Key Takeaways:
- Pipeline inventory is an essential component of the supply chain. The terms refers to goods that have been purchased and are now in transit between two points in the supply chain.
- When goods are ordered, they are transferred from a supplier to a retailer or distributor, with important metrics such as time-in-transit and lead time tracked en route.
- Supply chain managers calculate pipeline inventory by multiplying lead time by demand rate. This shows how much pipeline inventory is currently in transit at any given time.
- Decoupling inventory refers to safety stock that is not yet purchased by stored to safeguard an enterprise against supply chain disruptions, such as production challenges or a sudden increase in consumer demand.
- Challenges that can make pipeline inventory management difficult include issues with tracking and visibility, demand forecasting difficulties, and supply chain disruptions such as a pandemic or natural disaster.
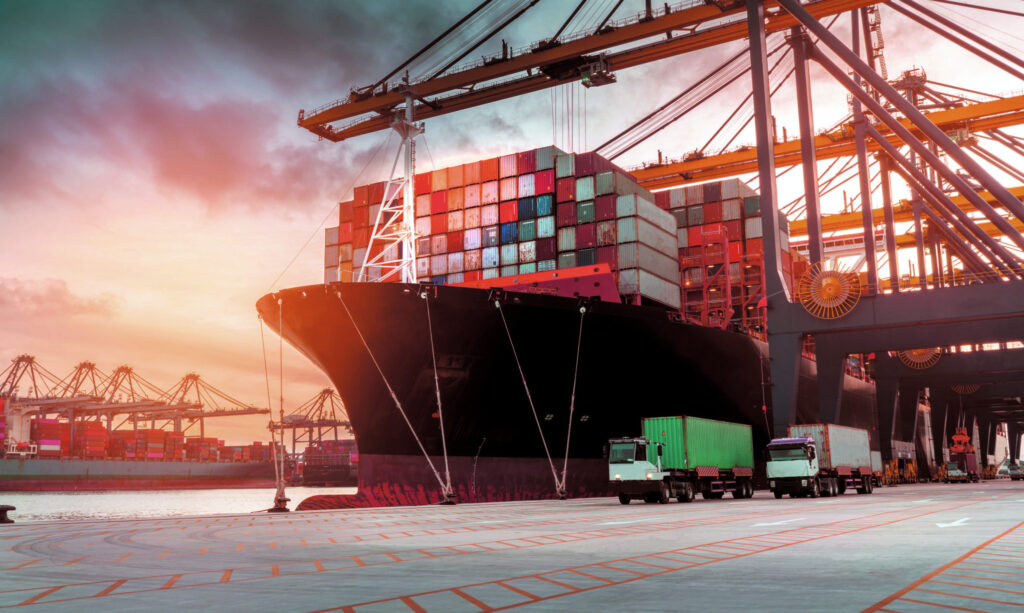
What is Pipeline Inventory?
Pipeline inventory is an essential component in the national and global supply chain — especially as supply chains grow increasingly complex. In contrast to stockpiles of goods that are in storage and haven’t yet been paid for, pipeline inventory refers to goods that have been purchased or committed for purchase and are now in transit between one point and another in the supply chain. Every day, countless tons of goods in the pipeline inventory are flowing between manufacturing facilities, warehouses and fulfillment centers, and retail stores.
How Pipeline Inventory Works
When an order is placed for a specific quantity of goods, a retailer or distributor places an order with a supplier, which either sources or manufactures the goods. They are then shipped from the supplier’s warehouse to the retailer’s own distribution center before ultimately being delivered to the store. Along the way, important metrics such as time-in-transit and overall lead time are tracked and real-time data is provided to the purchaser, creating improved supply chain visibility. It is important to remember that in contrast to other types of inventory, pipeline inventory refers to goods that are in transit or destined for transit, and have already been purchased. Key components of pipeline inventory include:
- In-transit inventory that is already physically moving between locations.
- Work-in-progress inventory, which is undergoing manufacture or assembly but represents an investment in goods that have already been ordered and purchased.
- Distribution inventory stored at a warehouse or distribution center; while it is technically not in transit yet, distribution inventory is considered part of the pipeline inventory because it is destined to be shipped.
