Key Takeaways:
- Warehouse automation has revolutionized the supply chain and enabled unprecedented speed and accuracy
- Among the major technologies enabling effective warehouse automation is automated storage and retrieval systems (ASRS), which are designed for the precise storage and retrieval of goods.
- Automated guided vehicles (AGVs), meanwhile, are robotic vehicles that transport goods and pallets through different sections of a facility.
- These systems are fundamentally different, though they are united in the goals of improving speed and efficiency, enhancing safety, reducing reliance on manual labor, and contributing to lower overall cost of business.
- The integration of lightweight, durable plastic pallets also improves the efficiency of these systems while reducing damage and downtime.
The advent of warehouse automation has revolutionized the modern supply chain, fueling unprecedented accuracy and speed in response to rising consumer demand. Among the many technological advancements paving the way for increased logistics efficiency are Automated Guided Vehicles (AGs) and Automated Storage and Retrieval Systems (ASRS). While both play an important role in an automated supply chain operation and can have overlapping features, they are suited to different operational needs — and understanding the distinction can help supply chain managers identify the right solution for their facility.
What Are Automated Storage and Retrieval Systems (AS/RS)?
An ASRS (or AS/RS) is a complex and automated solution designed for the quick and precise storage and retrieval of pallets and goods. These systems combine high-tech hardware, including cranes and shuttles, with sophisticated software tools. A standout feature of an ASRS is its ability to use vertical space effectively, often surpassing the capabilities of human operators and allowing the “real estate” of a warehouse to accommodate a large volume of goods within a smaller footprint. ASRS systems are fast and precise, both of which are critical in industries where timely order fulfillment is essential.
Types of Automated Storage and Retrieval Systems, which can be customized and scaled depending on the needs of an enterprise, include:
- Unit-Load Systems: Designed for moving and organizing large pallets.
- Mini-Load Systems: These systems are tailored to smaller items, like bins.
- Shuttle-Based Systems: These use sophisticated, rail-guided shuttles to move goods.
What Are Automated Guided Vehicles (AGVs)?
Although ASRS systems have many moving parts, the system itself is typically stationary. Automated Guided Vehicles (AGVs), on the other hand, are mobile robots that transport goods within warehouses, fulfillment centers, and manufacturing facilities. Working in conjunction with an ASRS, an AGV can provide mobility and flexibility across the full breadth of a warehouse operation. Employing guidance technologies such as lasers or magnetic strips, and equipped with various sensors to ensure safe operations, these vehicles can handle a range of tasks, including towing carts and transporting individual pallets. Their advantages are numerous:
- AGVs can be easily adapted to changes in facility layouts;
- They are scalable; as an enterprise’s needs grow, so can the fleet;
- They can be designed to handle diverse types of materials and platforms;
- They do not require human operators — and while they are not flawless, they are generally subject to fewer errors and safety issues.
AGVs also come with some disadvantages, such as potentially high up-front costs, limited decision-making capabilities, and regular maintenance requirements. But in a typical automated environment, especially in large-scale operations, they are an essential component in the mix.
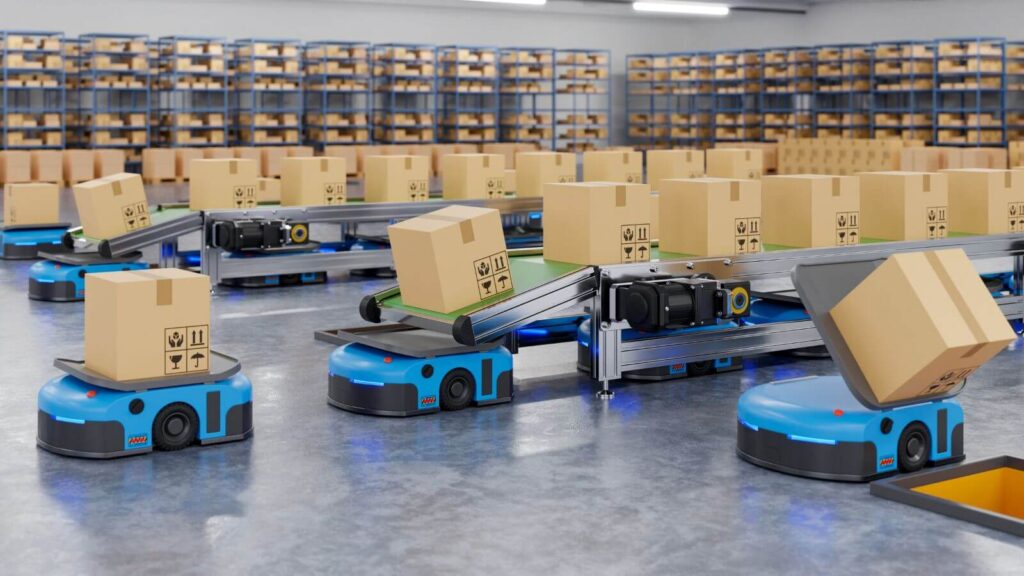
The Differences Between AGVs and AS/RS in Warehouse Automation
Both AGVs and ASRS systems are integral parts of an automated warehouse environment, and they both use sophisticated hardware and software to facilitate the efficient movement of goods within a facility. But they fundamentally differ in their design and application:
- An ASRS system is stationary and focuses on high-density storage and retrieval. Because AGVs are mobile, they are meant for transporting goods throughout different areas of a facility.
