Key Takeaways:
- Strong Carrier Management is Essential: Effective carrier selection, fostering positive relationships, and leveraging technology are crucial for a healthy supply chain.
- Become a Shipper of Choice: Prioritize on-time deliveries, efficient loading/unloading, and clear communication to earn better rates and reliable service from carriers.
- Embrace Technology and Data: Implement Transportation Management Systems (TMS) to track KPIs, analyze data, and make informed decisions for optimizing carrier selection and performance.
Best Practices for Effective Carrier Management
The past few years have been a whirlwind for the supply chain industry, exposing vulnerabilities while offering valuable lessons in building resilience and optimizing operations. For many businesses, the real burden lies not in managing inventory or addressing customer needs, but in overseeing the carriers that keep their products moving — it’s here that the gears can quickly grind to a halt. Companies can position themselves as shippers of choice and unlock significant benefits by implementing best practices in carrier management. These best practices include strategic carrier selection, fostering robust relationships with chosen partners, and leveraging technology solutions to streamline processes, maximize efficiency, and reduce stress. There’s a clear reason why top industry performers have such impressive track records — their hard-won expertise has been battle-tested and proven to drive real results. It’s a simple yet powerful truth: effective carrier management is the foundation of a solid supply chain. Here is a list of best practices to consider:
Boost Efficiency: Become a Shipper of Choice
The foundation of effective carrier management lies in building durable relationships with reliable partners. It is crucial to select carriers who align with your business objectives. Consider on-time delivery rates, cargo handling capabilities, and technology integration.
Remember, the pool of top-performing carriers is finite, especially with a projected driver shortage of 160,000 by 2030, according to the American Trucking Associations. Partnering with the best not only reduces costs but also improves overall operations. Carriers frequently give the best deals to shippers they can count on, especially when demand is sky-high. Building trust with carriers involves understanding their frustrations and adjusting to develop mutually beneficial relationships.
Identify and Maintain Key Performance Indicators (KPIs)
KPIs are the metrics that measure success in carrier management. These include on-time delivery, tender acceptance/rejection rates, invoice accuracy, and upfront pricing precision.
However, it’s important not to overlook intangible factors like communication quality and responsiveness to issues. Integrating these metrics with technology allows for real-time data analysis, enabling informed decision-making. For instance, Transportation Management Systems (TMS) can improve transportation performance and are a less risky choice, as Sam Kheir, iGPS’s Carrier Procurement Manager, notes in a recent column for Supply & Demand Chain Executive.
A successful TMS implementation hinges on features that address critical areas like planning, execution, fleet management, and robust carrier integration. This holistic approach minimizes roadblocks and ensures a smooth overall operation.
Managing Risks Proactively
Unforeseen events can disrupt even the best-laid plans. Think of a TMS as a security blanket; it is a shield from unwanted surprises because it enables scenario planning, real-time data analysis, and contingency plan creation. The system can empower a business to compare potential disruptions and choose the best course of action. This focus on real-time insights is complemented by investment in business continuity planning, ensuring a robust response system for unforeseen disruptions. A study by Marsh McLennan, a leading professional services firm, revealed a gap between risk awareness and preparedness. While six key emerging risk areas (climate change, cyber threats, technological advancements, geopolitical instability, post-pandemic challenges, and evolving regulations) are widely recognized as significant threats, only 25 percent of companies are actively evaluating or modeling the potential impact on their business. By proactively managing risk with a TMS and robust business continuity planning, companies can transform uncertainty into an opportunity to come out stronger.
Open Communication and Constructive Feedback
Open and honest communication is the only way to foster solid bonds with carriers; it’s the foundation for all successful partnerships.
Carriers that want to hit their targets need to pinpoint their strengths and weaknesses, then work on closing the gaps. Building an open-book environment where concerns are discussed without hesitation helps both parties stay on the same page. Fewer, more reliable partners can mean deeper relationships and a more efficient way of doing business; a win-win for companies and carriers.
However, it is also essential to select carriers with the capacity to meet a business’s specific needs. For example, finding carriers for standard shipments is easier than finding carriers for temperature-controlled or less-than-truckload (LTL) shipments. Diversifying the carrier pool or partnering with larger LTL providers may be necessary for greater flexibility.
Building a Mutually Beneficial Partnership
Becoming a shipper of choice requires businesses to demonstrate their value to carriers and reward carriers that consistently meet or exceed KPIs by offering increased business opportunities. Consistent, on-time shipments, efficient loading and unloading practices that minimize downtime, and clear communication regarding volume expectations and special requirements all contribute to this. This benefits shippers by securing reliable capacity at competitive rates and allows carriers to optimize their operations and maximize profitability.
