Cold storage presents many challenges for businesses. Cold temperatures affect employees, increase depreciation on equipment, and necessitate more frequent maintenance on machinery. Still, cold temperatures must be carefully maintained to guarantee that temperature-sensitive goods inside facilities remain safe to use. This is crucial for products that include food and lifesaving pharmaceuticals, which can lose potency or become unsafe at warmer temperatures.
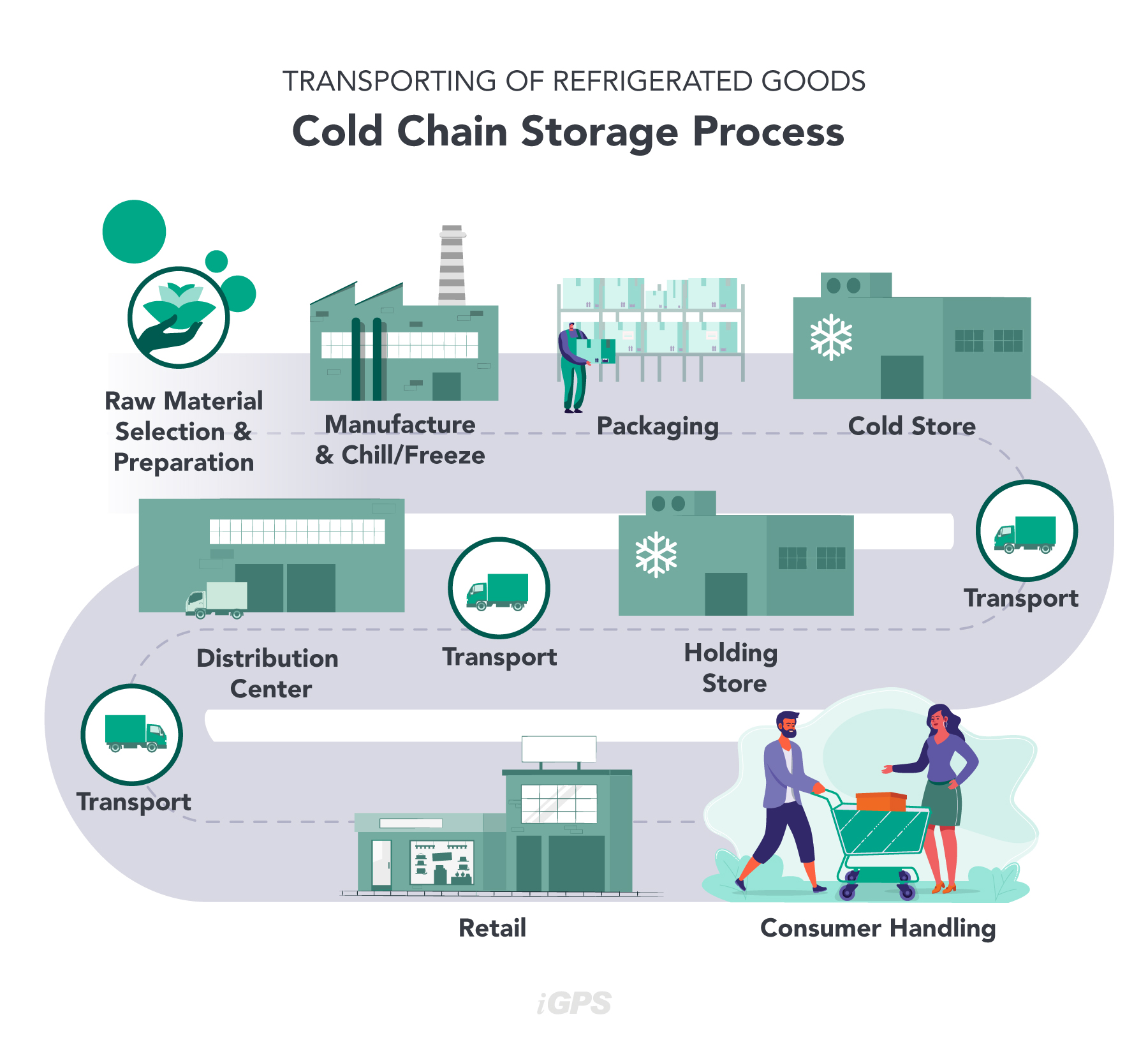
In 2020, the consumer demand for frozen foods significantly increased and has continued to grow since the onset of the pandemic due to the proliferation of online grocery options, safety concerns, and consumer demands for increased convenience. In fact, according to the American Frozen Food Institute (AFFI), 30 percent of consumers increased their home freezer capacity in 2020 and spent an additional $595 per person on frozen foods in 2021. A November 2022 study on the global cold storage warehouses market predicted that the industry was set to grow significantly by 2028, which will generate new opportunities for suppliers of temperature-sensitive goods.
Frozen products are set to play a larger role in the future of the supply chain as well as the retail market. Key best practices for warehouse cold storage can help to ensure that products are fit for use, equipment is in working condition, and employees remain healthy.
