Reduce Product Damage Case Study
How Zirkle Fruit Reduced Product Damage
Fruit is a highly sensitive and perishable product, and the fruit supply chain requires a considerable footprint. Zirkle’s holdings include, for example, a cherry-processing facility covering more than 85,000 square feet. Traditional wood pallets are difficult to keep clean, and shed nails and splinters that can damage fruit, jam automated processing equipment, and cover the floors of trucks and warehouses in debris that must be swept up. And every damaged pallet that is returned by a retailer costs Zirkle Fruit money
Zirkle Fruit is a fifth-generation company that has been farming in Selah, Washington since the 19th century. The company and its subsidiaries and partners farm and distribute top-quality apples, blueberries, wine grapes, and cherries. Its Selah facility processes more than 9 million boxes of farm-fresh apples each year. Choosing the right kind of shipping pallet, was critical to reducing product damage and overall costs.
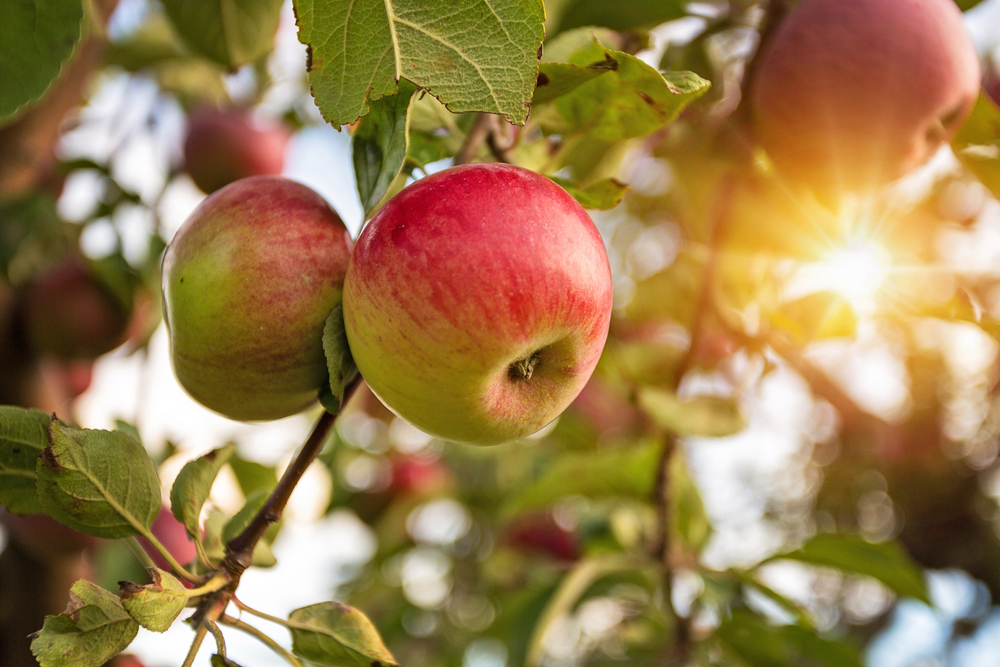
iGPS began supplying its lightweight, sanitizable pallets at Zirkle’s Selah facility. The company quickly recognized the benefits of the iGPS plastic pallet, which is lighter than a typical wood-block pallet and about four times as durable. During the first year of operation, iGPS was supplying a relatively small number of pallets, but the volume has more than tripled over the past several years.
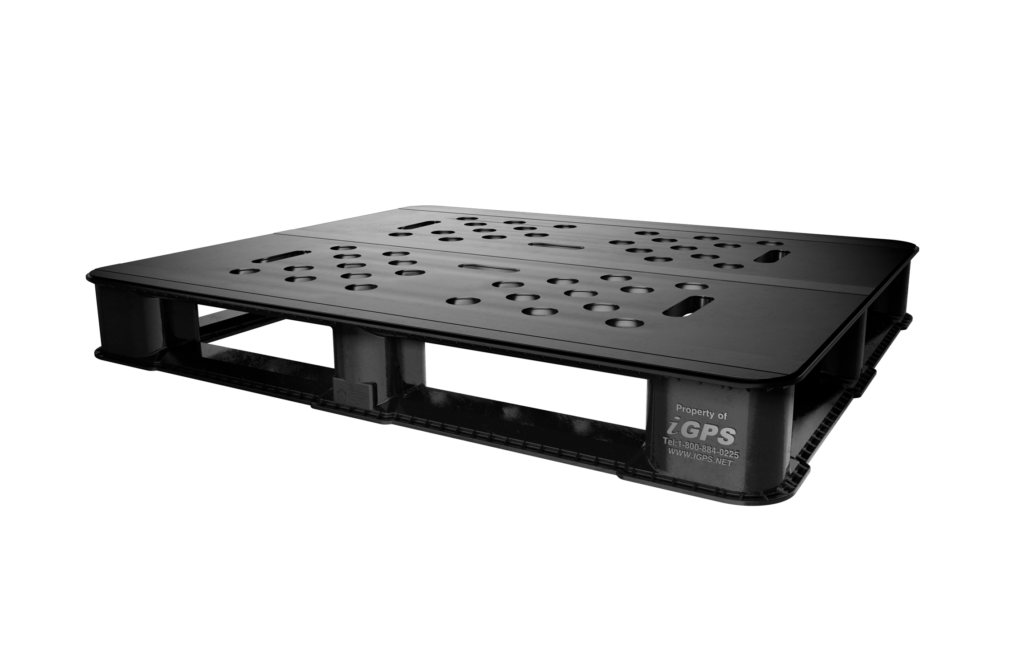
Since coming aboard as an iGPS client, Zirkle Fruit has benefited from an improved and more responsive retailer experience, as well as positive business results. During a typical month, the company sees as many as 20 wood pallets rejected by retailers due to damage. However, due to the iGPS pallet’s increased durability and absence of nails, in an average month, there can be as few as zero returns. Zirkle Fruit has also benefited from less product waste since iGPS pallets are cleaner and less likely to bruise and puncture fruit. The lighter weight of the iGPS pallets also means they are safer for employees and consume less fuel during shipping. And because the pallet does not shed splinters, debris on warehouse floors and clogged in automated processing equipment is now a thing of the past.