Plastic Pallet Pooling Benefits for
Meat & Protein
The protein and meat industry is fraught with risks and challenges. To cultivate a loyal customer base, manufacturers and retailers alike must deliver products guaranteed to be free of contamination using sustainable, cost-effective logistics solutions. Manufacturers of fresh, frozen, and canned meats, as well as the retailers who sell them to consumers, have the heavy responsibility of delivering meat items that not only comply with the standards of the FDA’s Food Safety Modernization Act (FSMA) but also meet consumers’ low-price, high-quality expectations.
The challenge for manufacturers in the protein industry then becomes how to deliver meat product shipments to the retailer free of spoilage and contaminants, especially as supply chains become longer. As the starting point in the supply chain, the responsibility of food safety often falls more substantially on the manufacturer.
Retailers, on the other hand, can often feel as though they have little control over the supply chain before a product reaches their shelves. How can grocery retail stores feel confident that the meat shipments they accept have not been contaminated anywhere in the chain while being transported, from being loaded onto a pallet at the manufacturer’s warehouse facility to the moment fresh or frozen meat is put on display in a cold case?
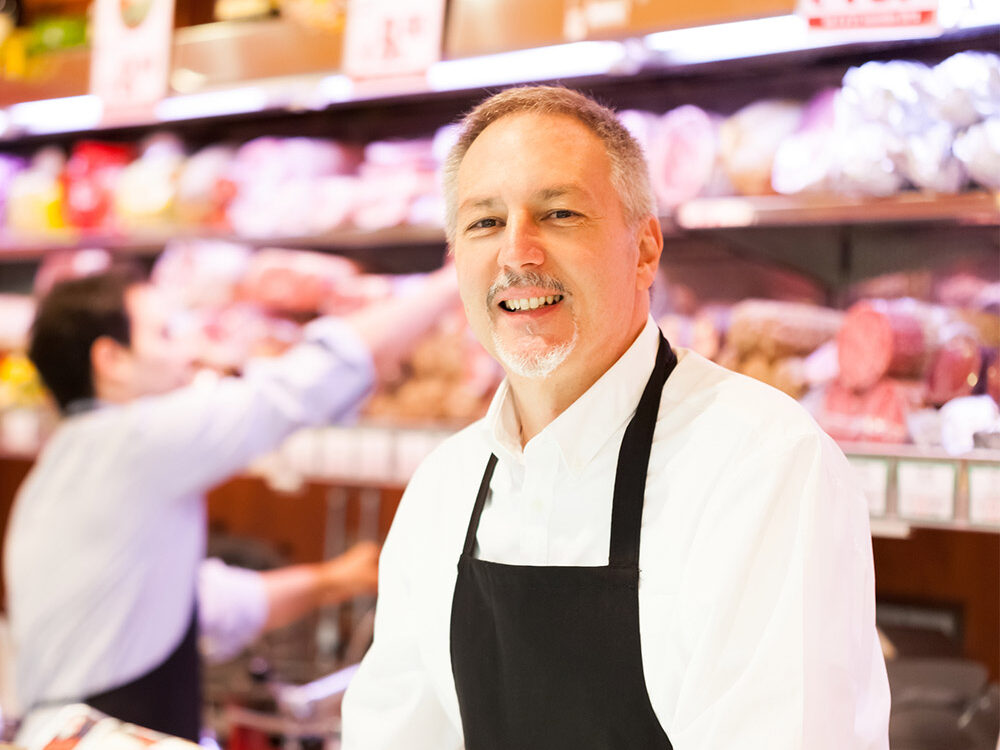
Why iGPS: The Best CBA Compliant Plastic Pallets for the Meat Industry
When you ship your meat products using CBA-compliant iGPS plastic pallets, you give your business, your retail partners, and your loyal consumers an added layer of protection. Hygiene, worker safety, and sustainability increase exponentially; simultaneously, product damage and transport costs are slashed. These benefits allow all manufacturing, warehousing, and handling systems to most effectively optimize automation throughout the entire supply chain.
Shipping pallets used within the meat industry must offer a crucial level of reliability and consistency. Irregular or broken wood pallets may damage packaging, enabling cross-contamination or exposure to unhygienic environments. Wood pallets are also porous, absorbing contaminants that cannot be removed. They can swiftly become a breeding ground for the bacteria always ready to hitch a ride in your shipments, such as Listeria and salmonella, not to mention parasites. The age of the wooden pallet is over.