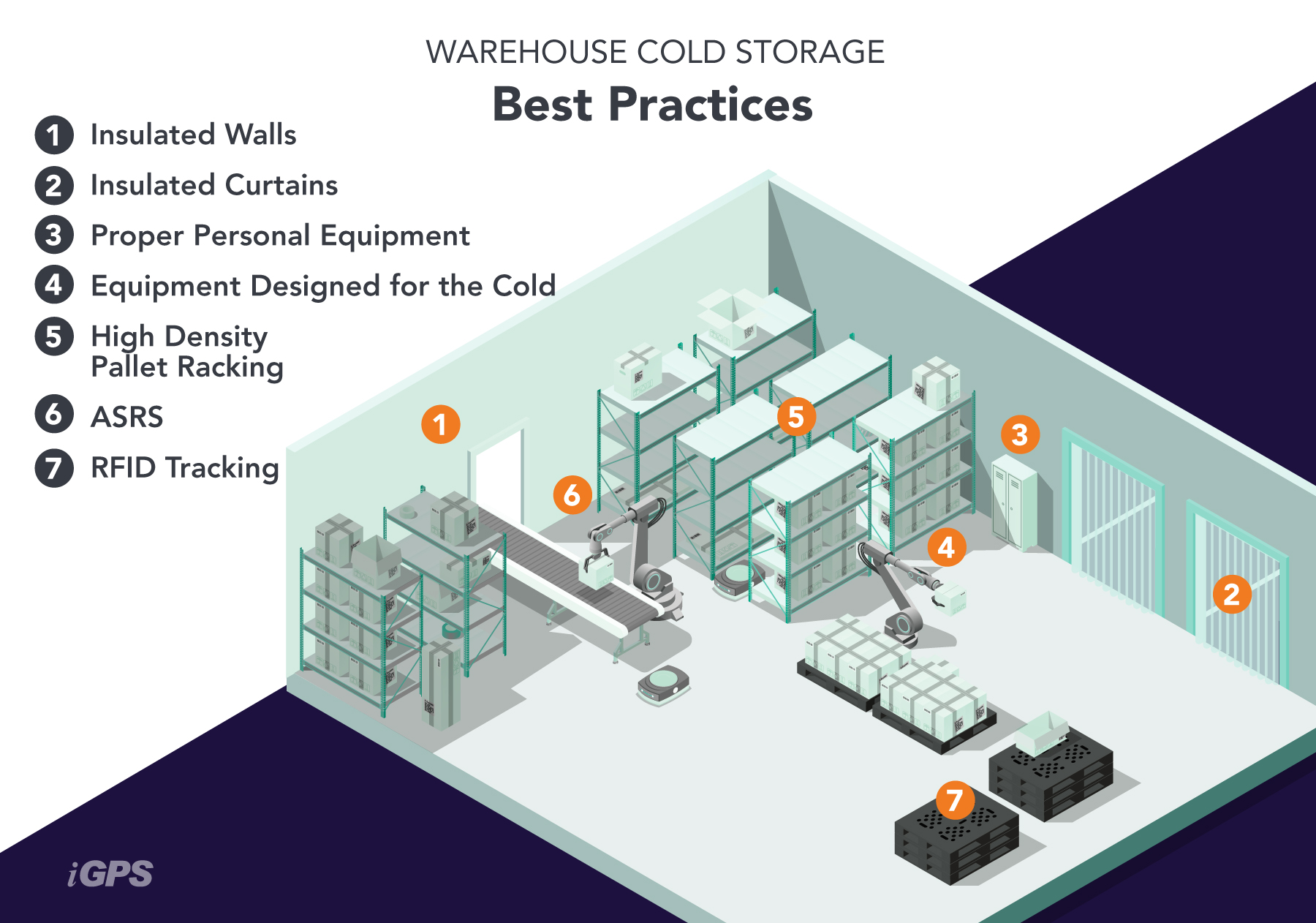
- Control Heat Exchange: The most fundamental best practice in a cold storage warehouse is temperature control. Each portion of the warehouse must remain within its set range to function properly. For example, refrigerated products must be refrigerated and frozen products must remain frozen. This means that the flow of heat must be meticulously controlled within the space. In homes and offices, this can be done easily with walls and insulation. But in a warehouse environment, with products coming in and out and routinely reconfigured, this becomes more complicated. Despite this flux, though, vegetables still need to be stored at 55 degrees F, dairy products at 34 degrees F, and ice cream at -10 degrees F.With insulated curtain walls, businesses can control temperatures anywhere from 15 degrees F to 40 degrees F of temperature separation depending on the thickness of their insulation. These plastic modular curtains can be deployed and redeployed as needed to separate warehouses into different zones.
- Provide Employees With the Proper Personal Equipment: It is essential for employers to make sure that their workers have the equipment needed to perform their jobs efficiently. With appropriate gear such as insulated pants, gloves, and other personal equipment, employees will spend less time lingering in warmer areas or opening doors to escape the cold. Open doors can affect the efficiency of pick-and-pack operations and violate temperature protocols. Providing appropriate gear can have broad positive effects and helps to ensure that temperatures stay consistent throughout the entire warehouse.
