If your facility invested in an automatic pallet wrapper, then you’re likely already experiencing total cost of business (TCOB) reductions. Consider the efficiency gains in sheer productivity. Remember when one warehouse worker would wrap maybe thirty pallets over the course of an entire workday? Entry model turntable wrappers can wrap as many in one hour, and more advanced double rotary arm wrappers can accomplish 130 pallet wraps per hour. Moreover, these automated improvements can be accomplished while saving warehouse workers from repetitively contorting their bodies into awkward wrapping positions that often result in strained necks and backs—and sometimes workers’ compensation claims.
While automation-generated savings can substantially lower TCOB and promote workforce well-being, managers can optimize these savings by following the most effective automatic pallet wrapper safety practices for warehouses. Let’s take a closer look at some of the best practices for operating an automated stretch wrap machine and then examine how plastic pallets fit into the overall safety equation.
Automatic Pallet Wrapper Safety Protocols
As warehouses transition from wrapping pallets manually to utilizing advanced machinery to accomplish the job, managers should ensure that they are implementing the appropriate safety practices to accompany their productivity upgrade. Here are a few best practices that will strengthen warehouse automatic pallet wrapper safety.
Best Practices for Automated Pallet Wrapper Safety
- Implement machine guarding standards for automated workspaces to protect warehouse workers and visitors.
- Erect barriers around pallet wrapping area.
- Install presence detection systems that can interface with automated wrapper controls and shut down the automated wrapper if a sensor is triggered.
- Upgrade machinery safety features.
- Review machinery features to confirm that a safety stop is present on the wrapper. Safety stops reduce scenarios where workers could suffer a crushed hand or foot.
- Update the automated wrapper’s control panel to feature a large, visible emergency shut off button.
- Optimize the automated wrapper workspace.
- Remove any cords, cables, or wires present in the workspace as they create tripping hazards.
- Follow a daily cleaning schedule to clear the workspace of dirt and debris that could endanger both workers and machinery.
In addition to the above best practices for automated pallet wrapper safety, forward-thinking warehouse operators are increasingly turning to durable plastic pallets with a uniform weight and size to gain efficiency benefits in the automated warehouse.
Why Plastic Pallets Increase Safety in the Automated Warehouse
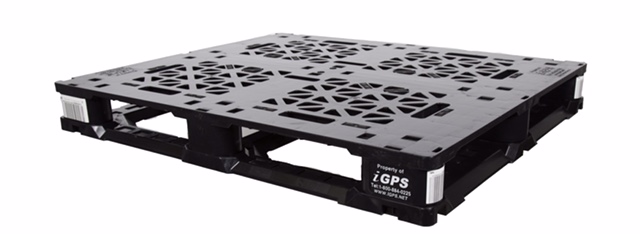
Warehouse managers have found that plastic pallets are uniquely well-suited to the rigors of the automated warehouse. Listed below are a few of the ways that plastic pallets stand out as the perfect choice for the automated warehouse.
Safer for Workers
Industry-leading plastic pallets meet the National Institute for Occupational Safety and Health weight standard for single worker lifting. Weighing around 50 pounds per pallet (up to 35 percent lighter than wood pallets), with thoughtfully designed features like ergonomic handles, plastic pallets are safer and easier to lift than wood pallets. Lightweight and easy to handle pallets help to decrease warehouse accidents and injuries.
Safer for Products
Plastic pallets that provide solid top deck coverage reduce product damage that can occur during transportation. Additionally, plastic pallets eliminate splinters and protruding nails that can damage products. And unlike wood pallets, plastic pallets will not absorb liquids that lead to product contamination and pallet decay.
Safer for Equipment
Consistency is key in the automated warehouse setting. Unlike wood pallets that degrade rapidly over a short lifespan, plastic pallets maintain a uniform weight and size over about 100 trips through the supply chain.
Plastic Pallets: The Perfect Fit for Automated Warehouses
Automated pallet wrappers present warehouse managers with an opportunity to increase warehouse efficiency and safety while reducing their total cost of business. By switching from wood pallets to plastic pallets, warehouse managers can ensure that these improvements achieve the greatest possible time and cost savings.
iGPS’ 100% recyclable plastic pallets are designed for the rigors and the requirements of the automated warehouse. To learn more about how iGPS pallets can enhance your automated pallet wrapper’s safety and efficiency, give our team a call at 1-800-884-0225, email a specialist at switch@igps.net, or visit our contact page.