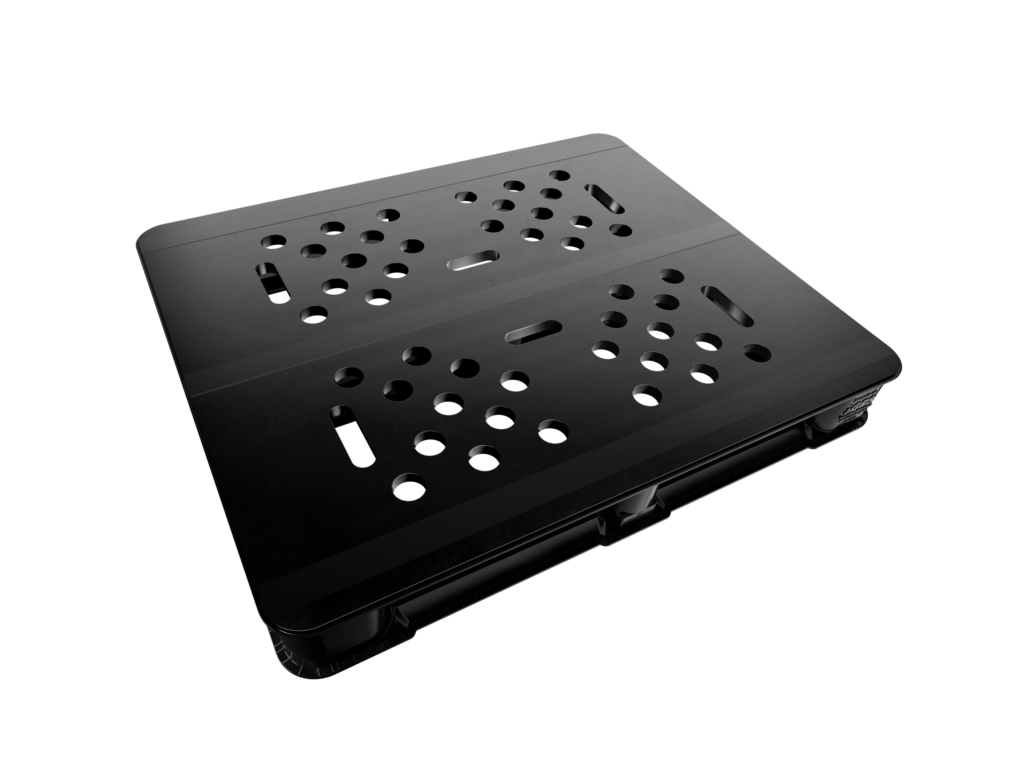
Only the iGPS plastic pallet pooling system offers the advanced shipping technology and logistics experience needed to give the meat manufacturer greater control over and confidence in their packaged meat shipments.
To get started with iGPS, reach out to our logistics experts today at 1-800-884-0225 or email us at info@igps.net. Our team will walk you through how our innovative shipping options can drastically lower your total cost of business.
The Seven Competitive Advantages and Benefits of the iGPS Plastic Pallet
- Food Safety and Hygiene: The pallet that packaged meat products are shipped on affects both hygiene and freshness. Only the iGPS plastic pallet is impervious to insects and rodents, does not rot or absorb moisture, and is highly resistant to bacteria. Aside from meeting the FDA’s FSMA standards, this also means that you will never need to expose an iGPS pallet, and therefore your products, to fumigation or pesticides.
- Reduced Transportation Costs: The plastic iGPS plastic pallets reduce your shipments’ weights. Weighing around 50 pounds, iGPS plastic pallets are up to 35% lighter than standard wood pallets. The result is lower fuel costs to transport your products from the warehouse to the retailer. Lighter loads also mean faster delivery—and meat shipments must arrive at their destination as quickly as possible.
- Reduced Product Damage: The iGPS plastic pallet is sturdy, uniform, and has no protruding edges or parts. This reduces the chance that your packaged products will be damaged during transport. iGPS pallets can stand up to cold packs or dry ice, i.e. -109.3 degrees Fahrenheit, without cracking or breaking. That’s a big advantage in the meat industry as it helps protect whole product shipments from being rejected or destroyed.
- Increased Automation: As manufacturing, warehousing, and handling systems continue to become increasingly automated, all pallets must adhere to consistent physical parameters. The iGPS plastic pallet is ideal for automated systems as each one is a uniform 48 x 40 inches in dimension. Its uniform design will not cause errors in automated systems and eliminates unwanted product overhang. Shrinkage and warping are also not a concern with iGPS platforms, ensuring compatibility with automated guided vehicle (AGV) technology.
- Sustainability: iGPS plastic pallets eliminate the need for wood platforms, which reduces the consumption of trees. Our pallets are reusable, long-lasting, and require less fuel to transport, which reduces carbon emissions during transit. To estimate the amount of carbon emissions the iGPS pallet can reduce for each of your shipments, try using our greenhouse gas calculator.
- Increased Worker Safety: The iGPS plastic pallet is not only safer for employees to work with than wood pallets but also makes handling pallets easier. Durable plastic eliminates gaps, broken boards, protruding nails, and splinters that can injure meat industry warehouse workers.
