Key Takeaways:
- The efficient movement of products is essential to a well-managed supply chain, not only on the open roads but inside logistics facilities.
- AGVs and other robot-guided transportation technologies use special sensors that let them navigate their environments safely and without human guidance.
- The advantages of AGVs include increased efficiency, improved accuracy, and enhanced safety.
- AGVs, which include forklifts, tuggers, and other types, also enable greater cost savings and scalability.
- Other transport technologies include robotic picking systems and collaborative “cobots”. Together, these solutions increase supply chain visibility and sustainability while reducing lead times.
The Power of Transportation Technology
The efficient and timely movement of goods is, of course, essential to the optimization of a well-managed supply chain. This is true not only in the arena of intramodal transportation, but also inside the walls of warehouses, fulfillment centers, and other facilities involved in logistic operations.
As facilities become increasingly reliant on automation, the advent of transportation technology — including autonomous guided vehicles (AGVs) and other robot-guided transportation solutions — has revolutionized warehouse operations and dramatically increased overall efficiency.
AGVs: A Game-Changer in Facility Operations
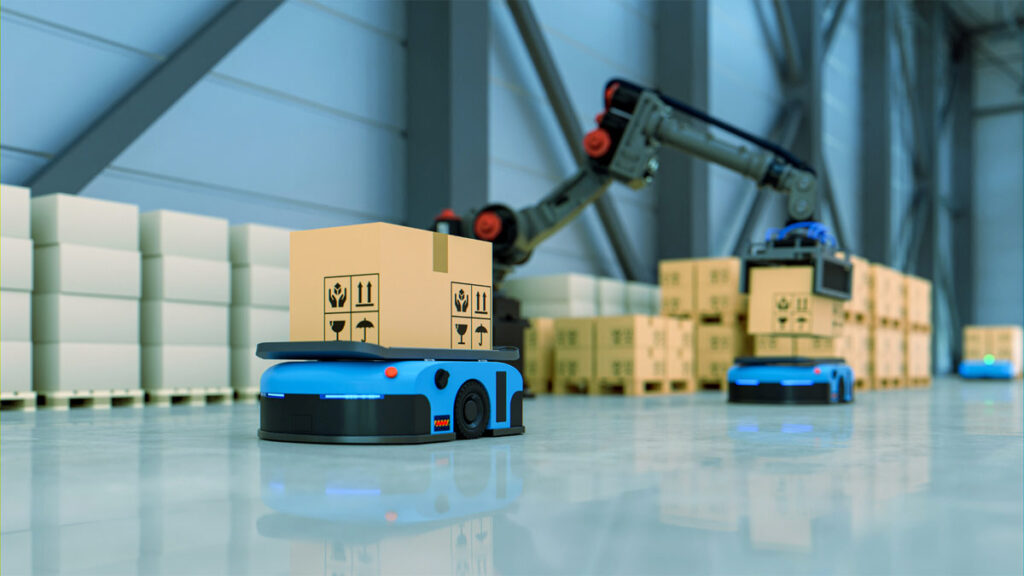
Autonomous guided vehicles have transformed the movements of products and raw materials within facilities of every size. These self-driving vehicles are equipped with specialized sensors and sophisticated software that enable them effortlessly to navigate their environments without human guidance or intervention. AGVs can be programmed to follow specific routes, to pick up and drop off pallets and other materials, and even to interact with pallets and other facility equipment.
The advantages of AGVs are numerous:
- Increased Efficiency: AGVs can operate 24 hours a day, seven days a week, without fatigue or the need for human breaks or shift changes. This leads to significantly increased productivity and ultimately, faster order fulfillment times.
- Improved Accuracy: Because they are not subject to the nuances of human error, AGVs are highly accurate and can reduce the occasional issues associated with manual operations, even by experienced drivers. This reduces the possibility of misplacements and other inventory discrepancies within a facility.
- Enhanced Safety: According to OSHA, between 35,000 and 62,000 injuries involving forklifts occur each year. The number of deaths has also increased over the past ten years. By automating the potentially hazardous operation of a warehouse vehicle, AGVs reduce the risk of collisions and other accidents that can cause injuries.
- Cost Savings: By reducing human labor costs, improving inventory management and accuracy, and minimizing the possibility of accidents as well as damage to products and equipment, AGVs contribute to improved supply chain cost management.
- Scalability: Without the constant need to hire or dismiss human operators, a fleet of AGVs can be easily scaled up or down to meet evolving demand as operational needs change.
Types of Autonomous Guided Vehicles
A bustling warehouse or fulfillment center can be populated by a variety of AGVs, each with its own unique capabilities that make it essential for the specific task at hand. Unit load carriers, for example, are designed to transport individual pallets or containers. By scanning the RFID tags embedded within a pallet, such as a lightweight iGPS plastic pallet, they can even determine where a particular pallet belongs, all without requiring direction from a human operator.
