Key Takeaways
- Warehouse shipping may seem like a simple and straightforward process, but it’s not.
- Streamlining warehouse shipping is an ongoing challenge for logistics specialists.
- Methods to improve the warehouse shipping process include labeling and tracking; implementing automation; and improving equipment.
- Switching to safer, lighter plastic pallets can also streamline the shipping process.
How to Improve the Warehouse Shipping Process
Behind the seemingly straightforward process of warehouse shipping lies a potential minefield of delays. Imagine this: a customer clicks “order,” the warehouse management system (MMS) spits out a pick list, and a worker or automated system efficiently gathers the items. Boxes and pallets are packed, and everything seamlessly ships out on the next truck. It sounds simple, but it’s not.
Streamlining warehouse shipping is an ongoing challenge for logistics specialists, but small wins add up over time. It involves continually looking for small tweaks that shave seconds off each shipment, lower per-shipment costs, and add significant savings in the long run.
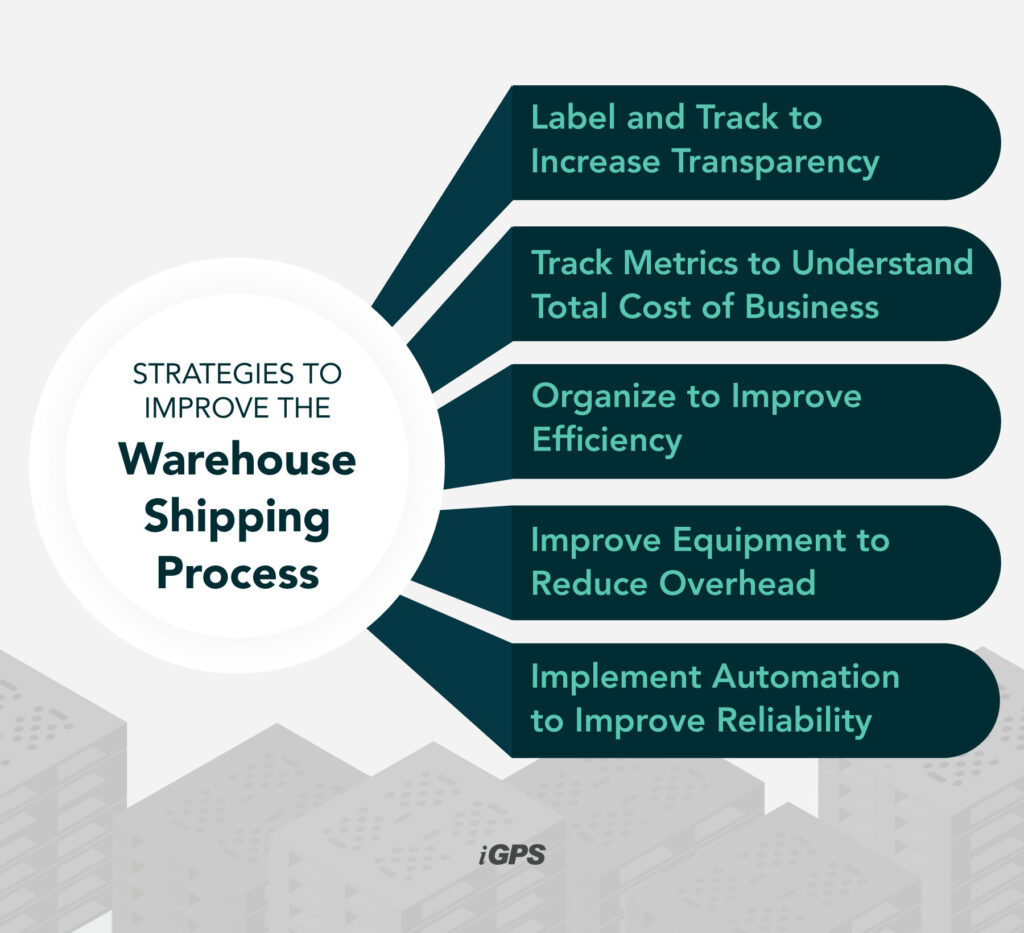
5 Tips on How to Improve the Warehouse Shipping Process
1. Label and Track to Increase Transparency
Keeping tabs on a sea of moving products can be a logistical nightmare. Here’s the rub: improper labeling throws a wrench into the well-oiled machine of warehouse operations. Picture a picker halfway through an order, forced to detour because a key item lacks a clear label. This disrupts the entire picking route, costing valuable time. In fact, warehouse picking errors can be costly, ranging from $10 to a whopping $250 per mistake according to Honeywell. The solution? A clear and consistent labeling system can eliminate these roadblocks and keep your warehouse running smoothly.
