A guide to top
Grocery Chain Pallet Requirements
Food manufacturers know the cost of a bad pallet. If a load of their products arrives at a retailer on a platform determined to be unacceptable in quality, manufacturers can expect fines from the retailer of anywhere from $5 to $25 per pallet. In some cases, the entire load may be rejected, resulting in thousands of dollars in lost products and wasted time. However, different retailers have different understandings of what constitutes a “bad pallet.” Understanding the top grocery chain pallet requirements makes it possible to minimize the risks associated with inadequate shipping platforms.
While the Consumer Brands Association (formally the Grocery Manufacturer Association) standards are a good place to start when it comes to breaking down what retailers are looking for, in many cases, the unique requirements of specific grocery chains will be much more stringent. That’s because a poorly packed pallet or one in poor repair can be indicative of damaged products and even potential contamination. And, as grocery retailers follow in the footsteps of warehouses and distribution centers by implementing automation, damaged pallets pose yet another risk because they threaten to jam and even damage automated systems. By establishing strict pallet standards, major grocery chains reduce the likelihood that they will accept unsuitable loads of products that could put their customers, employees, and equipment at risk.
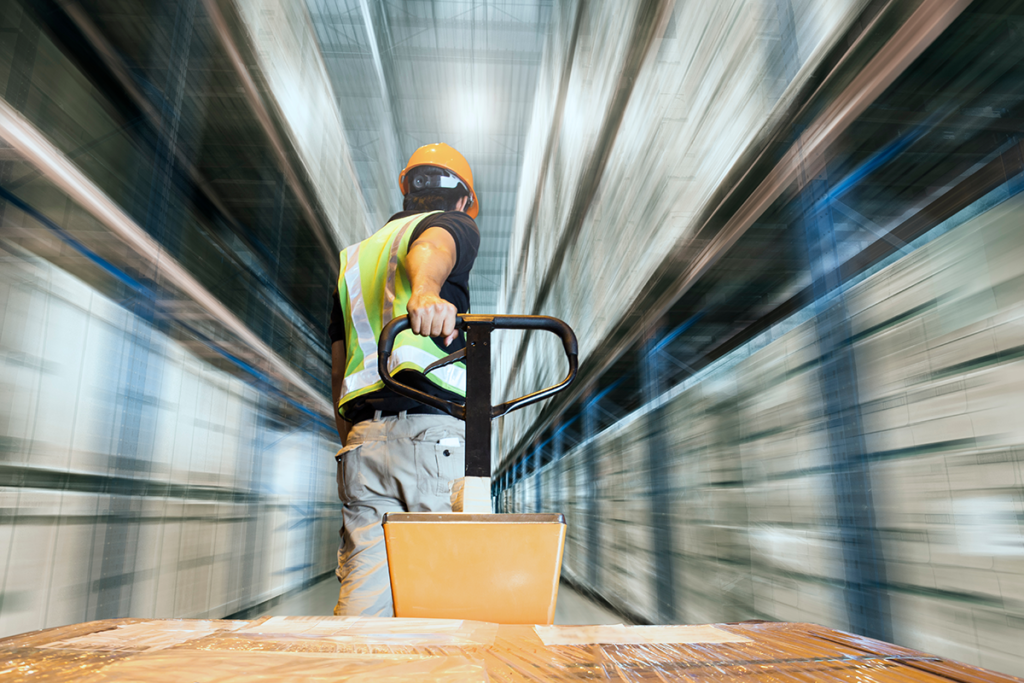
Basic CBA Pallet Specifications and Grades
Most retailers and grocers follow the Consumer Brands Association (CBA) recommendations for pallets and will not accept loads on platforms that don’t meet at least these basic criteria. The standards set requirements for the sizing and capacity of pallets, among other details. CBA pallets meet the following criteria:
- 48 by 40-inch footprint
- Four-way forklift entry
- Load-bearing capacity of at least 2,500 pounds
- Top and bottom deck boards that are ⅝-inch thick
CBA wood pallets are also graded based on their state of repair. They will fall into one of three categories.
Grade A
Grade A pallets are typically brand new and have not had any prior repairs, nor do they require any. Some pallets in this category may also fall into an even higher tier, where they’re suitable for in-store displays.
Grade B
This category of pallets likely has had some minor repairs, like board replacements, plates, or plugs. However, they remain structurally sound and are still useful for most supply chain purposes, aside from display.
Grade C
This grade of pallets includes those that have obvious defects and have received extensive repairs. There is a high risk of failure in these pallets, which is why it’s typically not wise to use them for shipping.
Just because a pallet meets CBA specifications does not mean it will automatically be accepted by the retailer. Grocery chains are wary of accepting any pallets that look as though they might have caused product damage or could harm employees handling them. Moreover, every major grocery chain has its own specific set of criteria.
Individual Grocery Chain Pallet Requirements
Along with requiring the use of CBA pallets, most major grocers will have their own specific criteria for accepting shipments from vendors. These requirements arise from internal protocols, as well as the types of technology used by each chain. We have compiled the list below for easy access but still encourage all vendors to contact the specific company for verification of their pallet requirements.