Tuggers are used to pull trailers and carts, which enables them efficiently to transport bulk materials throughout a facility. Some of these machines can pull several tons of materials at a time.
AGVs equipped with forklifts, meanwhile, can be used to load and unload pallets from racks and shelving systems. AGVs can also be integrated with conveyor systems to create a seamless flow of products and materials throughout a facility. And using sensors and AI, all of these different transportation technologies can move through facilities without colliding with equipment, racking systems, human beings, and each other.
Additional Technology Transportation Solutions
In addition to AGVs, supply chain facility managers are increasingly adopting other robot-guided transportation solutions to streamline their operations. These include
- Automated Storage and Retrieval Systems (ASRS): ASRS combines systems for automated storage with solutions for automated retrieval, which optimizes space utilization and quick and easy access to inventory.
- Robotic Picking Systems: These systems use robots with highly maneuverable arms to pick individual items from shelves or bins, which reduces the need for human labor while also improving accuracy. Many robotic systems can move around the facility, making them an additional type of AGV.
- Collaborative Robots (Cobots): Cobots are designed to work alongside human workers, sharing tasks and optimizing productivity. For example, e-commerce giant Amazon has experimented with sophisticated bipedal robots that can move and handle items in ways that enable them to collaboratively work with human workers to increase their speed and efficiency.
Additional Benefits of Transportation Technology in the Supply Chain
The advantages of reduced human labor, increased accuracy and safety, and enhanced productivity are undeniable. But the benefits of AGVs and other robot-guided systems extend beyond the walls of warehouses and other supply chain centers. For example:
- They Improve Supply Chain Visibility: AGVs and other transportation technology can provide supply chain managers with real-time insights regarding the location and status of goods throughout one or multiple facilities, enabling enterprises to make educated decisions and respond quickly to evolving situations.
- They Reduce Lead Times: In the Amazon age, consumers have become accustomed to receiving goods more quickly than ever. By streamlining supply chain operations, transportation technology can help reduce processing and delivery times and ultimately result in heightened customer satisfaction and a stronger competitive advantage.
- Enhanced Sustainability: Consumers in recent years have demanded that manufacturers and retailers adopt greener solutions that are better for the planet and its inhabitants. Transportation technology helps contribute to organizational sustainability goals by reducing fuel and energy consumption, decreasing greenhouse gas emissions, and minimizing overall waste output. When paired with sustainable shipping platforms, such as lighter, recyclable iGPS plastic pallets, these technologies become even more environmentally friendly.
The Future of Transportation Technology in the Supply Chain
Transportation technology continues to march forward; advances that once seemed like the stuff of science fiction are now increasingly common. While humans continue to play important roles in all facilities and likely will for some time to come, we may even be moving toward a future in which some warehouses are entirely robot-automated, not even requiring lights to operate. Other potential innovations include:
- Increased integration of AGVs with other warehouse automation technologies, such as automated sorting systems and robotic packaging machines.
- The development of AGVs that operate in more complex and dynamic environments than those found in typical warehouses, such as outdoor spaces (this is already happening in the construction industry, for example) or areas with mixed vehicular traffic.
- The increased use of AI to enable AGVs to continually learn and adapt to changing conditions, rather than simply following predetermined routes and motions.
While we can’t know with certainly what the future will hold, there is no doubt that these advances will continue at a breakneck pace, as organizations jostle for market share and competitive advantage while identifying how best to lower their total cost of business.
Frequently Asked Questions
What is transportation technology in warehousing?
Transportation technology in warehousing refers to the tools and systems used to move goods efficiently within and outside warehouse facilities. These technologies can include forklifts, conveyor belts, automated guided vehicles (AGVs), and warehouse management systems (WMS). They help streamline operations, reduce labor costs, and improve overall productivity.
What other new technologies are used in distribution centers?
Besides AGVs, warehouses also employ automated storage and retrieval systems (ASRS) for efficient storage and retrieval of goods. These systems use robotic arms or cranes to move pallets or individual items between storage locations. Additionally, some warehouses employ automated packaging machines to speed up the packaging process and reduce labor costs.
Beyond warehousing, what are the main types of transportations in logistics?
Beyond warehousing, logistics involves various modes of transportation. Trucks are widely used for road transportation, while trains offer efficient bulk transportation over long distances. For urgent shipments or perishable goods, airplanes are suitable. Ships are used for transporting large quantities of goods internationally, and intermodal transportation combines multiple modes, often using containers for seamless transfer.
Manufacturers looking to make their facilities more automation-friendly use iGPS plastic pallets. These pallets maintain a consistent size and weight, and don’t shed nails and splinters that can jam automated equipment. For more information, contact us at 1-800-884-0225, email a specialist at switch@igps.net, or visit our contact page.