In the grocery supply chain, mold isn’t just inconvenient and unsightly. It can contaminate products, lead to costly recalls, and lower retailer confidence in your product. Knowing how to prevent mold on pallets could be the difference between a rejected load–and the accompanying fines–and an easy delivery. Supply chain managers should ensure that their pallet processes are designed to minimize the risk of mold contamination.
Reducing this risk starts with proper pallet maintenance. Mold can’t grow without moisture, so mold prevention should focus on making sure wood pallets don’t stay wet and that proper cleaning, drying, and storage practices are followed. Alternatively, supply chain managers may want to consider switching to pooled plastic pallets. Plastic platforms are particularly mold-resistant, making maintenance and storage simple.
How to Prevent Mold on Pallets
Combating mold on wood pallets is a challenge because wood is porous. Even thoroughly drying the surface of the pallet won’t necessarily prevent the growth of mold when moisture has seeped deep into the wood. In most cases, it’s also not possible to completely avoid getting pallets wet. In the supply chain, moisture can collect on pallets through many means, from a humid loading dock or warehouse to an accidental spill. The simple act of moving a pallet from an air-conditioned environment to a much warmer one is enough to cause condensation to form on a platform’s surface. While it’s not possible to keep pallets dry all the time, there are ways for supply chain managers to proactively combat the formation of mold.
- Choose wood pallets made from kiln-dried lumber: Many pallets are made using green or wet wood, which contains natural moisture that can promote mold growth on the pallet even if it isn’t exposed to damp conditions. Kiln-drying is part of the wood curing process; it removes most of the natural moisture from the wood and also limits its absorbency. However, pallets that get wet after the kiln-drying process may still become moldy.
- Use industrial fans: Industrial drum-type fans are useful for improving airflow around pallets. Fans can be placed in areas where pallets are sorted and stacked prior to going into longer-term storage. Improving air movement around the pallets gives moisture less time to settle into the wood. It also discourages mold from taking hold, since constant air movement makes mold spores less likely to settle on pallets and grow.
- Clean wood pallets regularly: Cleaning wood pallets ensures that most mold spores are removed from the surface before they have a chance to grow and spread. Pressure washing is the simplest way to eliminate spores that have landed on the wood.
- Ensure airflow in storage: Following pressure washing, it’s crucial that wood pallets be allowed to dry completely before being placed into storage. It’s also important to store pallets in areas with good airflow and low humidity; avoid storing wood pallets in trailers, where the air is often warm, humid, and stagnant.
It can be difficult to eliminate mold on pallets due to the natural absorbency of wood.
Even with all these efforts in place, it can be difficult to eliminate mold on pallets due to the natural absorbency of wood. In some cases, such as in humid locations or in the cold chain, the best way to prevent mold is to switch to a non-absorbent pallet material like plastic.
How Plastic Pallet Pooling Solves the Problem of Mold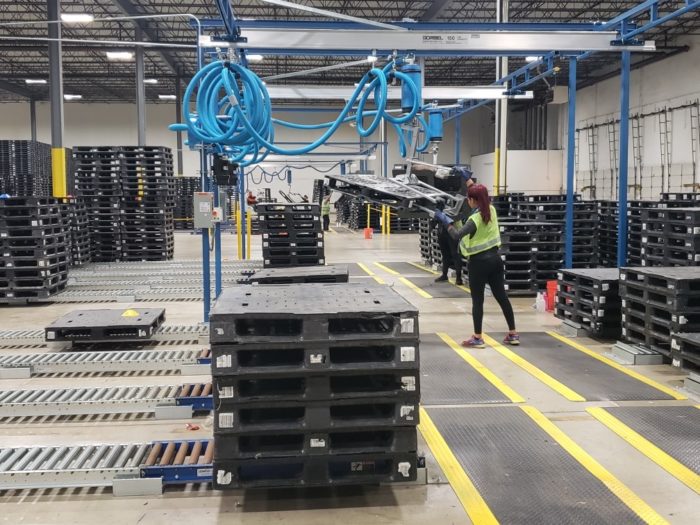
Plastic pallets have one clear advantage over wood when it comes to combating mold issues: plastic is a non-porous material, so the only moisture supply chain managers need to worry about is on the surface. Taking reasonable precautions, such as letting pallets dry before stacking them and storing them in a cool environment, will significantly reduce the risk of mold with no chemical or heat treatment needed.
Plastic pallets are non-absorbent and easy to keep dry.
Choosing to rent plastic pallets through a pooling provider also lessens the burden of pallet maintenance and mold prevention. Pallet pooling companies will wash pallets, when necessary, between supply chains, and will have protocols in place for ensuring all pallets are cleaned and dried in a way that reduces the risk of mold growth.
The only real way to prevent mold on pallets is to eliminate moisture. Wood pallets offer an extra challenge since they’re porous; for these pallets, extra time and effort is needed to avoid mold. Plastic pallets, on the other hand, are non-absorbent and easy to keep dry–and, therefore, free of mold. Supply chain managers can outsource much of their mold control efforts by working with a plastic pallet pooling company.
Renting iGPS plastic pallets is an ideal way to avoid issues with mold on pallets and ensure that your shipments are protected. For more information, contact us at 1-800-884-0225, email a specialist at switch@igps.net, or visit our contact page.