic Pallets Lower Your Total Cost of Business
The upfront purchase price for a wood stringer pallet may be low, but the costs of downtime, product damage in transportation or storage, and load rejection can add up. Then there are the costs of procuring pallets to replace used ones, issues with debris from broken pallets contaminating loads, and employee safety concerns due to loose pieces of wood and nails. When these things are taken into consideration, cheap wood pallets look much more expensive than their basic sticker price.
Something as simple as a broken board or a loose nail can bring an automated warehouse–with its cranes, conveyor belts, palletizers, pallet moles, and automated guided vehicles–to a halt. The resulting downtime can wreak havoc on delivery timetables, and if the warehouse’s goods are perishable or temperature sensitive, then a delay might even require whole batches of product to be discarded.
A strong plastic pallet is less likely to cause interruptions because of its unified design and construction. It lacks boards that can splinter or come loose and nails that can catch in machinery. While strong plastic pallets will cost more upfront than wood pallets, their greater safety and efficiency will lower your Total Cost of Business (TCOB) by saving you money on your warehouse operations and transportation and by supporting your reputation as a good partner to retailers.
The Benefits of Strong Plastic Pallets
The disadvantages of stringer pallets are obvious enough that many supply chains have opted for a stronger wood block pallet that can be reused three or four times before needing repair. While they are stronger than stringer pallets, like any wood pallet they are still subject to wear with use and still cause the same issues with breakages, inconsistent weight/shape, machinery jams, and loose nails as stringer pallets do. After all, they’re still made from the same material as their flimsier cousin. And, like single-use wood pallets, wood block pallets gradually lose strength with each use. A plastic pallet, on the other hand, is as strong on its twentieth or fiftieth trip is as it was on its first trip through the supply chain. Plastic pallets have other advantages over wood block pallets as well:
- Improved Sanitation: Plastic pallets are more hygienic than wood as they don’t absorb moisture or chemicals from their surroundings and are easily cleaned to reduce microbe levels on their surface. They stay odor-free and don’t provide an easy vector for contamination.
- Lighter Weight: A high-quality plastic pallet weighs around fifty pounds, comparable to a stringer pallet’s weight and far less than a wood block pallet’s usual weight of around 65 – 75 pounds.
- Durable Unitized Construction: Plastic pallets don’t use nails that can pull free and damage equipment or injure employees. Since they aren’t composed of individual boards, either, they won’t easily crack or leave behind debris in the warehouse.
- Automation Friendly: Plastic pallets are uniform in size, shape, and weight, making them ideal for use with automated equipment.
All of these advantages make strong plastic pallets an ideal fit for the modern supply chain. Today’s sophisticated logistics systems require equipment with a high level of reliability to operate at peak efficiency, and plastic pallets offer this reliability along with many other advantages.
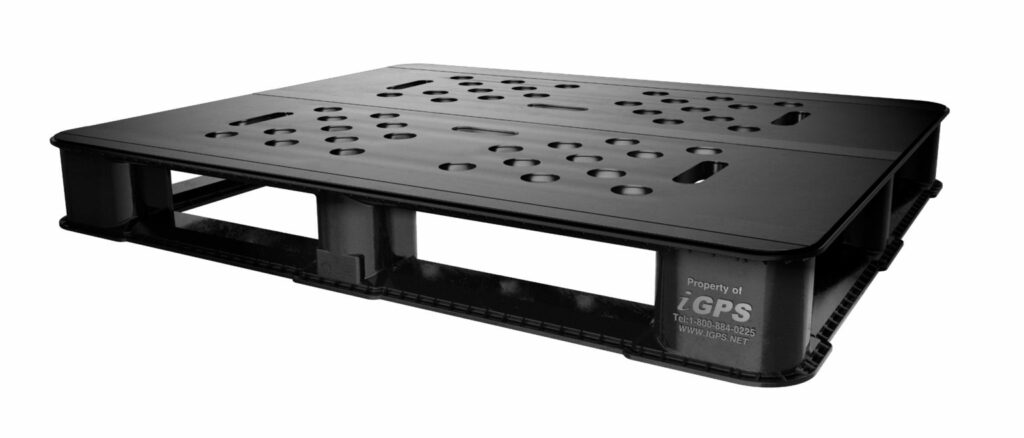
How to Find Tough Plastic Pallets
When choosing a plastic pallet, pick one that matches strength and durability with intelligent design. iGPS’ strong plastic pallets can support a static load of 30,000 pounds when evenly distributed and a 5,000-pound dynamic load when in motion. In contrast, a stringer or wood block pallet’s load rating usually falls around the 2,000 pound mark
iGPS plastic pallets can be expected to make 100+ ACTUAL trips through the supply chain in their lifespan due to their incredible durability. One-way pallet manufacturers state how many trips their pallets can make in a LAB ENVIRONMENT which is nothing like the real stresses, misuses, and abuse pallets must withstand in the supply chain.
The iGPS plastic pallet also incorporates intelligent design to increase durability and minimize pallet damage with use. Chamfered edges on the bottom deck of the pallet and forklift notches with rounded edges help guide pallet jacks and forklifts into the fork openings to help prevent damage to the forklift or to the pallet. iGPS pallets are made of sturdy HDPE plastic that bends before it breaks, so it’s resilient in a rough-and-tumble warehouse. To save on your Total Cost of Business, choose strong, light, and uniform iGPS plastic pallets.