Key Takeaways:
- Warehouse automation is experiencing a revolution, as sophisticated AI and robotics systems tackle tasks that were once deemed non-automatable.
- Industry leaders are embracing automation at an accelerated pace, driven by labor shortages and the booming online grocery market.
- Types of automated systems include pallet shuttles, autonomous guided vehicles, and palletizers.
- Although automation may result in workforce reduction, it also demands skilled personnel for maintenance.
- Plastic pallets can improve automation equipment performance and return on investment.
AI and Robotics Powering the Future of Grocery Warehouse Automation
Gone are the days of clunky, unreliable robots relegated to the warehouse periphery. Today’s warehouse automation is experiencing a revolution spearheaded by sophisticated AI and robotics tackling tasks once deemed non-automatable. This wave of innovation is rippling outwards, transforming industries like the grocery supply chain, where automation is streamlining tasks and elevating efficiency levels beyond what was once deemed possible.
Grocery warehouses are gearing up for a robot-powered future. Industry leaders are embracing automation at an accelerating pace, driven by factors like persistent labor shortages and the booming online grocery market. A 2023 report by Mordor Intelligence predicts the retail automation market, including e-grocery automation, will balloon to $37.38 billion by 2029, with a Compound Annual Growth Rate (CAGR) of 14.66 percent. This surge reflects the industry’s need for increased efficiency and cost reduction. However, with notoriously thin profit margins in groceries, careful planning and a thorough understanding of automation’s potential are vital to maximizing its benefits in future years.
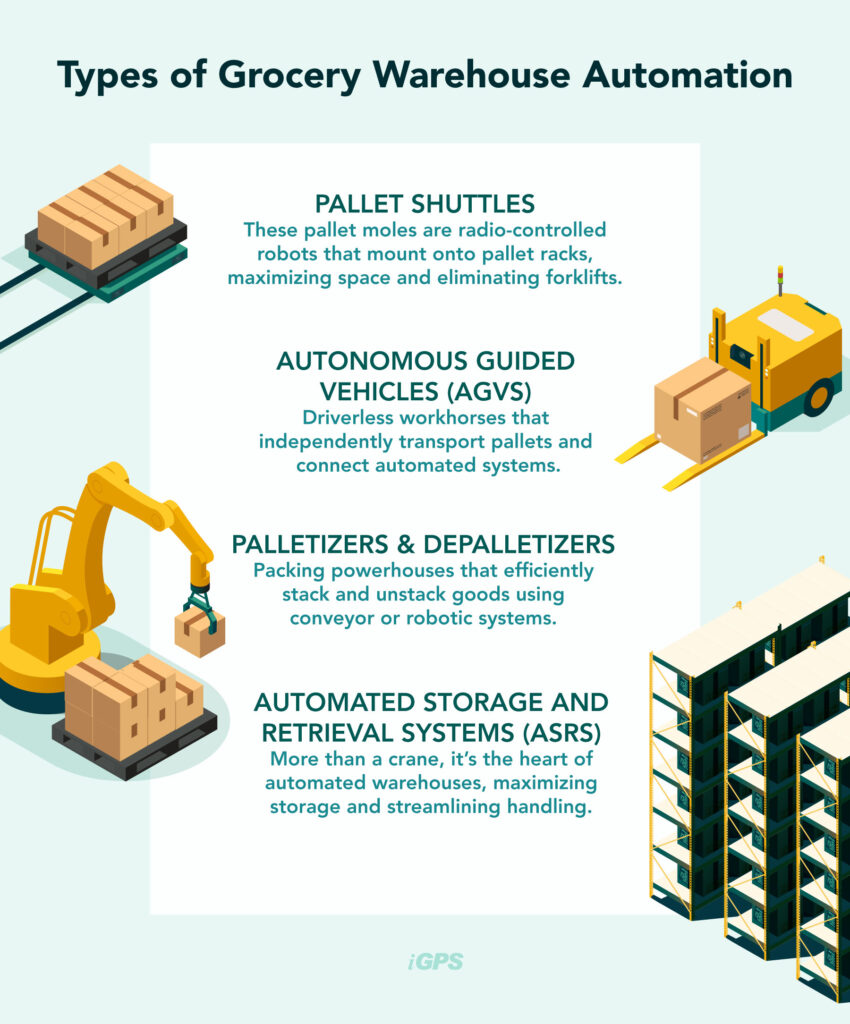
Types of Grocery Warehouse Automation
Forget a “one-size-fits-all” approach. Today’s grocery warehouses leverage a customized mix of automation based on their inventory. This shift reflects the diverse needs of their inventory. Delicate produce like lettuce demands specialized handling, while retailers manage a wider range of goods. A 2023 Grand View Research report predicts a booming market reaching $63 billion by 2030. Produce companies might use temperature-controlled storage and gentle robotic pickers, while retailers managing a wider variety of goods might benefit from palletization systems alongside automated storage and retrieval systems. The key takeaway? Modern grocery warehouse automation thrives on customization, considering factors like temperature sensitivity and product fragility. Grocery warehouse automation usually falls into one of the following broad categories:
