ARTICLE UPDATED ON JANUARY 31, 2024
The journey of Kaizen business strategies has been remarkable since Toyota pioneered them in Japan’s post-war reconstruction in the late 1940s. It was Toyota’s integration of Kaizen into its foundational “Toyota Way” principles that many believe set the gold standard for lean manufacturing. Kaizen approaches not only center on waste reduction but also emphasize ongoing improvement. These strategies are rooted in the belief that perfection is a moving target, and by consistently identifying and resolving issues, employees can progressively bring processes closer to perfection.
Today, Kaizen finds application across a broad spectrum of industries, but it tends to excel in manufacturing and warehouse settings. These environments often entail repetitive tasks that can be dissected into processes where minor adjustments can lead to substantial enhancements in productivity. These adjustments might involve altering the method of performing a step or modifying the tools employed to support those steps. Kaizen concepts tailored to facility operations, which can be as simple as transitioning to a different type of shipping pallet, can trigger positive improvements within the supply chain.
The Elements of Kaizen Business Strategies
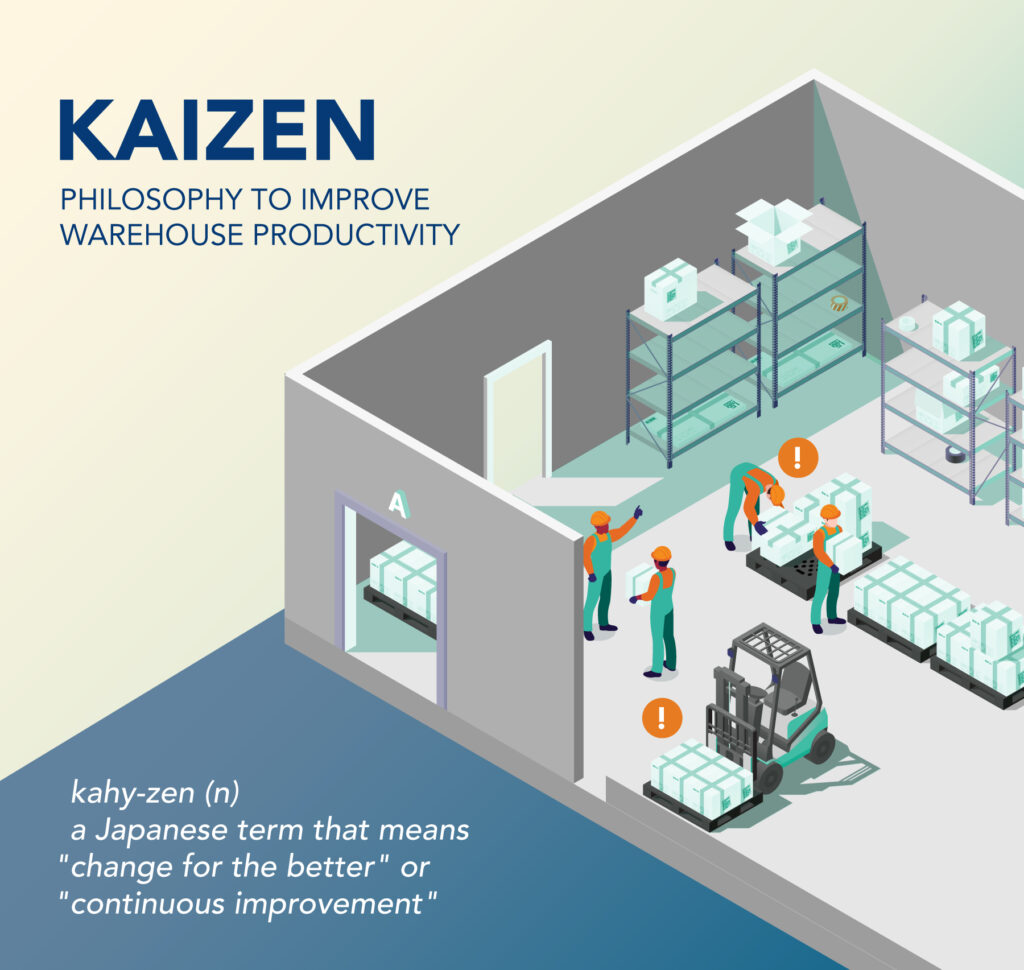
Kaizen, a Japanese term that means “change for the better” or “continuous improvement,” is not just a philosophy but a set of strategies that can transform the way businesses operate. The approach focuses on fostering a culture of continuous improvement within an organization. That means that Kaizen strategies are not a series of steps, but rather a cycle that is broken down into four stages, repeated indefinitely:
- Plan: Review the current state of operations and set goals, as well as suggest changes for reaching them.
