Key Takeaways:
- Nearshoring, which involves relocating production closer to home, is gaining traction as companies seek greater supply chain resilience and efficiency.
- U.S. imports from Mexico have surged 32 percent since pre-pandemic levels, highlighting the shift from traditional offshore manufacturing to nearshoring.
- Nearshoring offers a range of benefits, including reduced lead times, improved supply chain resilience, and protection against geopolitical and natural disruptions. These advantages make nearshoring an attractive option for many companies, despite the challenges it presents such as initial setup costs and regulatory hurdles.
How Nearshoring is Revolutionizing Supply Chains
The global supply chain has seen significant changes in recent years. The “just-in-time” model, known for its razor-thin inventory levels and lightning-fast deliveries, was once hailed as the pinnacle of efficiency has been disrupted by unforeseen events like the COVID-19 pandemic and geopolitical tensions. As companies rethink their approach to sourcing, a clear shift is underway – nearshoring is fast becoming a compelling alternative.
What is Nearshoring?
Nearshoring involves strategically shifting production or sourcing activities from distant overseas locations to geographically closer countries. It typically means relocating operations to neighboring countries or those within the same region. For example, a US-based company might relocate its manufacturing from China to Mexico or another Central American nation.
Momentum for this trend is building, increased by the desire for greater supply chain resilience and efficiency. According to a report by Kearney, a global management consulting firm, U.S. manufacturing is making a comeback, fueled by nearshoring.
The data reveals a dramatic decline in U.S. imports from low-cost Asian countries, with a $143 billion drop in 2023 compared to the previous year. China, a major source of imports, saw a particularly sharp decrease of 20 percent. Meanwhile, Mexico, a preferred nearshoring destination, has experienced a boom. U.S. imports from Mexico have surged by 32 percent since pre-pandemic levels, surpassing China as the top exporter to the U.S. for the first time since 2013. These statistics paint a clear picture: As the pandemic spread, companies began to reverse the outsourcing trend, rebuilding production capacity closer to home.
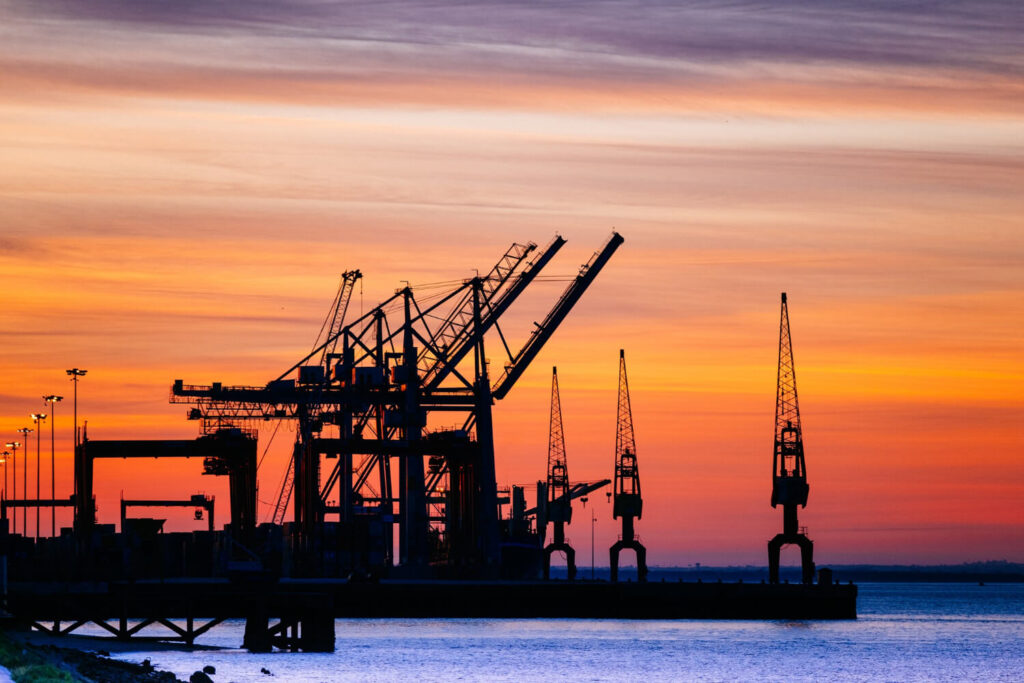
Examples of Nearshoring in Action
Several U.S.-based companies are beginning to put nearshoring strategies into action.