- Pallet Shuttles, The Warehouse Space Maximizers: Pallet shuttles, nicknamed “pallet moles,” are radio-controlled robots that transform warehouse storage. These high-tech sleds mount directly onto existing pallet racking. When a pallet needs storing or retrieving, the shuttle glides beneath it, lifts it, and transports it within the rack structure. This eliminates the need for forklifts to constantly maneuver through aisles, freeing up valuable floor space. Pallet shuttles allow warehouses to create high-density, deep-lane storage, maximizing their storage capacity without expanding their footprint.
- Autonomous Guided Vehicles (AGVs), Driverless Workhorses: AGVs are robotic vehicles that navigate warehouses, carrying pallets and racks. They come in various forms, from forklifts to shuttles, and can operate independently or bring different automated systems together.
- Palletizers and Depalletizers, the Packing Powerhouses: Palletizers and depalletizers handle the important tasks of stacking and unstacking goods onto pallets. These systems come in two main types: conveyor-based and robotic. Conveyor systems, equipped with bumpers and hydraulic clamps, excel at efficiently handling standardized items. Robotic arm palletizers are game changers, handling a broad array of packages with their knack for grabbing and placing boxes with precision.
- Automated Storage and Retrieval Systems (ASRS), More Than Meets the Crane: ASRS is more than just a fancy crane. It’s the core component of an automated warehouse. This system combines different technologies like pallet shuttles for maximizing storage space, autonomous guided vehicles (AGVs) for transporting goods, and palletizers/depalletizers for streamlined handling.
The story differs for perishable fresh produce, meats, and unpackaged foods, though. These products rely heavily on human labor for tasks like sorting, inspecting, and handling conveyor belts. The delicate nature of these items and the need for human expertise in assessing quality present a challenge for current automation technologies. In grocery warehouses, juggling efficiency with care requires sharp thinking. While automation excels in handling standardized goods, a successful strategy likely involves a well-balanced combination of human oversight and automation for tasks requiring agility and adaptability.
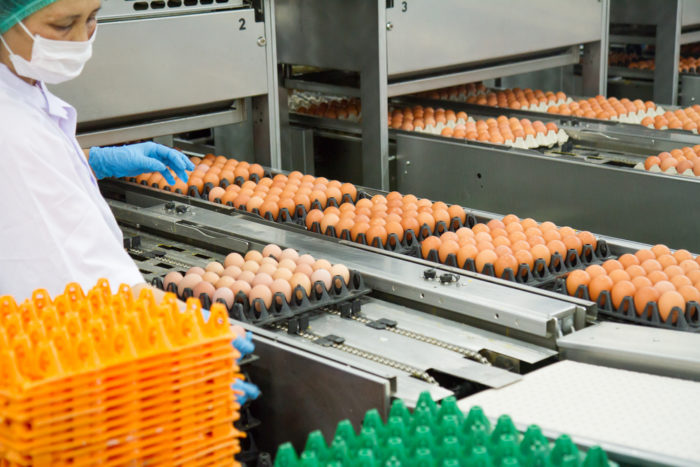
The Role of Warehouse Automation in the Grocery Industry
Labor cost reduction is a frequent argument in the automation debate. On one hand, there’s excitement over making processes more efficient. On the other hand, there’s anxiety about job displacement. The reality is more nuanced. While automation may see workforce reductions, it also demands skilled personnel for maintenance. A McKinsey Global Institute study predicts AI could create a wave of new jobs — between 20 and 50 million globally by 2030 in various sectors.
