ARTICLE UPDATED DECEMBER 20, 2023
Pallets are an essential component of virtually every warehouse delivery, making it a rarity to find a shipment that doesn’t utilize them. Even less common is the sight of goods leaving a facility without being securely palletized. The consistent flow of pallets, from intake to throughput, is a universal presence in the world of supply chains. At every stage of this journey, a thorough pallet inspection process is imperative to ensure that incoming pallets are strong enough for facility use and reliable enough to transport products to their final destinations without mishaps.
The responsibility of assessing the condition of a pallet falls upon the facility that takes custody of it. A flawed pallet inspection procedure can lead to product losses during transit and the rejection of deliveries upon reaching retailers. Therefore, it is of utmost importance to establish comprehensive inspection protocols and repair methods to guarantee that all pallets employed and dispatched by your business meet the required standards. These inspection procedures should be consistently applied, regardless of the pallet’s type or size. There are key elements that any pallet inspection procedure should encompass, ultimately ensuring the safety of employees, products, and equipment.
Basic Pallet Inspection Procedure Guidelines
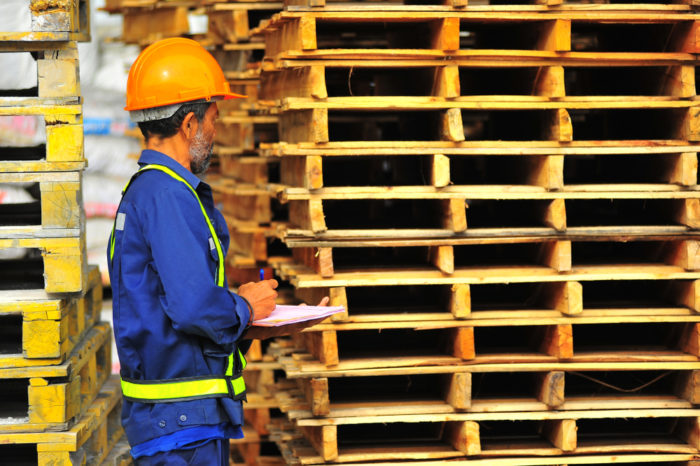
The International Organization for Standardization (ISO) provides criteria for pallet inspection procedures in ISO 18613:2014, which mainly cover pallet requirements for export and are aimed at preventing the spread of invasive species by ensuring compliance with the International Standard for Phytosanitary Measures (ISPM), specifically ISPM-15. Domestically, there is no organizational body that regulates inspection criteria for pallets. As a result, businesses must create their inspection processes and standards.
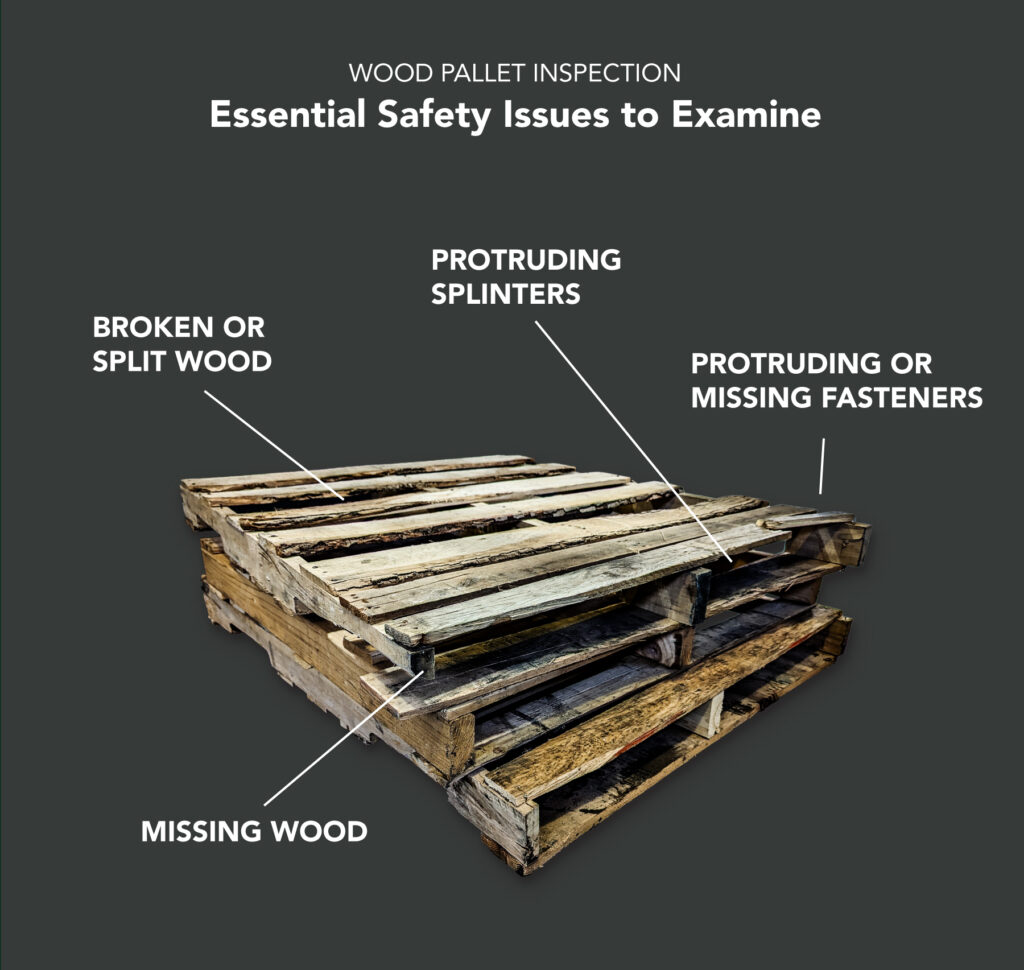
Any inspection process for wood pallets shipped domestically should primarily be concerned with determining whether the pallets are structurally sound and safe to handle and are not contaminated. These criteria should be the same whether the pallets are stringer or block pallets. Secondary inspection criteria should ensure that the pallet and its components won’t shed wood splinters and debris or lose fasteners. These are safety issues, as splinters and screws can puncture product packaging and cause product loss, harm employees, and damage equipment in the facility. At a minimum, a pallet inspection procedure should look for a few basic things:
- Broken Wood: Pallet boards that are broken all the way through are grounds for a pallet to be found unsuitable for use. A pallet should fail inspection if it is broken across the grain all the way through the board so that it separates a section of board from an anchor point where fasteners connect it to another board.
- Split Wood: Wood sometimes splits along the grain, but this doesn’t necessarily mean that the pallet is unusable. However, splits that exceed half the length, width, or height of the board or block, or splits of any length in stringer notches, indicate that the pallet should be pulled from service.
- Missing Wood: Pieces of board that are absent and expose a connection point or the shank of a fastener make a pallet unsuitable for use as-is.
- Protruding Splinters: Large splinters that protrude from any surface that encounters products or is handled by employees should be removed. If the splinter’s removal exposes connection points or fastener shanks, the pallet is no longer fit for service.
- Missing Fasteners: A specific number of fasteners are used on each pallet joint. The absence of one fastener means that the pallet no longer conforms to the structural standards to which it was built. Any missing fasteners will need to be replaced before the pallet can be returned to service
- Protruding Fasteners: Fasteners extending from boards pose the same safety hazard that protruding splinters do, and they also represent an unacceptable compromise of a pallet’s structural strength. They should be pulled and replaced before a wood pallet is reused.
A wood pallet that doesn’t pass an inspection doesn’t necessarily have to be discarded. Fasteners can be replaced, splits can be reinforced with additional wood or specially designed steel plates, and broken boards can be removed entirely and replaced. Unfortunately, for facilities taking delivery of potentially hundreds of pallets per hour, sorting out unsuitable wood pallets is time-consuming enough to be problematic. Hiring workers to repair and refurbish unsuitable pallets and designating an area for them to work in is an expense of time, money, and space that most logistics facilities cannot easily afford. The need to streamline or eliminate this process is part of the reason that plastic pallets have been gaining an increasing percentage of the pallet market.
