Dust. It’s a nuisance in the warehouse environment; clinging to clothes, settling on products, and creating a health hazard for employees. While keeping a facility perfectly dust-free might appear to be an elusive target, there are effective strategies that can drastically cut down on the dust particles and pave the way for a cleaner, more secure working environment.
Dust bunnies in your warehouse aren’t just a cosmetic issue but a health hazard. Warehouse dust is a cocktail of nasty particles, including soot from forklifts, mold spores, pollen, and even debris from pests. These airborne irritants can cause everything from respiratory problems to allergic reactions. A variety of best practices can help cut down on dust for the protection of both people and products.
Reduce Dust in Your Warehouse by Keeping Work Areas Clean
Regular facility cleaning is the cornerstone of dust control. But sporadic cleaning schedules and inconsistent efforts often leave warehouses cloaked in a dust blanket. To keep the dust down, it’s essential to have everyone clean up at the end of their shifts. To minimize dust levels, make sure of the following:
- Employees Are Trained on How to Clean Their Work Areas
Warehouses, fulfillment centers, and other logistics facilities contain complex machinery and hard-to-reach spots that often gather dust unnoticed. This accumulated dust becomes visible again when machinery and personnel resume operations the following day. Informing employees about these locations enables them to effectively sweep or vacuum the accumulated dust during daily clean-ups, minimizing debris and particulate levels in the warehouse.
- Employees Are Responsible for Their Work Areas
Training employees on cleaning procedures is just the first step. Make sure they understand their designated cleaning zones and hold them accountable for keeping these areas dust-free. This should be a core part of their daily tasks.
- Supervisors Are Responsible for Their Employees
Great cleaning procedures won’t work without follow-through. Regular inspections by supervisors, including those hard-to-reach areas, will ensure employees are properly removing dust and debris from their assigned zones.
Inconsistent cleaning is the real enemy of warehouse and facility dust. Vague cleaning procedures and infrequent schedules create the perfect environment for dust to thrive. You can significantly reduce particle levels by setting clear cleaning protocols and ensuring employees consistently follow them. If your warehouse has a history of infrequent cleaning, a complete shutdown for deep cleaning might be necessary to eliminate dust buildup.
Warehouse Dust Suppression Equipment
Although there are warehouse dust suppression systems available, their setup, operation, and maintenance costs are relatively high, making them more suitable for industries with substantial dust hazards. These systems actively work to either remove or suppress dust particles in the air.
In contrast, the electronics industry requires a different approach. With electronics, virtually invisible dust particles can be a menace to sophisticated equipment, making it an absolute must to eradicate all traces of dust. Here’s a breakdown of the three main categories of warehouse anti-dust systems:
- Fogging Systems: Fog cannons keep dust at bay with a constant, gentle mist. Tiny water droplets collide with airborne dust, drawing it down to the ground. This method effectively prevents grain dust explosions, a significant safety hazard.
- Ventilation Systems: Dust suppression ventilation systems are like air wranglers. They use extractor fans to pull air through filters, trapping dust particles before pumping the clean air back into the warehouse. Harnessing the power of extractor fans, they effectively sweep dust particles from the ambient air, fostering a remarkably pristine atmosphere within the warehouse.
- Partitioning: Partitioning systems create impermeable barriers that prevent dust from migrating between different areas. This is ideal for keeping outdoor dust or dust generated during specific processes from reaching sensitive parts of your warehouse.
Warehouses and other logistics facilities require specific dust control solutions based on their needs. Fogging systems, commonly used in bulk grain facilities (where grain dust is part of the product), aren’t ideal for other facilities. Settling dust creates extra cleaning and can raise humidity levels, potentially leading to mold growth. While effective for clean rooms, dust-filtering ventilation systems are too expensive for most warehouses. These intricate systems require continuous operation and frequent maintenance of filters, making them a significant cost factor.
