When supply chain managers think about warehouse injury prevention, they’re often primarily focused on serious injuries that put lives at risk. However, these aren’t the only workplace injuries that should cause concern. Minor sprains, strains, cuts, and bruises can have a marked, detrimental impact on a company’s bottom line by slowing down productivity and reducing workplace morale. Fortunately, preventing warehouse injuries isn’t difficult and some simple changes can significantly reduce minor accidents.
Why Small Injuries Matter
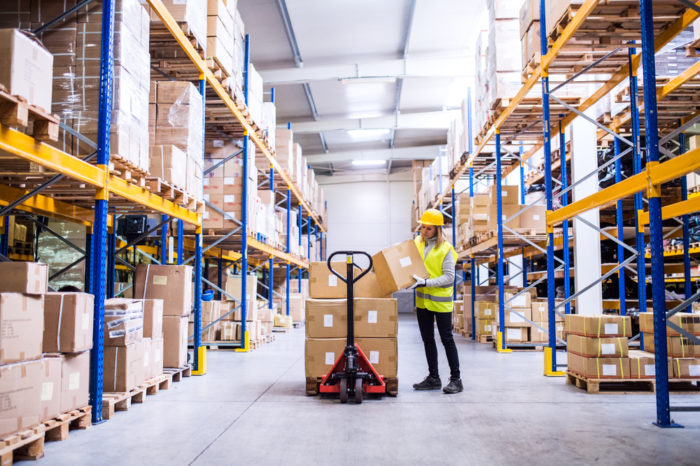
While it’s important to give priority to injuries that could put lives at risk, most warehouses already have extensive regulations in place to prevent accidents that might cause serious bodily harm. It’s much less common for facilities to introduce protocols designed to reduce minor injuries. Yet, while these types of injuries might not be life-threatening, they can disrupt productivity and have major repercussions for employees and for a workplace’s profitability. Some examples are:
- Sprains and strains: Sprains and strains can occur from exertion, and may be a result of repetitive movements. They typically occur in the lower back for warehouse workers, and one of the most common treatment regimens is light duty. It can take anywhere from several days to a month for these injuries to resolve, meaning that a worker will not be able to manage many of his or her tasks during that time.
- Cuts and splinters: Cuts and splinters in the warehouse may seem minor, but they can lead to serious infections within a non-sterile warehouse environment. For workers with pre-existing conditions, like diabetes or a suppressed immune system, a simple splinter could turn into a major, life-threatening illness. There’s also a risk that someone with a cut could contaminate products, resulting in product loss.
- Slips, trips, and falls: It’s difficult to keep a warehouse floor clean and tidy all the time. Debris, spills, and clutter all present obstacles for employees that could result in injuries. While most slips and falls result in fast recoveries, falling in the wrong way or the wrong place could cause more serious issues that might take months of recovery.
Supply chain managers should focus on the smaller changes they can make to improve warehouse safety.
Small injuries can add up to high costs when it comes to reduced productivity, insurance premiums, and overall morale. At the same time, it can be difficult to justify major upgrades to prevent them. That’s why supply chain managers should focus on the smaller changes they can make to improve warehouse safety.
Simple, Easy-to-Implement Warehouse Injury Prevention Tips
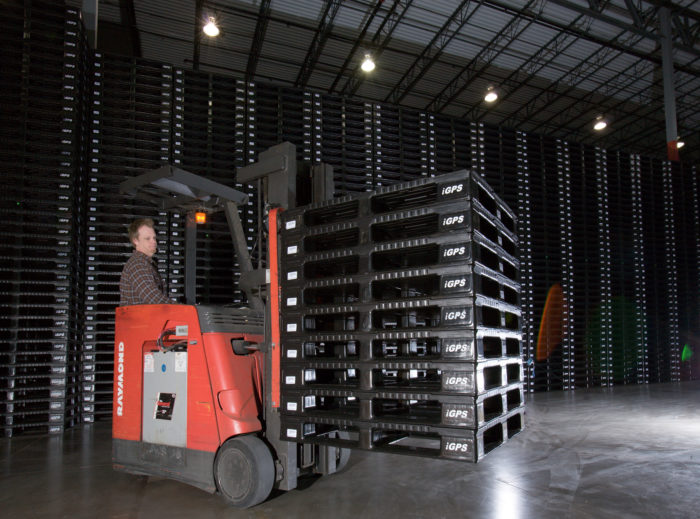
Many minor warehouse injuries come from handling pallets and products. It’s not always possible to eliminate the need to handle these items manually; however, it is possible to make items easier to handle and to protect employees as they work. Here are a few of the simplest and most effective ways:
- Switch to plastic pallets: Plastic pallets offer several advantages over wood that minimize common injuries in the warehouse. First is their light weight. Plastic pallets are usually under 50 pounds, meaning it’s safe–and in accordance with OSHA recommendations–for a single worker to handle them without assistance as long as they follow proper lifting protocols. Unlike wood pallets, plastic pallets also have a smooth unibody construction. That means there are no protruding splinters or metal fasteners that might cut workers who are handling them. The molded handholds on plastic pallets also provide better lifting ergonomics by more evenly distributing weight. This can further help limit lifting injuries and improve pallet handling safety. Overall, plastic pallets offer clear handling advantages over wood pallets, which makes switching to plastic platforms a smart way to immediately improve warehouse safety.
- Implement ergonomic evaluations and training: What is lifted in the warehouse is often less important than how it’s lifted. Managers should review the daily tasks of their warehouse workers to see how lifting practices and the arrangement of items in the warehouse could be improved. In some cases, a warehouse’s workers’ compensation insurance carrier will even offer this as a complimentary service to reduce injury claims.
- Provide protective gear: Rubber-soled boots can help reduce the risk of trips and falls for employees in the warehouse by providing a better grip on the floor. If your warehouse uses wood pallets, puncture-resistant boots can help prevent loose nails from going through shoe soles. Meanwhile, disposable plastic gloves are great for covering existing cuts and splinters to protect them from contamination and prevent the contamination of products. Protective work gloves are a good way to prevent cuts and splinters from occurring in the first place.
Upgrading to plastic pallets, reviewing employee processes, and offering protective gear can all contribute to warehouse injury prevention.
While minor injuries like those described above may not be expensive, or even particularly disruptive, they happen almost every day in warehouse environments and can add up to major losses over time. Upgrading to plastic pallets, reviewing employee processes, and offering protective gear can all contribute to warehouse injury prevention and make a positive difference for workers while improving a facility’s productivity.
iGPS plastic rental pallets leverage unibody construction that completely eliminates fasteners and splinters that can cause injuries to workers and damage to products. Our lightweight pallets are excellent tools for supporting your warehouse injury prevention practices. To learn more, contact us at 1-800-884-0225, email a specialist at switch@igps.net, or visit our contact page.