If you’re wondering how to keep track of pallets, you’re not alone. The ability to keep tabs on a pallet of goods as it moves through the supply chain is an enormous advantage for many industries, particularly those dealing with sensitive or perishable products, such as pharmaceuticals or fresh food. And as regulations mandating traceability such as the Drug Supply Chain Security Act (DSCSA) are put into place, being able to track a pallet is increasingly necessary.
Used, empty pallets can also create a logistical challenge, as operations managers must be able to locate them in order to return them to the warehouse or the beginning of the supply chain for reuse. One solution is a pallet management service, which can shift the administrative burden of tracking down and transporting empty pallets to a dedicated third party. In addition, technology now exists at the pallet level which, when used in conjunction with the appropriate software, makes it possible to follow individual pallets through the supply chain.
How to Keep Track of Pallets Using Technology
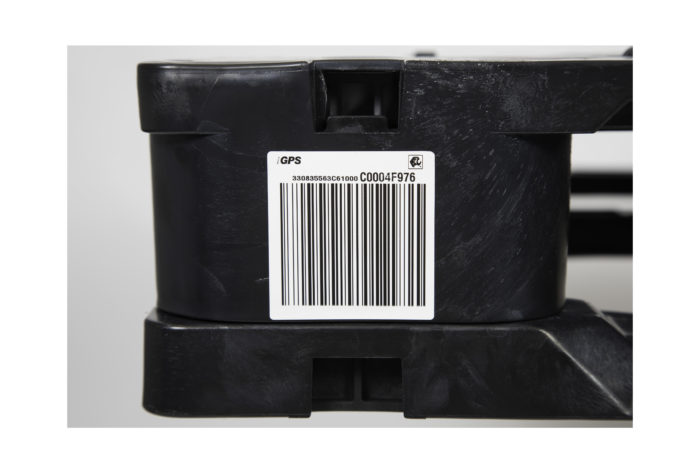
Successfully managing a pallet fleet requires consistently logging the whereabouts of each pallet, whether it’s on the back of a truck, at the retailer, awaiting unloading, or sitting on the warehouse floor. The logging process involves assigning each pallet a unique identifier and entering it into a computer system for tracking. A task like this would be impossible to manage manually, so managers turn to:
- Barcodes: Barcodes are used by grocery retailers to keep track of inventory and can be used at the pallet level as well. Unfortunately, they’re dependent on manual, line-of-sight scanning, meaning that only one item can be scanned at a time and it can be difficult to properly scan a barcode while the pallet is in motion.
- Radio-Frequency Identification (RFID): Like barcodes, RFID chips carry a unique identifier. They can be scanned during each stage of transport using near-field technology, which works across short distances and doesn’t require a line of sight. This makes it useful for scanning moving inventory as well as scanning many items at the same time.
- Both RFID and Barcodes: Combining both a barcode and RFID on a pallet ensures that it is trackable at every location, regardless of whether that location is equipped with an RFID reader.
- Inventory Management Software: Barcodes and RFID simply link each pallet to a unique identifier. That data isn’t useful without a centralized system to organize it and associate the details of a pallet’s journey with its identifier. Supply chain management software logs the pallet’s identifier as well as other details like the time the pallet was received or transferred, location, status, and involved personnel. Most systems are designed to work automatically, so that when an individual signs into the system and scans the pallet, its location and other details are automatically updated in the database.
RFID enables tracking with less effort than barcodes require.
Whether you choose barcodes, RFID tracking, or a combination of the two will depend on volume and tracking complexity. Both methods have their benefits; barcodes are more affordable and don’t require special equipment, while RFID enables tracking with less effort. Companies with a high throughput or those using a lot of automated equipment would likely do best with RFID or an RFID and barcode system.
Simplifying Logistics with Pallet Pooling
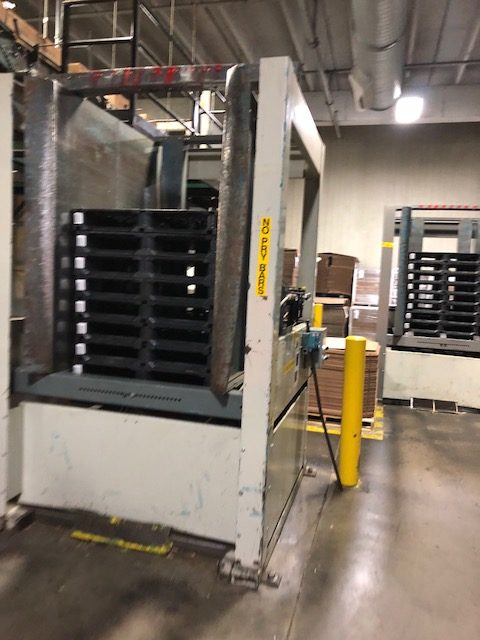
As every operations manager knows, reclaiming pallets at the end of the supply chain can be a frustrating logistical challenge which requires coordinating the return of pallets from their end location in a way that wastes as little time, labor, and fuel as possible. The challenge of reclaiming pallets is one reason why many companies choose to use flimsy one-way, single-use pallets that they abandon at the end of the supply chain after one use.
If you’re looking for a reliable way to keep track of pallets, seek out a high-quality pallet pooling program.
Pallet pooling offers an alternative to this practice and to the administrative hassle of tracking down and transporting empty pallets. By renting pallets, rather than purchasing them outright, managers can minimize the costs and logistics associated with maintaining a fleet, enabling them to focus on their core business. Rather than having to determine when it is most cost-effective to send a truck to reclaim empty used pallets–which often results in a dead leg–managers can instead rely on the pooling service’s wide network of depots and customers, which allows the pooling provider to efficiently manage a large pallet fleet.
If you’re looking for a reliable way to keep track of pallets, seek out a high-quality pallet pooling program that offers pallets that are both barcode- and RFID-enabled. A combination of RFID tracking technology and pooling is the best answer to the question of how to keep track of pallets. RFID-enabled pooled pallets, along with scanning equipment and proper logging policies, can ensure that you always know where your products are and always have the empty pallets you need.
iGPS rents GMA spec plastic pallets enabled with both RFID and barcode tracking to simplify your logistics and lower your Total Cost of Business (TCOB). For more information on our options, contact us at 1-800-884-0225, email a specialist at switch@igps.net, or visit our contact page.