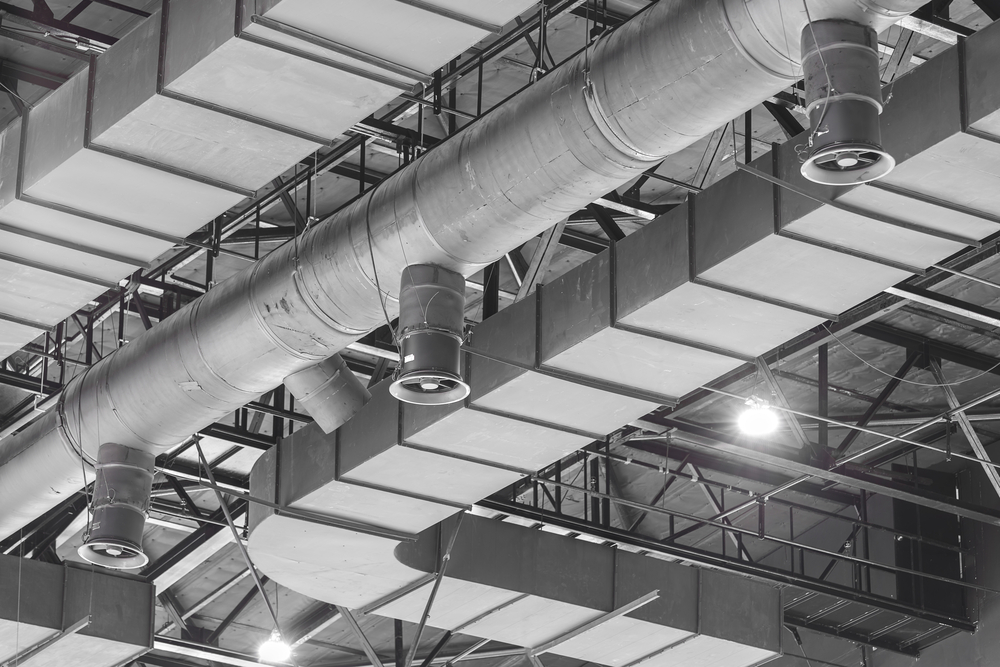
Partitioning, a more cost-effective solution, isolates sensitive areas from dust. Warehouses in the food and dairy sectors often use simple hanging plastic sheets. However, partitioning should be combined with efforts to minimize dust generation at its source for optimal effectiveness.
Reducing One Common Source of Dust in Your Warehouse
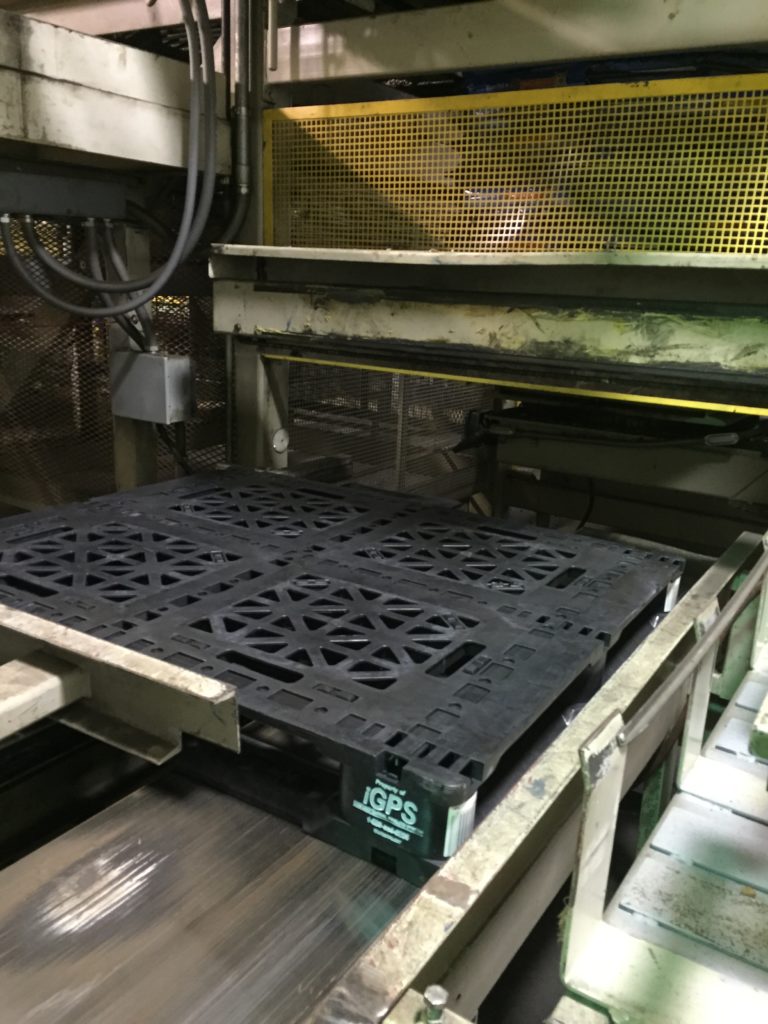
While dust infiltration in warehouses can have many origins, one often-overlooked source is the ever-present wood shipping pallet. Over time, these pallets naturally degrade. The constant friction caused by heavy loads being placed and removed or by powerful machinery navigating the warehouse accelerates this degradation. This breakdown weakens the wood fibers, causing them to fray or break loose, ultimately causing the accumulation of dust and debris throughout the warehouse. Warehouses prioritizing a clean and controlled environment should seriously consider minimizing the use of wood pallets in these areas. Alternative pallet materials or implementing a strict pallet inspection and replacement program can significantly reduce dust generation from this source.
Warehouses aiming to reduce dust may consider plastic pallets as an alternative to wood. They are generally more resistant to breakage and dust generation from friction caused by heavy loads or machinery compared to wood. Additionally, the single-piece construction of plastic pallets may contribute less to debris and fragments that ultimately become airborne dust.
Manufacturers seeking to reduce dust in their warehouses can opt for iGPS plastic pallets for their logistics operations. Our shipping platforms have no protruding nails or splinters, so they flow easily through automated systems. For more information, contact us at 800-884-0225, email a specialist at switch@igps.net, or visit our contact page.