Once goods are on the store shelves and ready for purchase by the consumer, they become cycle inventory — inventory that is no longer in transit and is now available for purchase while the store awaits replenishment.
Pipeline inventory management is an essential part of overall inventory management and planning, because it helps ensure customer satisfaction through the ready availability of goods; cash flow for suppliers and manufacturers as well as retailers; and improved demand forecasting and risk management.
Pipeline Inventory Calculation
Supply chain managers seeking to determine the current volume of the pipeline inventory follow a simple formula: Pipeline Inventory = Lead Time x Demand Rate.
The lead time is the time that it takes for products to be moved from the supplier to the end customer, whereas demand rate refers to the rate at which products are sold or consumed.
For example, if a retailer orders 1,000 units from a product per week, and it takes two weeks for the products to be delivered, then the formula is 2 weeks x 1,000 week, or 2,000 units. This means that at any given time, the retailer will have 2,000 units of product in transit, i.e., in the pipeline inventory. Of course, if there are multiple products in the mix with varying lead times and demand rates, then the pipeline inventory for each must be calculated separately, with the total pipeline inventory being the sum of the total. Changes in demand rate and variations in transportation modes can also impact outcomes.
The Importance of Decoupling Inventory
If the only products manufactured or assembled are ones that have already been purchased and spoken for, then organizations are not insulated against disruptions in the supply chain, which can include supplier shortages, delays in production, or unexpected increases in customer demand. This is why decoupling inventory, or “safety stock,” is also typically kept on hand. Decoupling inventory can improve lead times when demand goes up, while also preventing stockouts and lost sales. It also ensures that if a production issue arises, such as a materials shortage or natural disaster, inventory will still be available to be transitioned into the pipeline.
Pipeline Inventory Challenges
Pipeline inventory management is occasionally fraught with difficulties that can significantly impact bottom lines for manufacturers, suppliers, and retailers. Among the biggest challenges is visibility. While tracking technologies have improved, goods often travel across vast distances through intermodal networks, and any lack of real-time visibility can lead to uninformed decision-making.
Demand forecasting can also prove difficult, because in an era of economic uncertainty and continually fluctuating consumer behaviors, predicting future demand with precision is anything but simple. Inaccurate demand forecasting can result in either excess inventory, which ties up valuable capital in products that may not sell, or stockouts, leading both to unhappy customers and lost sales.
A third potential challenge is the constant threat of supply chain disruptions, which can be caused by transportation delays, geopolitical uncertainty, or natural disasters. The COVID-19 pandemic certainly posed significant headaches for supply chain managers, and in many areas of the supply chain its ramifications are still being felt. Such disruptions can result in a lack of availability of goods or materials, fluctuating lead times, and excess costs.
Balancing these variables is just another element of effective supply chain management. But when these challenges are managed and met successfully, it results in a steady supply of goods, regular cash flow for stakeholders, and smoother and more optimized supply chain overall.
Frequently Asked Questions
What is the difference between pipeline inventory and cycle inventory?
Pipeline inventory refers to goods that have been purchased and are in transit between different points in the supply chain, while cycle inventory is the stock at retail locations held to meet average consumer demand between orders.
What is the difference between pipeline inventory and decoupling inventory?
Pipeline inventory refers to goods that are in transit between different points in the supply chain. Decoupling inventory, on the other hand, is a type of safety stock held to buffer against potential disruptions in the supply chain. While pipeline inventory is about the movement of goods that have been purchased, decoupled inventory is stored “safety stock” designed to protect an enterprise against uncertainties.
What are the benefits of pipeline inventory management?
Pipeline inventory management benefits businesses by ensuring timely product delivery, improving supply chain visibility, optimizing cash flow, reducing stockouts, and enhancing demand forecasting accuracy.
Manufacturers embracing the future of work in the supply chain choose iGPS plastic pallets. iGPS pallets are lighter, more automation-friendly, and contribute to improved sustainability. For more information, contact us at 1-800-884-0225, email a specialist at switch@igps.net, or visit our contact page.