The rise of articulated robotic arms is also making grocery automation more accessible. Take robotic palletizers — a cost-effective alternative to manual labor, they excel at mixed-caseloads.
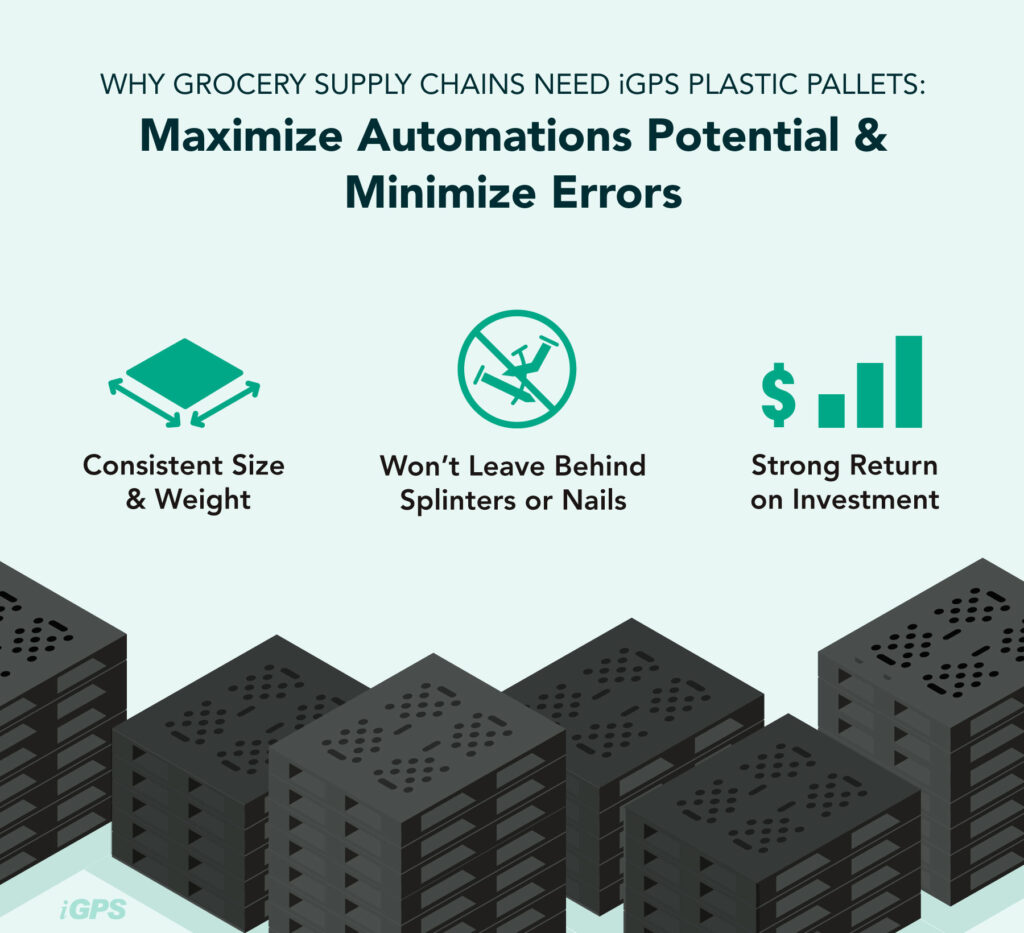
These robots and some AGVs are ideal for smaller warehouses due to their scalability and affordability. A 2023 report by Markets and Markets forecasts that by 2029, the robotic palletizer market is estimated to reach a staggering $1.9 billion, up from $1.4 billion in 2024. This targeted automation allows smaller grocery warehouses handling pre-packaged goods to compete and optimize efficiency in the evolving supply chain.
