Proper forklift safety in the warehouse isn’t just about preventing employee injuries, though that is its primary goal. It’s also about protecting a company’s bottom line, as improper forklift use can result in both direct and indirect costs. Damaged products, reduced employee productivity, fines, penalties, and increased insurance costs are all consequences of failing to adhere to proper forklift safety protocols.
OSHA has a long list of requirements and compliance information related to the safe use of forklifts in the warehouse, but the most crucial is the certification and licensing of the operator. In obtaining these certifications, the operator learns the importance of responsible use as well as visibility and load stabilization. Warehouse managers can make it even easier for employees to adhere to forklift safety protocols by providing clear-cut company protocols on forklift use and offering tools like plastic pallets which make the warehouse safer overall.
The Cost of Neglecting Forklift Safety in the Warehouse
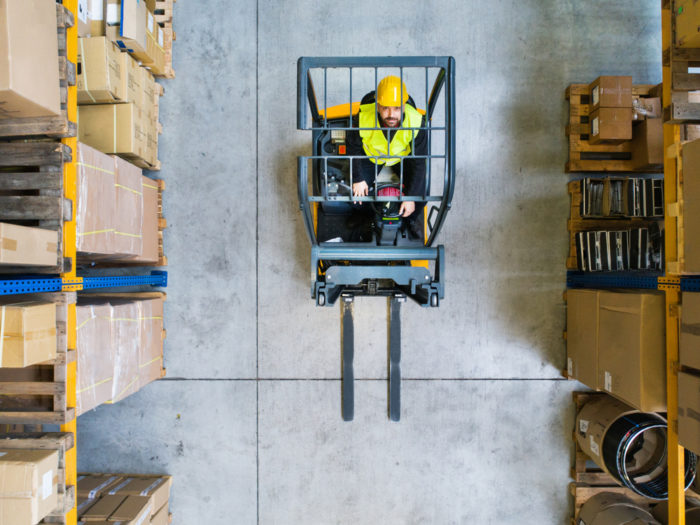
Improper use of forklifts in the warehouse can increase a company’s expenses while decreasing revenue, due to both direct costs and long-term consequences. Some examples of these direct and indirect costs include:
Direct Costs | Indirect Costs |
Employee injuries: From 2011 to 2017, forklift-related incidents resulted in 614 deaths overall and an average of 7000 injuries annually. The most common incident cause is operator error and improper use. | Employee morale: Workplace accidents lower morale among employees. At the same time, low morale is a contributor to workplace accidents. These two feed off each other and can create an ongoing cycle that hinders productivity. |
OSHA violations: An OSHA violation for unsafe forklift use can cost as much as $132,598 if the issue is deemed habitual. Even for a single violation, an OSHA fine could be as much as $13,260. | Insurance premiums: Insurers consider both incident and OSHA violation history when establishing premiums. A company that is shown to have a history of such violations will pay markedly higher premiums than one that’s violation-free. |
Damaged Products: Improper forklift use can result in damaged products and rejected loads. Products may be punctured or crushed if the pallet is improperly lifted, or the pallet may be dropped if the operator exceeds the maximum capacity. Even a few damaged products may result in the rejection of the entire load by the retailer or end-user. | Damaged reputation: While the occasional broken item is to be expected, ongoing issues with shipments cause damage to the reputation of the warehouse. Retailers and manufacturers may share their experiences with others in the industry, creating a poor reputation for that facility. |
Employees working on a deadline may feel rushed and overlook protocol in order to complete tasks quickly.
The human component is the biggest variable when it comes to forklift safety. Employees working on a deadline may feel rushed and overlook protocol in order to complete tasks quickly. While procedures and inspections can help prevent this, so can tools–like plastic pallets–that make it easier to adhere to protocols.
How Plastic Pallets Support Forklift Safety
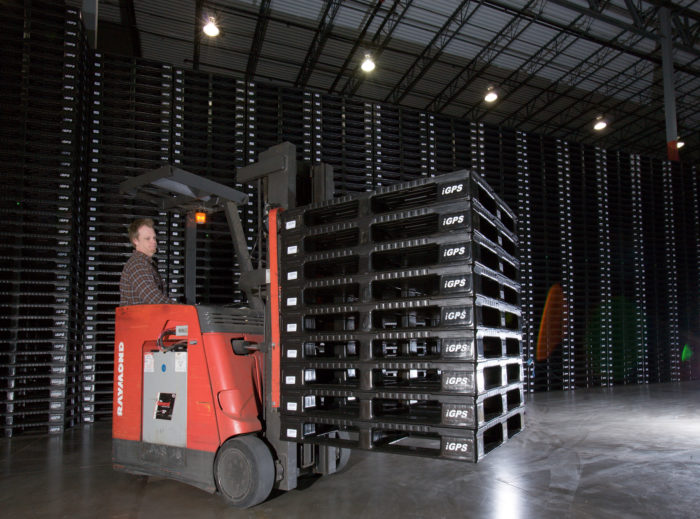
Forklift incidents occur for many reasons. A driver might collide with something due to limited visibility or room to maneuver, the vehicle might tip because of an unstable load, or the pallet holding the load itself might fail, spilling its contents. In any of these scenarios, injury and product damage is likely. However, plastic pallets can help guard against all these issues. This is because plastic pallets offer:
- Light, consistent weight: Plastic pallets typically weigh no more than 50 pounds, while the weight of a standard wood pallet can be up to 80 pounds. In addition, while the weight of wood pallets fluctuates significantly based on pallet type, moisture, manufacturer, and pallet age, plastic pallets stay consistent. A light, predictable weight makes it easier for the forklift operator to accurately gauge load weights and ensure the forklift is not overloaded.
- Strength and durability: Over time, wood pallets often lose hardware like screws as well as entire boards, which can result in the failure of the entire pallet. This causes spills, product damage, and potential contamination. Durable plastic pallets have a unibody construction that ensures no individual parts or hardware can come loose and be left behind.
- Thoughtful design: Wood pallets come in four- and two-way designs, meaning that in some cases, they will have to be approached from a specific angle when using the forklift. This can cause issues with maneuverability that lead to collisions. Plastic pallets are typically designed for four-way entry, so it’s safe to approach from any angle. High-quality plastic pallets also have chamfered edges and rounded fork notches that make it easy for forklift operators to enter the pallet without damaging it.
Easy-to-use tools like plastic pallets can greatly increase forklift safety.
Poor forklift safety in the warehouse negatively impacts a company’s bottom line in the short term and over time. While training staff on safety is the most important step your facility can take, providing durable, easy-to-use tools like plastic pallets can greatly increase forklift safety by making the process of moving loads easier and more predictable.
iGPS plastic pallet pooling supports forklift safety in the warehouse by renting sturdy, predictable platforms that minimize equipment wear and product damage. For information on our pallet rental options, contact us at 1-800-884-0225, email a specialist at switch@igps.net, or visit our contact page.