Product losses during transit are so common and seemingly inevitable that retail managers generally assume that some products will be damaged during transportation. Part of management training for most grocery and consumer goods retailers involves learning how to properly record, sort, and store products that arrived damaged so the retailer can get replacements or credit toward their next order. Given the range of industries that are affected by product damage, the costs are incalculable. It is safe to say, however, that reducing product damage during transportation can save substantial amounts of money over time.
One of the most vital elements in ensuring that products arrive at their destination undamaged is pallet load stability. Poorly stacked or loosely wrapped loads on a pallet can shift during handling and cause crushing damage to products. When products on the pallet move, they may also cause the weight distribution of a pallet to shift to one side, which can put strain on the forklift or even cause the entire load to topple over. Moreover, unstable pallet loads don’t just damage products and cause wear and tear on equipment, they are also a safety hazard to warehouse employees. In this article, we’ll discuss some ways to increase pallet load stability in order to ultimately lower your company’s Total Cost of Business (TCOB).
Packing and Stacking for Pallet Load Stability
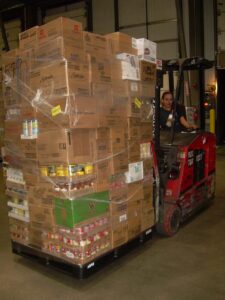
One common way that pallet load stability is compromised is through improper palletizing, or stacking products on the pallet in a way that renders the load unstable. Keeping a few basic considerations in mind can help maximize pallet load stability.
- Pallet Weight Limits: Pallet load stability will be compromised if the weight of the load exceeds the weight limit of the pallet. The upper limit on a pallet load depends on the type of pallet used and the dynamic (in motion) load capacity. Wood stringer pallets have a maximum dynamic load capacity of about 2,500 pounds, wood block pallets are slightly more robust at 2,800 pounds, and some types of plastic pallets have a whopping 5,000-pound dynamic pallet load capacity.
- Weight Distribution: How the weight of the products on a pallet is distributed also makes a difference in pallet load stability. The closer the weight is to the pallet itself, the lower the center of gravity and the more stable the load and pallet will be overall. Top-heavy loads can tumble off pallets and unbalanced loads can break pallet boards. Pallet load stability requires heavier products to be evenly distributed close to the pallet deck.
- Pallet Utilization: Standard GMA pallet dimensions are 40×48 inches. Products loaded onto a pallet should utilize as much of that space as possible without product overhang at the edges. Unused space on the pallet allows products to shift when the pallet is moved, causing instability.
- Stack Height: The maximum safe height that products can be stacked on a pallet isn’t related to the weight that it can hold. Instead, the determinant is generally the forklift operator’s ability to see over or around the pallet while driving. A safe height for a pallet stack handled by a standard forklift in most warehouses is about 60 inches, or five feet. Durable plastic pallets can technically be stacked higher, but this isn’t recommended unless equipment is available that is capable of handling a greater height.
- Pallet Wrapping: Once a pallet is loaded, the cartons will have to be bound tightly to each other and to the pallet. The usual means of accomplishing this is plastic pallet wrap. This can be done mechanically as part of an automated palletization process or manually. Wrapping should take place from the bottom to the top of the stack in order to bind the load together first. Once the stack of products is wrapped, it should then be bound to the pallet with wrap.
An interlocking product load pattern has a greater ability to resist lateral motion and keep loads from shifting.
The pattern used when stacking cartons onto a pallet matters a great deal for pallet load stability. An interlocked pattern involves alternating the way cartons are stacked so that each layer is offset, which creates a pattern resembling bricks in a wall. Columnar stacking, on the other hand, produces stacks in which cartons sit directly on top of each other in straight columns from the pallet deck to the top of the stack. There is disagreement over which pattern is better, but the truth is that both techniques can enhance pallet load stability. Which pattern should be used depends on how the pallets will be stored.
If the loaded pallets will be stacked directly on top of each other without the use of racking, a columnar pattern should be used as it provides greater compressive strength. If the loaded pallets are not stacked on top of each other, however, then an interlocking pattern is preferable as it has a greater ability to resist lateral motion and keep loads from shifting.
Choosing a Pallet That Stabilizes Loads
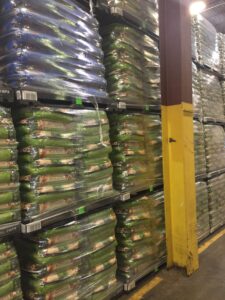
The type of pallet used can make a huge difference in pallet load stability. There will always be pallet loads that are less than perfect; mixed-case orders with different product types, for instance, won’t have a perfectly even weight distribution and load footprint. Moreover, fulfilling any order often results in at least one pallet that has fewer cartons than the others and it isn’t always possible to load these short pallets evenly. The result of these situations is that weight is unevenly distributed across the pallet. When the pallet moves, these forces are magnified. If most of the weight of a load ends up focused on a single area, the board or stringer on a wood pallet may break, significantly degrading pallet load stability. Plastic pallets do not share this disadvantage.
Using plastic pallets provides unmatched durability and boosts pallet load stability.
A plastic pallet is molded into a unitized construction, which gives it a high maximum dynamic load tolerance, and, generally, its top deck provides a greater surface than wood pallets. This also makes plastic pallets much more durable and robust than typical wood stringer or block pallets. Using plastic pallets provides unmatched durability and boosts pallet load stability to lower the costs of daily logistics operations.
The iGPS plastic pallet provides a durable, long-lasting shipping platform for your company’s products. iGPS rental pallets enhance pallet load stability and reduce product damage in transportation to expedite order fulfillment. To make the switch, give our team a call at 1-800-884-0225, email a specialist at switch@igps.net, or visit our contact page.