Ecommerce has driven massive growth in the sizes of warehouses. In fact, the footprint of the average warehouse has doubled in size since 2002. Yet even as more products are shipped and the shipping process becomes more complicated, it’s not practical for warehouses to keep getting bigger. In many cases, warehouse operations need to be convenient to major metropolitan areas where land isn’t available or is cost-prohibitive. Since warehouses can’t keep getting bigger, warehouse space management must get smarter.
Strategies for optimizing warehouse capacity generally involve repurposing space that’s not efficiently used by taking advantage of technology and third-party services. Options like ASRS, pallet pooling, and decentralized warehouse locations all offer ways to make the most of storage space and minimize your total cost of business (TCOB).
Three Ways to Enhance Warehouse Space Management
Reducing inventory held is the most obvious way to maximize warehouse storage space, but it’s not always practical as it can adversely impact revenue. To maintain maximum inventory without impacting productivity or overfilling the facility, supply chain managers should consider the following options:
- Create more compact storage using an ASRS: Automated Storage and Retrieval Systems (ASRS) allow warehouse managers to make the most of their space by reducing the amount of floor space needed to place and retrieve pallets. These systems work via a mechanical vertical crane, which allows for much more densely packed storage.
- Consider a decentralized warehouse model: Building more warehouses rather than adding to an existing facility may seem counterintuitive, but this can be an excellent strategy when dealing with limited access to available land. Owning or renting several smaller warehouses is often much more practical than owning a single large one. Having several facilities can also save on transportation costs, as the smaller warehouses can be strategically placed to take advantage of shipping routes. It’s not necessary that every facility be a warehouse in order to make use of this strategy. Managers can also open up smaller off-site storage spaces to hold equipment needed during peak demand, such as extra pallets, forklifts, automated guided vehicles (AGVs), and other items.
- Make the most of vertical space: The ceiling heights of large warehouses typically start at 32 feet but can be more than 40 feet in some cases. Making the most of this vertical space is crucial. Simple changes such as using easily stackable plastic pallets can open up more space on the warehouse floor. In particularly high warehouses, mezzanines can add an additional floor or two, significantly expanding storage and production space.
- Switch to pallet pooling: Pallet pooling offers a great opportunity to take back some space on the warehouse floor while also eliminating the need for overflow storage. Since it’s necessary to have a supply of extra pallets on hand for periods of peak demand, owning and storing an internal supply of platforms requires setting aside significant warehouse floor space for sorting and storing idle pallets. Participation in a pallet rental program allows warehouse managers to increase or decrease the number of platforms coming into the facility according to need.
Pallet pooling offers a great opportunity to take back some space on the warehouse floor while also eliminating the need for overflow storage.
In many cases, the above strategies do more than just improve space utilization in the warehouse. They can also reduce labor costs, as in the case of ASRS. They can reduce transportation costs, as in the use of decentralized warehouse locations. They can even increase worker safety, in the case of a switch to lighter, stackable plastic pallets.
Using Plastic Pallet Pooling to Reclaim Warehouse Space 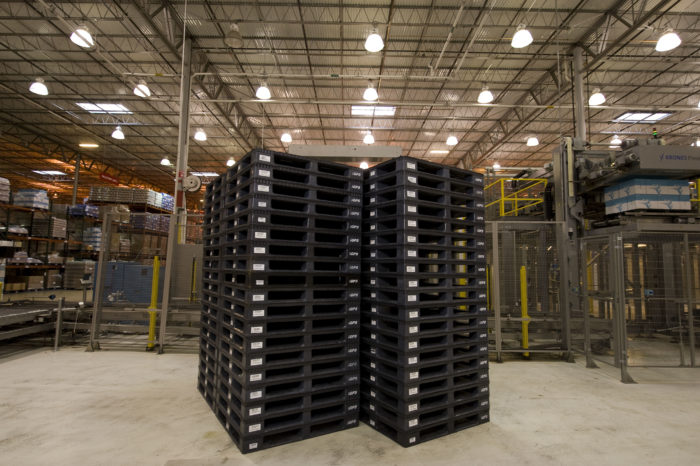
Pallet pooling allows companies to rent their pallets as and when needed, rather than owning them–but not all options are equal. Wood pallets are the most common type of pooled pallets, but they are not ideal for optimizing warehouse space management. Wood pallets tend to create unstable stacks and are prone to breakage, meaning that significant space must be set aside to store broken pallets until they can be sent out for repair. For warehouses looking to make the most of limited space, plastic is a far more practical option.
Plastic pallets can be stacked very high without risking the stability of the pile, saving space on the warehouse floor.
Since plastic pallets have consistent dimensions and weight that don’t change with age or exposure to moisture, they can be stacked very high without risking the stability of the pile, saving space on the warehouse floor. Finally, plastic pallets are easy to clean and less prone to damage than wood pallets, so that much less space is required for sorting and storing pallets prior to returning.
Plastic pallet pooling is a smart solution to warehouse space management as it gives managers easy access to extra pallets without the need to store an internal supply onsite. Plastic pallets are ideal for use with space-saving ASRS and high-density storage systems due to their uniform weight and dimensions. Any manager looking for a fast, simple way to reduce wasted warehouse space and maximize their TCOB should consider the benefits of plastic pallet pooling.
iGPS plastic pallet rental allows you to easily adjust your pallet supply as seasonal demand changes to free up valuable warehouse real estate. For more information, contact us at 1-800-884-0225, email a specialist at switch@igps.net, or visit our contact page.