Pallet dimensions must not exceed 48 by 40 inches. Any general delivery pallets not rented from iGPS, PECO, or CHEP must be pre-approved. Pallets holding less than 750 pounds must withstand up to 1500 pounds of weight on the bottom layer, while those holding more than 750 pounds must be able to withstand 2500 pounds. The maximum allowable pallet load height is 58 inches and all loads must be stretch-wrapped at least three times.
Pallets must be 48 by 40 inches and meet or exceed Grade A CBA standards. Deck coverage must be 63 percent on the top and 47 percent on the bottom. If there are visible cracks on the top or bottom boards, they must be no more than ⅛-inch wide and 15 inches long.
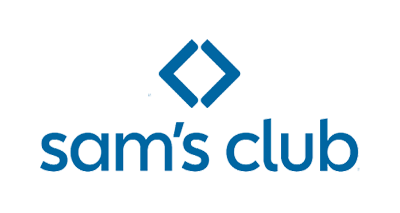
Sam’s Club pallet requirements call for a Grade-A, 48-by-40-inch, true 9-block pallet that meets strict CBA specifications and allows for four-way forklift entry. Sam’s Club specifically requires pallets from approved pooling providers (iGPS, CHEP, PECO, or RM2) with solid, unpatched blocks and boards that are clean, intact, and free from repairs, damage, or overhang.
Kroger requires 48 by 40-inch four-way block pallets from a pallet pooler or pallets with a Grade A rating. iGPS, CHEP, and PECO are all accepted by this chain. International pallets must meet similar criteria and also require a heat treatment marking.
Incoming pallets must be 48 by 40 inches with four-way entry and pallets with broken stringers or repairs, such as metal plate patches, will be rejected. Wood pallets must be hardwood; softwoods such as pine, cedar, and spruce are not accepted. Pooled pallets should belong to CHEP, PECO, or iGPS rental pools.
BJ’s requires four-way entry 48-by-40-inch pallets in excellent repair. iGPS, PECO, and CHEP are all approved rental pallet vendors. Wood pallets must be free of broken or cracked boards, splinters, or loose hardware and be fumigated before entering BJ’s supply chain.
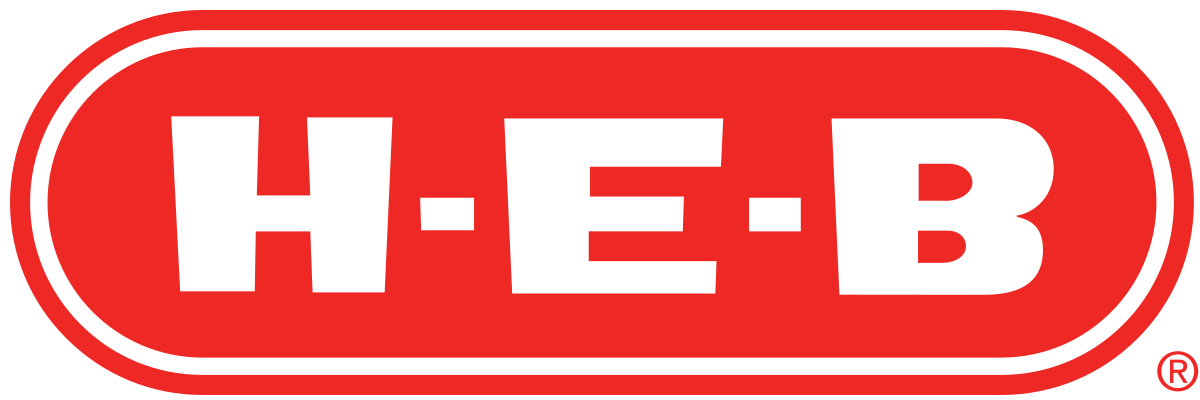
Texas grocery chain H-E-B requires a 48-by-40-inch four-way pallet made of hardwood. The pallet must be reasonably clean and free of stains from petroleum or unknown substances. It must not have broken stringers or stringers with plates covering vertical splits.
Albertsons requires a 48-by-40-inch CBA specification pallet with three stringers, seven top deck boards, and five bottom deck boards present without loose boards, soiling, or obvious repairs. Albertsons will assess fees for noncompliance and for the repalletizing of a load shipped on non-compliant pallets.
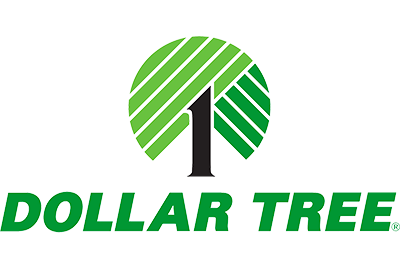
Dollar Tree pallet requirements call for a Grade-A, 48-by-40-inch CBA-specification pallet with four-way entry. Dollar Tree specifically requires three-stringer pallets with stringers that are unpatched, unblocked, and in good condition.