- Use Equipment Designed for the Cold: The equipment typically found in a warehouse needs to have certain modifications for cold storage. Workers with heavy gear may find it hard to use a touchscreen, so equipment needs to be designed with buttons that are large enough to be felt through gloves. Electrical equipment must be sealed from condensation to avoid short circuits. High-voltage batteries must be used, since their exposure to cold can result in a 40 to 50 percent degradation.
- Practice Cold-Storage Forklift Safety: When forklifts move from warmer zones to freezers, condensation can form. Operators should always assume that forklift tines are slippery, which can cause pallets to slide. Moving and turning at safe speeds not only minimizes the chance of injury, but can also prevent a costly mess.
- Employ Automation Wherever Possible: Cold storage is more expensive than other types of warehouse space due to the costs associated with temperature maintenance. In conjunction with deep lane storage systems, automation can make the most of the cold storage space available by improving cube utilization. High-density pallet racking systems with pallet shuttles and Automated Storage and Retrieval Systems (ASRS) increase throughput and make optimal use of vertical space.The use of automated palletizers and depalletizers along with Autonomous Guided Vehicles (AGVs) for shuttling products through the warehouse make it possible for cold storage areas of the warehouse to operate with very few employees. Autonomous machinery moves seamlessly between temperature zones without hesitation and can log actions automatically with a centralized system. An automated system can reduce cooling costs and guarantee that products are kept at safe temperature levels.
- Maintain Accurate, Up-to-Date Records: To maintain the utmost level of safety, businesses must not only keep products cold, but also log an accurate record of their temperature. Temperature sensors can automatically track temperature, trigger alarms, and make note of potential lapses. This technology can be integrated with Radio Frequency Identification (RFID) tracking, which eliminates the need to scan every carton and SKU. Once cartons and pallet numbers are associated in the database, only the pallet needs to be scanned. This information can be made transparent throughout every level of the supply chain.Maintaining precise temperature records for all products in a warehouse keeps the public safe and helps businesses with their bottom line by avoiding issues that include costly recalls and product waste. Utilizing technology to ensure records are accurate may be the most important practice for any cold storage warehouse.
Optimizing Cold Storage Warehouse Best Practices
Implementing small changes in procedure and equipment can add up to big savings and greater profits in the future. Enacting a cold chain best practice can pay off in a big way down the line, as the demand for cold storage is predicted to increase. One way to elevate your cold storage best practices even further is by introducing plastic pallets from iGPS.
Plastic pallets have several distinct advantages over traditional wood pallets when it comes to cold storage, for a variety of reasons:
- Structural Integrity: Plastic pallets do not change shape when moved throughout different temperature zones. This means that their structural integrity isn’t dramatically affected by sudden shifts in temperature.
- Nonporous: Plastic pallets are non-absorbent, so condensation from temperature changes won’t encourage mold, mildew, and bacterial growth.
- Automation-Friendly: Plastic shipping pallets can also be equipped with RFID tracking to make record-keeping and tracking easier. Given the sensitivity of products in cold storage, the accurate record-keeping enabled by RFID chips is a great advantage. Furthermore, plastic pallets’ uniform dimensions make them more compatible with automated machinery.
Replacing an inventory of wood shipping pallets with plastic ones can be a challenge, but renting from a pallet pool significantly simplifies the transition. Pooled plastic pallets improve the efficiency of cold storage warehouse best practices while saving on pallet management costs.
Companies committed to optimizing their cold storage techniques use plastic pallets from iGPS, which are lightweight, recyclable, and help streamline your supply chain. For more information, contact us at 1-800-884-0225, email switch@igps.net, or visit our contact page. We also invite you to follow us on LinkedIn.
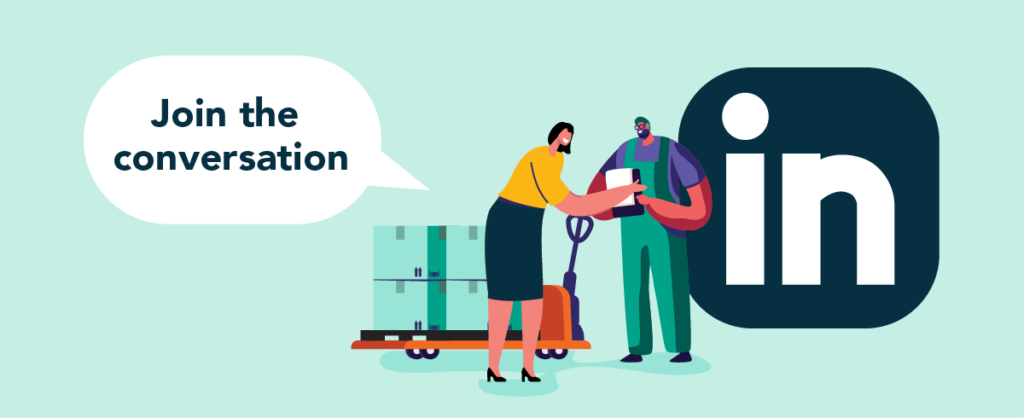