- AGVs require floor space for movement and navigation. An ASRS excels at high-volume storage and retrieval, maximizing vertical space.
- An ASRS requires significant infrastructure, including conveyors and racking systems. This means that as a facility’s layout changes, an existing ASRS may be less adaptable. AGVs can be easily reprogrammed to adapt to new layout changes.
- AGVs may face delays in navigating a crowded environment, whereas ASRS systems are designed to facilitate fast retrieval times without typically being impeded by obstacles.
The Similarities Between AS/RS and AGVs
As noted above, while AGVs and ASRS are fundamentally different, they share common ground and common goals in enabling an efficient automated environment — which is exactly why it is helpful to highlight their distinct uses. Their similarities are numerous:
- Both systems automate repetitive tasks, reduce the need for manual labor, and are ultimately designed to enhance efficiency and accuracy in warehouse operations.
- Both integrate seamlessly with advanced warehouse management systems (WMS), which facilitate real-time tracking and inventory management.
- Both use sophisticated sensors and software to ensure accurate storage, retrieval, and transportation of goods while keeping the environment as safe as possible for human workers.
- On the topic of safety, both systems contribute to a decrease in workplace injuries by automating tasks like heavy lifting and navigating hazardous spaces.
- And because they improve productivity and reduce errors, both systems provide long-term operational safety as part of an automated environment.
Together, AGVs and ASRS systems help enterprises scale their operations and plan future business growth as needs evolve and grow. And when plastic pallets enter the mix — such as durable, lightweight plastic pallets distributed by iGPS — the benefits of these systems are truly able to shine.
Plastic pallets are lighter than traditional wood pallets, which lowers wear-and-tear on automated systems while increasing the speed and agility of handling processes. The absence of nails and splinters, meanwhile, minimizes the risk of equipment jams and malfunctions, reducing maintenance costs and maximizing uptime.
When an ASRS system receives an iGPS pallet, its embedded RFID chips can be scanned to verify the identity and proper location of the goods, ensuring accurate placement in high-density storage. AGVs can scan these same RFID chips to confirm that they are handling the correct goods and bringing them to the appropriate destinations.
What is Warehouse Automation?
Warehouse automation involves the use of automated technology to streamline and accelerate warehouse and logistics processes, from storage and retrieval to transportation and inventory management. It involves a combination of automated systems like AGVs and ASRS systems, driven by sophisticated software solutions such as warehouse management systems (WMS) and enterprise resource planning (ERP) tools. When working in tandem, these systems reduce bottlenecks, minimize errors, limit workplace injuries, and accelerate swift and accurate order fulfillment.
By understanding the roles and applications of warehouse automation systems — including AGVs and ASRS systems, and their ability to integrate with advanced shipping platforms like iGPS pallets — supply chain managers can make informed decisions about how to optimize their business operations and remain competitive in an increasingly fast-paced and automated world.
Frequently Asked Questions
What are some key differences between AGVs and ASRS systems?
AGVs are mobile robots designed to transport goods within a warehouse, while ASRS systems are stationary and focus on storing and retrieving items in high-density storage areas. AGVs offer flexibility and adaptability to changing layouts, whereas ASRS systems excel in precise, high-volume storage and retrieval tasks.
What are similarities between AGVs and ASRS systems?
Both AGVs and ASRS systems aim to improve warehouse efficiency by automating manual tasks, reducing errors, and enhancing productivity. They integrate with warehouse management systems (WMS), use advanced sensors for precision, and support scalability to accommodate growing operational needs.
How do AGVs and ASRS systems work together to improve warehouse automation?
AGVs transport items to and from ASRS systems, creating a seamless workflow where ASRS handles efficient storage and retrieval while AGVs manage material movement across the facility. This collaboration reduces bottlenecks, optimizes space utilization, and accelerates order fulfillment processes.
Manufacturers striving to implement effective warehouse automation technologies choose durable iGPS plastic pallets for their shipping needs. iGPS pallets are lighter, more automation-friendly, and help lower greenhouse emissions. For more information, contact us at 1-800-884-0225, email a specialist at switch@igps.net, or visit our contact page.