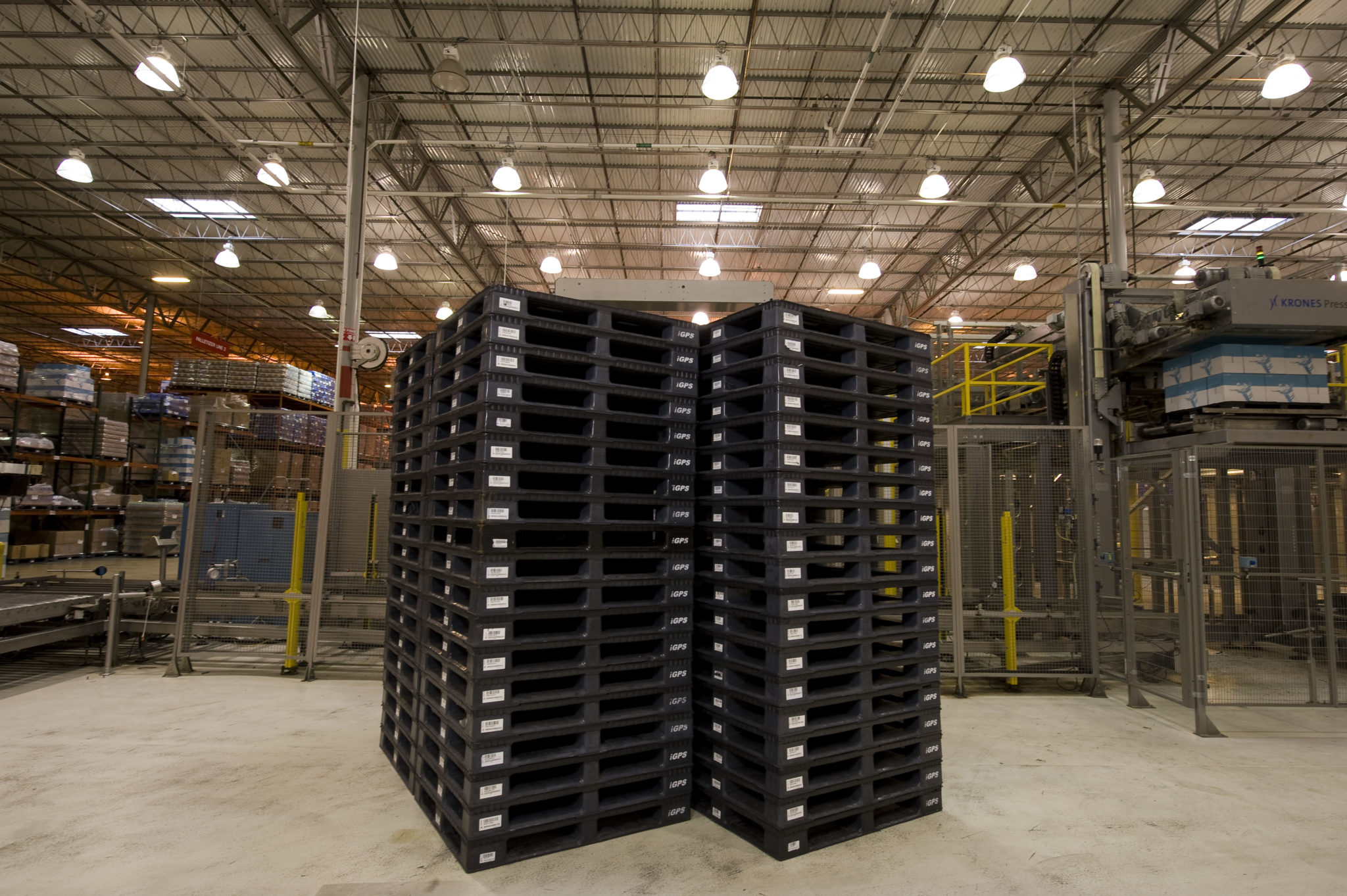
Why Many Grocery Chains Prefer Plastic Pallets
Wood pallets have traditionally been used to ship food products simply because, for a long time, wood was the only option. Now that other pallet materials are available, plastic pallets are not only accepted but they are often specified in grocery chain pallet requirements as being preferred. One reason is that plastic pallets are more durable than wood and rarely show significant damage. As a result, they don’t need to be categorized by grade like wood pallets.
As well as being more durable, plastic pallets are also non-porous. Since they don’t absorb moisture, it’s easier to keep them clean of spills that might contaminate their product load. Their lack of absorbency makes plastic pallets more hygienic than wood and therefore ideal for food transport. Moreover, the uniform size and dimensions of plastic pallets, along with their durability, make them a good fit for modern automated equipment. Some even come with RFID tags embedded to ensure easy tracking through the supply chain.
Because of the benefits discussed above, many grocery chains are beginning to phase out wood pallets entirely in favor of plastic. Costco is one example. This chain recently established a two-year plan to accept only plastic pallets from vendors. Reasons for the switch include the sustainability, low weight, improved hygiene, and durability of these platforms. Vendors who adopt the use of plastic pallets now will find themselves aligned with more and more grocery chain pallet requirements requesting plastic shipping platforms.