- An Efficient Pooling System: Pallet pooling allows the meat industry to deliver the freshest products possible, as pooling enables a focus on capital expenditures and day-to-day supply chain operations. By renting pallets rather than buying them, you get the exact number of pallets you need, when you need them, which eliminates the expense of purchasing, maintaining, and warehousing a pallet inventory. Pooling means pallets are efficiently allocated and routed to maximize both usage and transportation resources.
iGPS delivers quality pallets, on time, as required by the manufacturer. The manufacturer then ships their products on pallets to their distributors, who may store the products in warehouses or immediately ship them out to grocery retailers throughout North America. Once the pallets have been unloaded at a retail outlet, iGPS arranges for the return of the empty pallets back to one of their many depots throughout North America for inspection, cleaning, and, if required, repair. They are then reissued to another manufacturing customer. The iGPS pallet pooling system is seamless, cost-effective, and ensures that operations run more smoothly for everyone who handles meat products and helps bring them to the consumer.
iGPS aligns retailers and manufacturers by helping them achieve their shared goal of meeting consumer demand for excellent quality meat products at affordable prices. Our seven key competitive advantages help lower the total cost of business—for retailers and manufacturers alike.
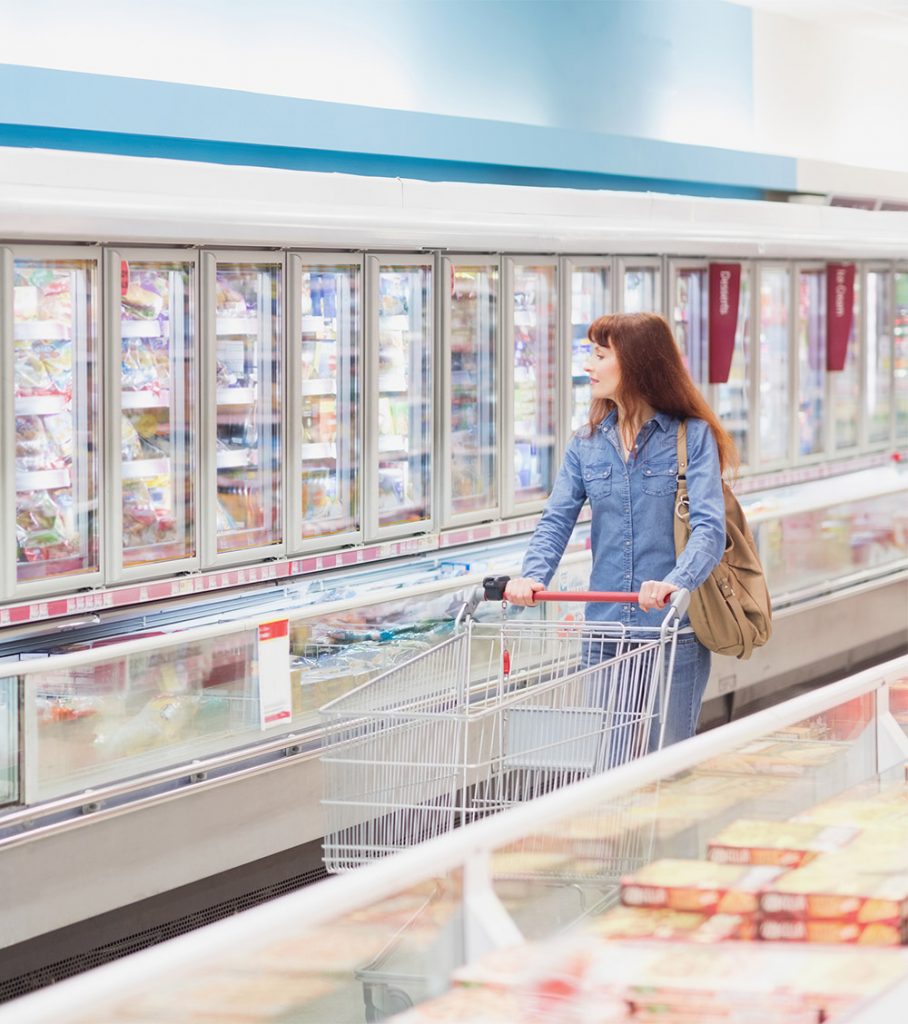
Sustainable and Cost-Effective: Choose iGPS to Lower Your Total Cost of Business
Protein and meat retailers and manufacturers both share in the challenge of bringing a highly perishable food product safely to market. Each stakeholder in the supply chain must meet a seemingly impossible mandate: Increase safety and convenience while lowering costs along the supply chain to pass those savings on to consumers.
Why waste money on an inferior, wooden pallet with inherent problems? Invest in the iGPS plastic pallet pooling solution that lowers your total cost of business by making your supply chain run more efficiently. When you lower costs, increase sanitation, and support automated warehouse activities, all supply chain stakeholders win. Deliver shipments with pride by investing in CBA-compliant iGPS pallets. Good for business; good for the planet.
iGPS Plastic Pallets
Are sanitary enough for bagged lettuce but strong enough for bagged concrete.
Allow you to easily track shipments through RFID technology.
Meet the highest standards of platform hygiene, according to the FDA’s Food Safety Modernization Act.
Are compliant with Consumer Brand Association (CBA) specs.