Optimizing Efficiency with Plastic Pallet Pooling Services
Effective carrier management goes beyond simply selecting reliable partners and fostering long-term relationships. It’s about streamlining processes and maximizing efficiency throughout your entire supply chain. This is where plastic pallet pooling services come into play.
Traditional wooden pallets can be a hidden bottleneck in carrier management. Due to inconsistent sizes, they can be damaged, require frequent repairs or replacements, and contribute to wasted space on trailers. These inefficiencies can lead to delays, increased transportation costs, and frustration for shippers and carriers.
Plastic pallet pooling services offer a compelling alternative. These services provide businesses with a network of high-quality, reusable plastic pallets that can be used throughout their supply chain.
The benefits of plastic pallet pooling services for carrier management are numerous, including reduced transportation costs, improved on-time delivery, enhanced damage protection, and minimized downtime. Businesses can significantly enhance their carrier management strategies by implementing plastic pallet pooling services.
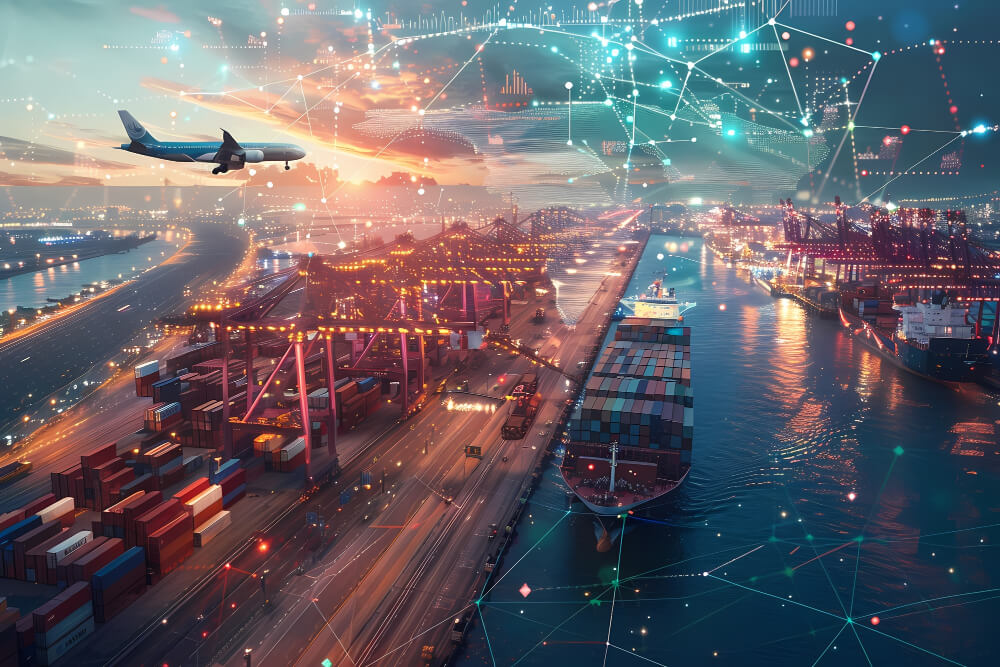
FAQ
Why is strong carrier management essential for a robust supply chain?
Effective carrier management ensures the smooth movement of products through the supply chain. This involves strategic carrier selection, fostering positive relationships, and leveraging technology to optimize processes, improve efficiency, and ensure peace of mind.
How can an organization position itself to become a shipper of choice for carriers?
Companies can become shippers of choice by prioritizing on-time deliveries, ensuring efficient loading and unloading practices and other procedures, and maintaining clear, proactive communication with carriers. Building trust and understanding (and fixing) situations that lead to headaches can also lead to better rates and more reliable service.
What role does technology play in optimizing carrier management?
The latest cutting-edge technology, especially Transportation Management Systems (TMS), plays a critical role in tracking key performance indicators (KPIs), analyzing data, and making informed decisions during every phase of the transportation process. Such tools improve transportation performance, enable real-time data analysis, and guide organizations in proactive risk management.
What are the benefits of using plastic pallet pooling services in carrier management?
Plastic pallet pooling solutions reduce transportation costs, improve environmental sustainability, and enhance product and worker safety.
As we navigate the continually evolving supply chain landscape, effective carrier management is the cement that holds everything together. By positioning themselves as a shipper of choice, embracing new technology innovations, and adopting sustainable alternatives like plastic pallet pooling services, organizations can build resilient partnerships and set themselves up for business success.
Manufacturers looking to streamline their carrier services can enhance their logistics operations by opting for iGPS plastic pallets. These pallets are engineered to seamlessly integrate with automated systems, ensuring a smooth flow in an increasingly automated supply chain. For more information, contact us at 800-884-0225, email a specialist at switch@igps.net, or visit our contact page.