- Do: Get key stakeholders on board and put the plan into action.
- Check: Review the results and compare them to prior data.
- Act: Report results, fix problems, and return to the planning stage.
This cycle, often abbreviated to PDCA, ensures manufacturers can take advantage of industry innovations. Upon the introduction of a new technology or service, enterprises can determine how it fits into their current processes and whether it can be used to boost efficiency. In this way, Kaizen can be invaluable for creating strategies that leverage new resources to eliminate common warehouse inefficiencies.
Warehouse Inefficiencies and Causes of Production Delays
Before implementing Kaizen ideas in a warehouse or fulfillment center, it’s important to determine where inefficiencies most commonly occur. While every facility is different, throughput is often affected by the following:
- Equipment disruptions: Automation in warehouse processes is crucial to efficiency, but when these systems break down, they can create significant production delays.
- Employee injuries: In 2021, the warehouse and storage industry’s injury rate was 5.5 per 100 full time employees. Injured employees may need to take time off work or go on light duty restrictions as they recover, which heavily impacts productivity.
- Rejected loads: When a retailer or distributor rejects a load of product, employees must return the truck to the facility, repack it and send it out again, resulting in damaged inventory, higher transportation costs, and wasted working hours. When rejected goods have short shelf lives, as in dairy and produce deliveries, the entire load is often lost.
- Conveyance: The more frequently inventory is handled, the higher the risk of product damage. Moving inventory around the warehouse due to space issues or poor planning also wastes working hours, lowering the productivity of the facility as a result.
Kaizen methods examine these problems by addressing the process that caused the issue. In many cases, a single step in a process may contribute to multiple problems. By changing that one factor, many inefficiencies can be reduced or eliminated.
Kaizen Ideas for Warehouse Management: Why Focus on Your Pallets
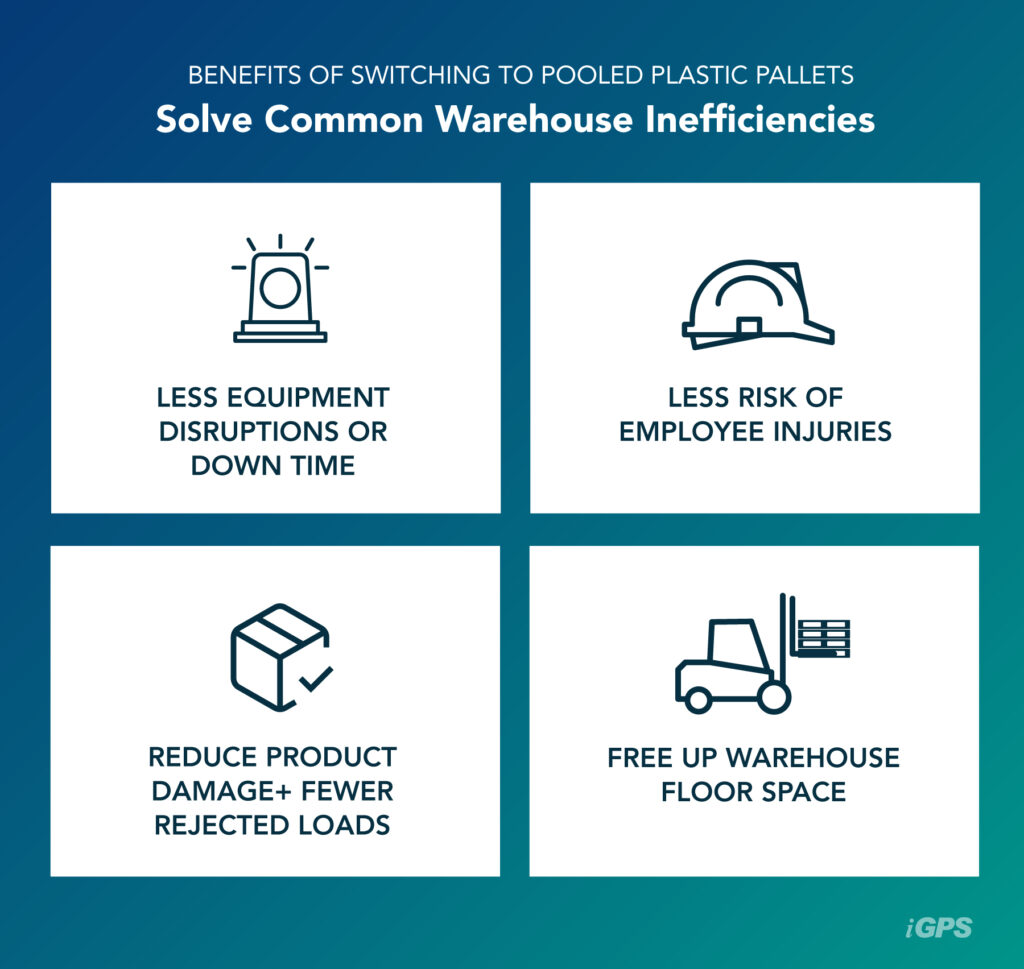
When conducting a kaizen assessment of a warehouse, fulfillment center, or other facility, managers often notice that simple changes make the biggest impact on productivity. For example, a small change, like switching to a plastic pallet pooling model, can create a noticeable improvement in many areas. In pallet pooling, manufacturers rent pallets from a shared pool used by other manufacturers. This eliminates the upfront cost of pallet purchase and allows facilities to scale their programs as needed based on seasonal demand changes.
