ARTICLE UPDATED ON SEPTEMBER 19TH, 2022
During a product’s journey from the manufacturer to the retailer, it is not uncommon for damage to occur. As incoming shipments arrive, retail managers routinely check for damaged products and intercept damaged goods before they can enter inventory. Product damage during transportation is so frequent that it is common for store managers to order extra product just to ensure that they have enough sellable inventory on hand to meet their customer’s demands. Many businesses accept product damage during transportation as a normal part of their operations and pre-calculate it as part of their Total Cost of Business (TCOB). However, supply chain technology is constantly evolving, and transportation managers and logistics coordinators will find that if they put the effort into building a resilient supply chain and reducing product damage they can boost efficiency, reduce costs, and optimize their supply chains.
Top Causes of Product Damage

One of the top reasons of damage during transportation is load shifting. This may occur when products are not stacked correctly. If one package moves, other packages on the pallet can be shifted out of place and the load becomes unstable. Once out of place, if there is a sudden stop or shift in speed, the products are no longer safe against damage. If the weight is transferred to points in the load that are not able to take the strain, it may result in crushed packages, squished produce, or broken beverage containers.
Most manufacturers and distributors take measures to prevent this sort of shifting. They carefully pack the loads in the recommended way, then wrap the pallet load with shrink wrap to hold everything in place. Unfortunately, these measures are not 100 percent effective. Product damage can still occur due to:
- Improper Packing: Packing products is not an exact science, especially at distribution centers where loads coming from manufacturers are broken apart to make mixed product loads that will be shipped to retail stores. Canned food, beverages in boxes, and paper goods can all end up on the same pallet, and there may not be a foolproof way to pack these all together and ensure they do not shift. Wrapping a load too tightly may crush products and not wrapping it tightly enough can allow the load to shift; either issue can cause product damage during transportation.
- Forklift Damage: Forklifts can damage a pallet, which is a persistent problem in supply chain logistics. Products can be damaged by the forklift as it transports them throughout a facility, or a forklift may damage the pallets the products are carried on, heightening the chances of damage throughout the transportation process.
- Pallet Damage: When looking to reduce product damage throughout the supply chain, it is important that a manufacturer chooses the right pallet for their needs. Wood pallets in particular can become damaged during their operational life, and while warehouse workers make the effort to sort out pallets that are too damaged to be used, inevitably some will slip through. A board that breaks or comes loose when the pallet is packed or moved might not be noticed. Later, the damaged surface can move during transport, causing the load to shift and ultimately leading to product damage.
Products may also become damaged during storms and other severe weather events — which are becoming more and more prominent. A severe rainstorm may flood a fulfillment center, causing water damage, and extreme temperature and humidity changes can greatly impact perishable items and significantly decrease their shelf life. Products transported by ship may also be impacted by stormy waters. Items stored in glass or breakable bottles can move and fall, causing a loss of products due to damage. It is imperative that manufacturers and retailers find ways to build their supply chain resiliency to protect against product damage in severe weather events.
How to Reduce Product Damage with Better Equipment
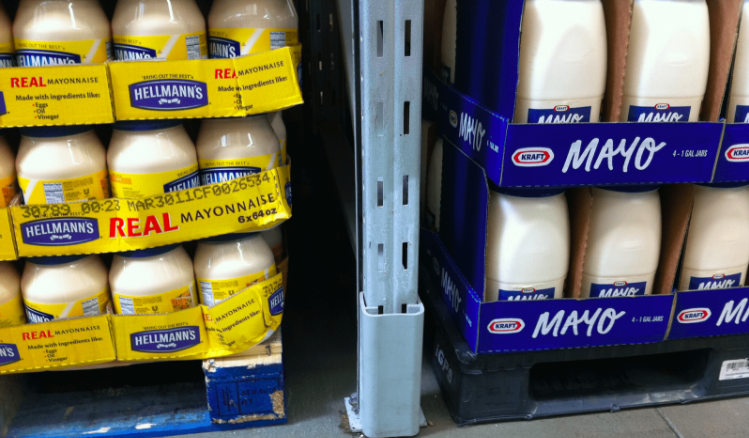
To prevent product shifting, almost all pallet loads are wrapped in clear plastic stretch wrap. The quality and amount of this wrap can make a big difference in its effectiveness, as can its compatibility with the method used to wrap loads. Many fulfillment centers employ automatic pallet wrappers to reduce the risk of error, optimize the process, and build resiliency. One warehouse worker can wrap about thirty pallets over the course of their workday, while most automatic pallet wrappers can wrap as many in an hour.
Another equipment upgrade that can reduce damage is an improved shipping platform. Wood pallets are prone to damage, such as protruding nails and splinters, which in turn can lead to product damage during transportation. Using a more durable pallet that can better stand up to rough handling can reduce the amount of product damage and can save companies money.
Using a more durable pallet…can save companies anywhere from $0.15 to $0.70 cents per pallet.
Plastic pallets reduce product damage in other ways, too. Manufacturers looking to reduce product damage in their supply chains may benefit from using recyclable, lightweight iGPS plastic pallets. Their durability helps reduce debris and other waste in transportation and warehouse spaces that can damage loading equipment. Plastic is also impermeable to fluids, which limits the spread of product and chemical spills and improves hygiene while preventing chemical contamination.
As products are transported throughout the supply chain, damage is inevitable. Both logistics operations and outside factors such as weather play a role. But by enhancing processes and working toward a more resilient supply chain, companies can decrease the amount of product damage that occurs and improve their bottom-line benefits.
Companies committed to reducing product damage in their supply chain use iGPS plastic pallets for all their shipping needs. Our lightweight, recyclable plastic pallets can help reduce harmful emissions and your Total Cost of Business. For more information, contact us at 1–800-884-0225, email a specialist at switch@igps.net, or visit our contact page.