Cold chain management has transformed to meet the growing global demand for fresh food and pharmaceuticals. This transformation has not always been easy, though: businesses running cold chain logistics operations often struggle to transport and store perishable food products while maintaining their safety and freshness. Pharmaceutical products such as vaccines are particularly prone to damage arising from cold storage temperature fluctuations that can lead to expensive recalls. Product wastage and recalls that stem from cold chain management inefficiencies increase the total cost of business (TCOB) and negatively impact the bottom line. Consequently, operations managers are always looking for effective measures to address cold chain logistics challenges.
Key Challenges in Cold Chain Logistics and How to Address Them
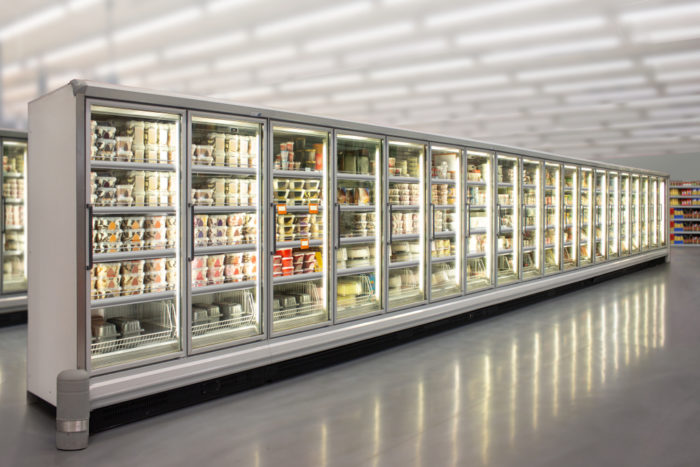
Businesses face cold chain logistics challenges at every step of the supply chain—procurement, storage, transport, and delivery to the end-consumer. Heat exposure due to poor insulation, moisture build-up inside the storage facility, and the resulting microbial growth on products are common issues that impact cold chain logistics. The follo1wing are the three most frequent cold chain logistics challenges that can be effectively addressed with technology and the right auxiliary equipment.
Temperature Control
Moisture and humidity are key factors that can cause significant damage to perishable products. Though employees in cold storage warehouses are trained to identify potential gaps in temperature control and maintain the right temperature around the clock, any lapses due to human error can damage an entire inventory. Inadequate cooler space for product load storage can also cause damage. By introducing automation to monitor cold storage temperature, warehouse managers can lower product damage incidents in cold chain logistics. An Automated Storage and Retrieval System (ASRS) can also create an additional cold chain capacity by improving cube utilization and pallet stacking.
Product Tracking
Most cold chain logistics challenges arise from a lack of supply chain visibility. Logistics managers are often clueless about real-time product location, temperature, and condition during transport and storage. Supply chain congestion and transportation delay can affect the safety and freshness of an entire load of time-sensitive biologics and perishable food products. Deploying Radio Frequency Identification (RFID), along with temperature sensors, scanning equipment, and supply chain management (SCM) software can effectively track product movement and condition across the supply chain.
Maintaining Hygiene
When it comes to warehouse storage of perishable products, there is always a possibility of cross-contamination and pest infestation. This can occur due to temperature increases, unsanitized surfaces, or through widely used wood block pallets.
Cross-contamination by pathogens and pests can be particularly detrimental for biologics and vaccines, as the contaminants can compromise the safety of pharmaceutical products. Logistics managers can help maintain hygiene in cold chain logistics by ensuring products are stored at the recommended temperature, scheduling regular cleaning and sanitization, and switching to food-safe, non-absorbent pallets.
While adopting ASRS or RFID tag technology to maintain temperature and track product loads can significantly improve the efficiency of cold chain logistics, switching to high-quality plastic pallets can further reduce the risks associated with wood pallets that can cause contamination in cold storage.
Using Plastic Pallets to Solve Cold Chain Logistics Challenges
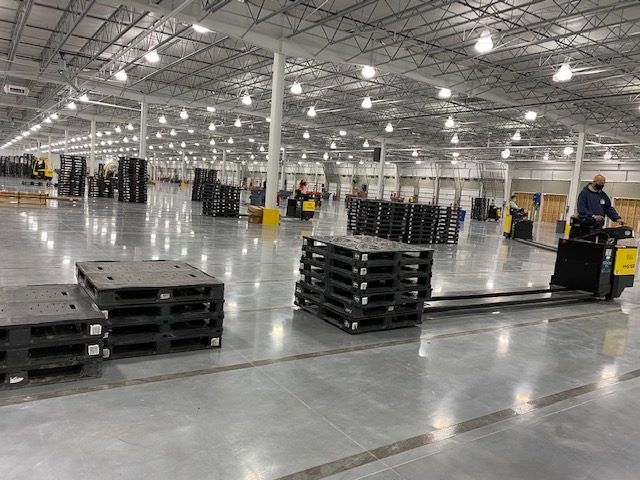
Strong and lightweight plastic pallets offer a cost-effective solution for product transportation and storage in cold chain logistics. The following features of plastic pallets are instrumental in addressing common cold chain logistics challenges:
- Unitized Construction: Since plastic pallets are devoid of any splinters, loose boards, or protruding nails, they significantly reduce the risk of product damage. The unitized construction of these pallets, leading to uniform weight and dimensions, also makes them more compatible with ASRS, with fewer incidents of equipment downtime due to platform failure.
- Increased Durability: Plastic pallets have an increased lifespan compared to wood block pallets and can make up to 100 trips across the supply chain. The increased durability of the pallets makes them an ideal fit for embedding RFID tags to track and trace product loads.
- Non-Absorbent Plastic Surface: Plastic pallets are impervious to moisture. Their non-absorbent plastic surface also resists the growth of bacteria and makes it easy to clean the surface after every use without the treatment of pesticides or fungicides. As a result, plastic shipping platforms offer improved hygiene for food products and bio-pharmaceuticals.
Cold chain logistics operations are complex and there is always a risk of damage and recall when handling such time-sensitive products. Yet, businesses can solve several cold chain logistics challenges and improve the efficiency of their operations by making a timely switch to plastic shipping platforms.
Non-absorbent iGPS pallets offer increased hygiene and carry embedded RFID tags to ensure track-and-trace visibility. To learn more about how our intelligent shipping platforms can address cold chain logistics challenges, give our team a call at 1-800-884-0225, email a specialist at switch@igps.net, or visit our contact page.