Streamlining Pallet Management With Plastic Pallets
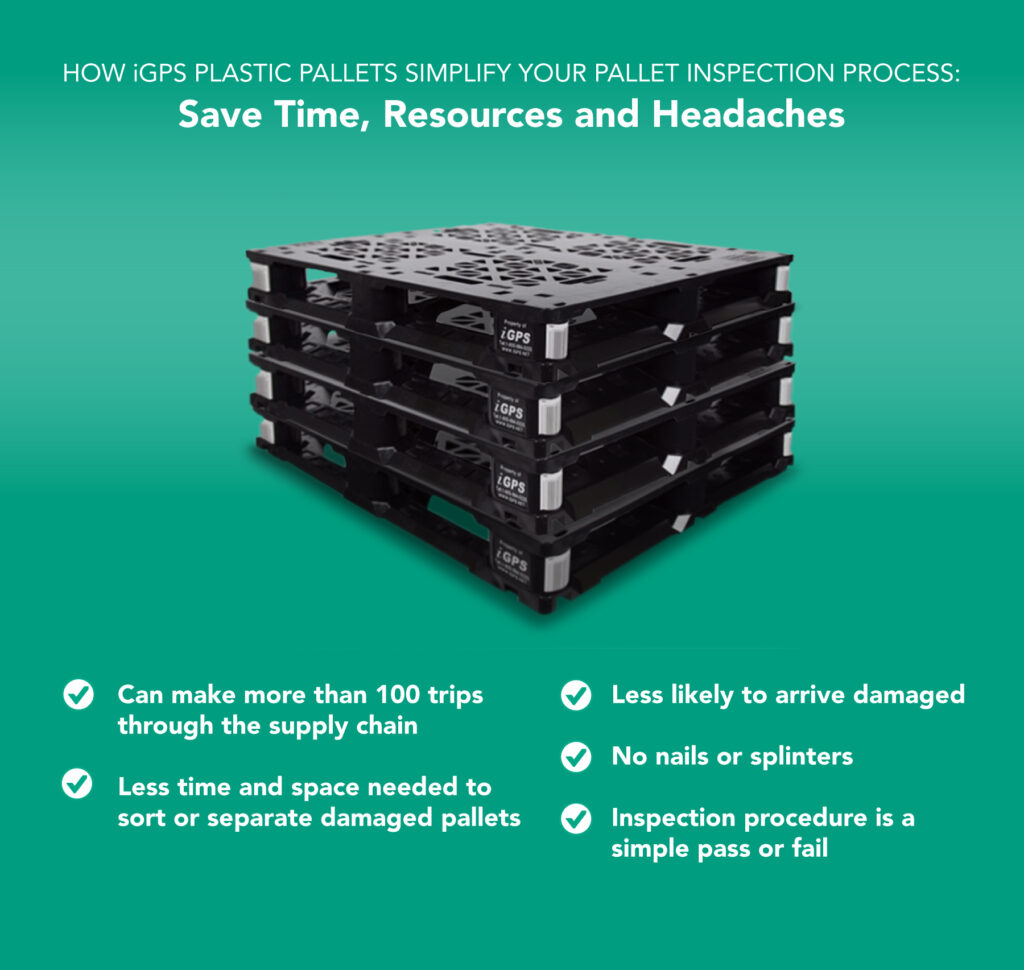
Plastic pallets have a big advantage in durability over either wood stringer or block pallets. High-quality plastic pallets can make more than 100 trips through the supply chain in their lifetime and are significantly less likely than wood pallets to arrive at a warehouse or distribution center damaged. As a result, far fewer plastic pallets need to be sorted and separated from arriving pallets for repair, saving facilities space that would otherwise be needed to group and store damaged wood pallets.
The pallet inspection procedure for plastic pallets is also a far simpler process than that of wood pallets. Since plastic pallets have a unitized construction, they don’t use nails or screws that can protrude or become lost in the facility where they might harm workers, products, or equipment. Plastic pallets are not prone to splinters, which does away with another source of damage or injury in the facility and lowers the risk of product damage during transportation. The integrated construction of plastic pallets also means that they have multiple redundant connection points. For all of these reasons, the pallet inspection procedure for plastic pallets is a simple pass or fail inspection that takes into consideration the overall condition of the pallet rather than examining many individual points of failure.
Altogether, plastic pallets enable a simpler, more streamlined pallet inspection procedure that saves time and space and ensures that more pallets are fit for reuse when they arrive. Plastic pallet pooling takes this one step further by making plastic pallet repair and retrieval the responsibility of your pallet pooling provider, saving you time, space, and money that will ultimately reduce your Total Cost of Business (TCOB).
The large role pallets play in the supply chain is undeniable. Proper pallet inspection is essential for ensuring the safety of workers, protecting products, and maintaining operational efficiency. By implementing a thorough inspection process and adhering to best practices, organizations can enjoy the benefits of a secure and sustainable supply chain while maximizing cost savings.
iGPS rents durable, lightweight GMA-spec plastic pallets with a unitized construction designed to streamline your pallet inspection procedure. To talk about what our pallets can do for your supply chain, contact us at 1-800-884-0225, email a specialist at switch@igps.net, or visit our contact page.