Automation excels with consistent packaging. Pre-packaged cartons of standard size and weight are perfect for robotic palletizers, boosting efficiency. This holds across warehouses: consistency is king for automation.
This applies not only to packaging, but also to shipping platforms. To maximize the benefits of consistent packaging and minimize errors even further, food and beverage manufacturers are increasingly turning to durable, automation-friendly iGPS plastic pallets to maximize automation’s potential. Wood pallets can absorb moisture, which not only increases their weight but also causes them to swell and warp, which can create problems for palletizers and other automated equipment. Plastic pallets, on the other hand, do not absorb moisture and maintain a consistent size and weight at all times. Plastic pallets also do not shed nails and splinters, which can further jam automated equipment while creating additional cleanup and maintenance headaches, and their embedded RFID technology enables iGPS pallets to communicate with Autonomous Guided Vehicles and other robotic equipment to ensure appropriate placement within automated storage and retrieval systems.
One thing is for certain — the grocery industry isn’t going backward. Food and beverage manufacturers and grocery retailers will continue to embrace the latest innovations while enabling products to be made more quickly, more cost-effectively, and in greater volumes. Exciting times are ahead.
Key Questions and Answers
What are the benefits of automation in a warehouse?
Automation improves efficiency and reduces manual labor, minimizes errors, and results in long-term cost savings.
What is the objective of warehouse automation?
The objective of warehouse automation is to optimize operations by streamlining processes, improving accuracy, and reducing costs.
How does automation benefit workers?
Workers in automated environments benefit from increased productivity, improved safety, and enhanced job satisfaction because they can work on more complex tasks.
Manufacturers navigating grocery warehouse automation due to the rise of artificial intelligence (AI) can enhance their logistics operations by opting for iGPS plastic pallets. These pallets are engineered to seamlessly integrate with automated systems, ensuring a smooth flow in increasingly growing AI-focused warehouses and facilities. For more information, contact us at 1-800-884-0225, email a specialist at switch@igps.net, or visit our contact page.
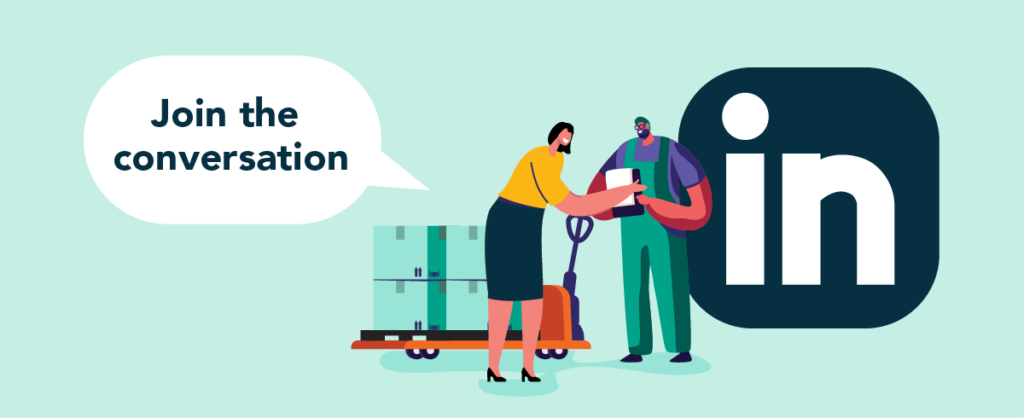