The success of a pallet pooling program relies heavily on the quality of pallets in the pool. The use of durable reusable plastic pallets in pooling is ideal when looking to boost supply chain efficiency. Plastic pallet pooling can reduce:
- Equipment disruptions: PlaPlastic pallets are gentler on equipment as they don’t leave behind wood debris which can clog or damage sensitive machines. Plastic pallets are lighter as well, which reduces overall wear and tear on the machinery. Engineered plastic pallets also offer consistent weight and dimensions, making it easier to calibrate automated equipment.
- Employee injuries: Lightweight plastic pallets are easier for employees to handle manually and also reduce the risk of lifting injuries, which are common for warehouse workers.
- Rejected loads: Retailers often reject loads shipped on wood stringer pallets because these pallets are prone to break, which can cause product damage. Plastic pallets, on the other hand, are accepted industry-wide because they are durable, easy to clean, resistant to contamination, and keep the product shipped on them safe and intact.
- Conveyance: By using a plastic pooling provider, warehouses can free up floor space, which eliminates the need to shift inventory around to make room on crowded floors.
By replacing traditional wood pallets with pooled plastic pallets, facility managers can simultaneously address several common causes of warehouse inefficiencies. This strategy supports the Kaizen philosophy of continuous improvement as it allows a facility to make a small change that ultimately results in significant improvements. Any logistics manager aiming to improve their facility’s processes should consider switching to high-quality pooled plastic pallets.
Kaizen strategies are a powerful way to instill a culture of continuous improvement within a supply chain facility. Ultimately, the commitment to improving and the embrace of Kaizen as a way of conducting business can lead to lasting success and growth for any organization.
Companies looking to boost supply chain efficiency should consider using iGPS plastic pallets for all their shipping needs. Our lightweight, recyclable plastic pallets flow seamlessly through automated systems and reduce the Total Cost of Business. For more information, contact usat 1-800-884-0225, email a specialist at switch@igps.net, or visit our contact page.
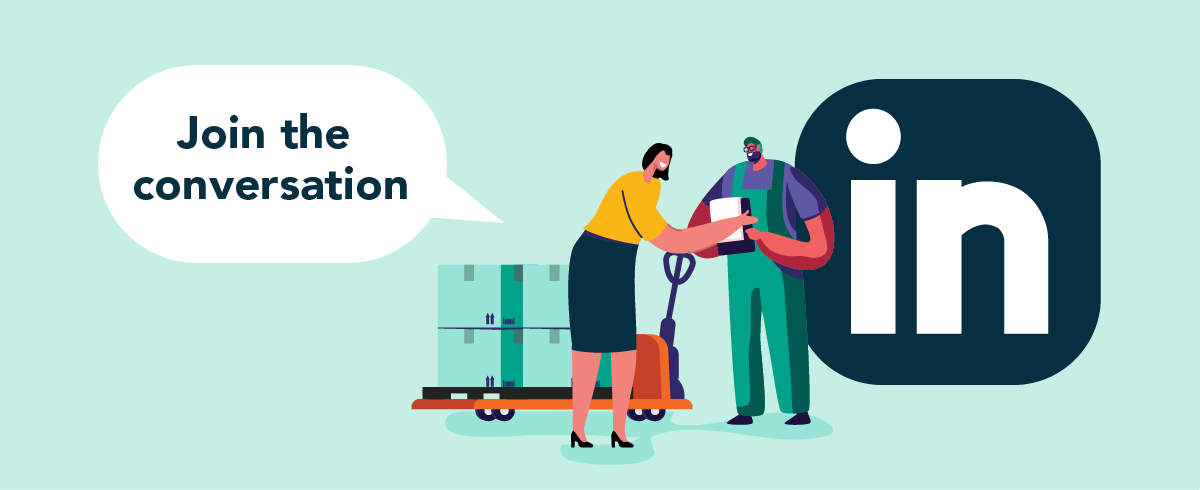