Warehouse wizards know clear labeling is the key to a speedy operation, and now technology makes labels machine-readable and easily recordable. GS1 standards, the business language of the supply chain, have been powering machine-readable barcodes since the 1970s. These track products throughout their journey. Radio Frequency Identification (RFID) uses GS1 identifiers too, which results in transformed stockrooms. Plus, real-time tracking systems like RFID can reduce picking errors; proper labeling and tracking makes products practically self-locate.
2. Understand Your Total Cost of Business
Using supply chain management software alongside machine-readable tracking simplifies data collection and comparison.
The software analyzes labor utilization, inventory levels, transportation efficiency, and even hidden costs like returns due to errors. This comprehensive cost analysis empowers managers to make informed decisions. Do they need to revisit their workflow and see where technology can lend a hand? Would optimizing storage layout be more beneficial? Ultimately, warehouse inefficiencies get exposed, and managers can address bottlenecks in intake and order fulfillment, boosting productivity and cost-effectiveness; this data becomes key to understanding a facility’s Total Cost of Business (TCOB).
3. Organize to Improve Efficiency
Warehouse tidiness matters. Keeping things clean and organized prevents disruptions in shipping processes. Even minor tweaks, like placing frequently picked items within easy reach, can give productivity a boost.
To maximize storage capacity within a facility, managers can implement deep-lane storage systems. These systems utilize high shelving with pallet racking, allowing for significant increases in product storage compared to traditional layouts. While installing deep lane racking temporarily disrupts operations and requires a temporary halt in some activities, the benefits can be substantial.
In today’s omnichannel environment, where businesses manage multiple sales channels and prioritize fast, accurate order fulfillment, a strategic reorganization can be a worthwhile investment. Facilities with well-organized layouts can experience an increase in picking efficiency. This efficiency gain translates directly to faster order fulfillment and potentially higher customer satisfaction.
4. Implement Automation to Improve Reliability
Human error is a major obstacle in the warehouse shipping process. Workers often rush to put products away, leading to misplaced items. With facility automation, the outcome is virtually always the same: consistent, reliable results. Automated Storage and Retrieval Systems (ASRS), AGVs, pallet shuttles, and palletizers enhance reliability and predictability. For example, automated case picking reduces errors in picking and palletizing, cutting down on costly returns and rush shipments.
5. Improve Equipment to Reduce Overhead
Warehouse enhancements typically zero in on making operations more dependable and consistent. Upgrading equipment can significantly reduce errors and delays in order fulfillment. For instance, improved warehouse lighting has increased worker productivity and reduced accidents. Switching to higher-quality pallets with angled entryways for forklifts and evenly supporting deck surfaces can prevent product damage and streamline operations. These small upgrades can boost efficiency and slash costs, ultimately enhancing efficiency and reduce the Total Cost of Business (TCOB).