Mexico’s close location to the U.S. has made it a potential magnet for carmakers like Ford and GM, thanks to its geographic proximity and lower production costs. This shift towards nearshoring can pave the way for these and other companies to streamline their operations, possibly slash costs for car parts, and ultimately put more affordable vehicles on American driveways.
Apple has also moved some of its iPhone 14 production to India from China in a notable instance of a trend called “friendshoring,” which refers to companies shifting their manufacturing bases to allied nations. Both these trends involve companies strategically shifting production or sourcing locations, though friendshoring prioritizes trusted partners over pure geographical closeness.
By September 2023, a whopping 42 companies set up shop in Mexico specifically due to nearshoring trends; of those, eight were from the United States, according to market analysis from ProMexico Industry, a website designed to attract foreign companies to invest in manufacturing facilities in Mexico.
Benefits of Nearshoring
By relocating production closer to home, to countries like Mexico, companies could allow for quicker responses to market demands and reduce the risk of stockouts (that’s when a manufacturer runs out of a product, which could lead to customer dissatisfaction). One of the most significant benefits of nearshoring, for example, appears to be reduced lead times.
But beyond the geographical benefits, nearshoring also enhances supply chain resilience in several key ways. The first way is by fostering diversification. Nearshoring opens the door to a broader pool of potential partners and simultaneously reduces reliance on a single source half a world away. It also spreads the risk. For instance, a possible disruption at one supplier won’t halt the entire production line.
Secondly, nearshoring helps companies sidestep potential geopolitical flare-ups. By working with local suppliers, businesses reduce the risk of being exposed to possible international conflicts and other trade disruptions.
Finally, nearshoring can present a shield against the unpredictable forces of nature. Floods, earthquakes, and other natural disasters can throw wrenches into supply chains. Nearshoring can help businesses weather these storms.
Challenges of Nearshoring
While it’s clear there are many benefits, nearshoring also comes with challenges that companies must navigate to ensure a successful transition. One of the primary issues is the initial setup costs. Transitioning to nearshoring can involve significant up-front infrastructure, technology, and workforce training investments, not to mention potential land acquisition, construction or renovation, and outfitting a facility with necessary machinery and equipment.
Beyond the initial set-up costs, another prospective challenge could include navigating cultural differences and facing possible regulatory issues. Regarding working with partners from other cultures, companies should consider investing in cultural awareness training for their employees to bridge these gaps and foster effective collaboration. Companies may also want to consider seeking legal counsel to mitigate the risk of regulatory troubles and financial penalties. By tackling these would-be challenges head-on, manufacturers could unlock the many benefits nearshoring can offer.
How Plastic Pallets Can Enhance Nearshoring Strategies
A successful nearshoring strategy requires careful consideration of various factors, including efficient logistics and material handling. This is where plastic pooling services can emerge as valuable assets. Efficient pallet pooling services can streamline nearshoring operations by handling procurement, storage, transportation, repair, and recycling — freeing businesses to focus on core activities. Furthermore, these services echo the cost-saving aspects of nearshoring by reducing overall expenses. Lastly, for those nearshoring initiatives prioritizing sustainability, pallet pooling contributes to environmental goals through the promotion of reuse and responsible recycling practices.
As more businesses adapt to a dynamic global environment, nearshoring is becoming an essential strategy for maintaining a competitive advantage.
Manufacturers considering shifting to nearshoring their operations can enhance their logistics operations by opting for iGPS plastic pallets. These pallets are engineered to seamlessly integrate with automated systems, ensuring a smooth flow in an increasingly AI-focused supply chain. For more information, contact us at 800-884-0225, email a specialist at switch@igps.net, or visit our contact page.