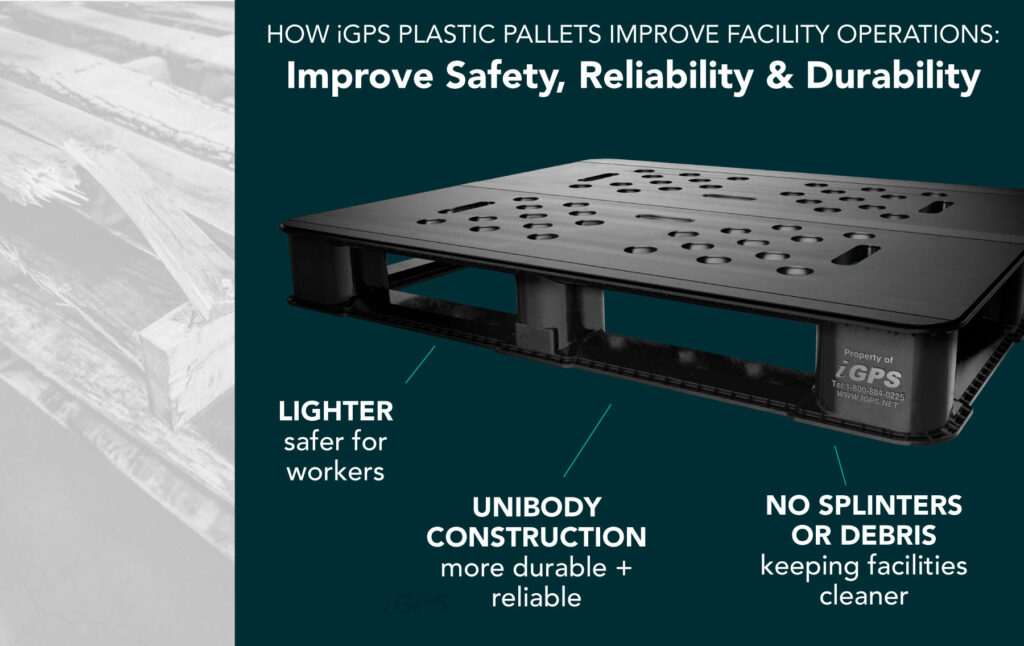
How to Improve the Warehouse Shipping Process with Pallets
While equipment upgrades can significantly impact efficiency, warehouse operations can be further optimized by focusing on the tools used daily by workers.
For example, switching to plastic pallets can significantly improve facility operations by enhancing safety, reliability, and durability.
Plastic pallets are lighter than wood, making them easier and safer for employees to handle. They’re also built to last. Unlike wood pallets, which leave splinters and nail debris behind, plastic pallets keep facilities clean and minimize the risk of injury.
One simple swap can unleash a cascade of benefits: opting for plastic pallets can deliver immediate benefits and streamline the warehouse shipping process in multiple ways.
In Conclusion: Frequently Asked Questions
How do you improve warehouse logistics?
To improve warehouse logistics, optimize the layout for efficient workflows, implement technology like barcode scanners and RFID, train staff on equipment and procedures, and partner with plastic pallet providers for lighter, safer shipping.
How do you optimize warehouse processes?
Focus on streamlining workflows, reducing manual labor, and improving accuracy. This can be achieved by implementing advanced technologies like automated guided vehicles (AGVs), using warehouse management systems (WMS) for real-time inventory tracking, and optimizing storage for efficient product flow.
What is the 5S method of lean warehousing?
The 5S method is a Japanese lean manufacturing technique used to improve workplace organization and efficiency. It involves five steps: Seiri (sorting), Seiton (set in order), Seiso (shine), Seiketsu (standardize), and Shitsuke (sustain).
Companies committed to improving their shipping processes can opt for iGPS plastic pallets. These pallets are lightweight, recyclable, and have embedded RFID tags. For more information, contact us at 1-800-884-0225, email a specialist at switch@igps.net, or visit our contact page.
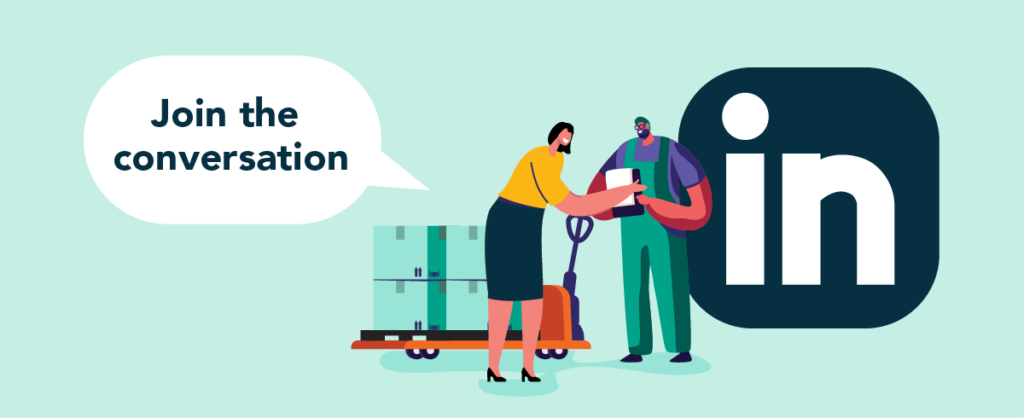