In the intricate world of pharmaceuticals, logistics hums in the background as a silent hero. Yet, this behind-the-scenes player deserves center stage for countless medications to reach patients safely and on time. As industry practices evolve to include increased automation, logistics becomes the orchestrator of efficiency, ensuring a seamless and timely delivery of critical medications to those in need.
Pharmaceutical warehouses aren’t just storage hubs; they’re lifelines. The U.S. pharmaceutical warehousing market is projected to grow to $89.3 billion by 2032, with the increasing demand for temperature-controlled storage leading that growth.
Embracing innovative storage solutions and data-powered optimization is a critical step toward ensuring a seamless and efficient journey for every pill and vial. According to the “North America Pallet Market Report and Forecast 2022-2027” report, food and pharma giants are driving the market for plastic pallets, drawn in by their superior resistance to insects, fungi, and other pathogens.
The sterile pharmaceuticals market is projected to grow by over 50 percent in the next seven years, in part due to the COVID-19 pandemic, according to McKinsey. To seize additional market share, sterile manufacturers must rapidly increase their production capacity.
Outdated pharmaceutical facilities may seem like a distant problem, but they directly and indirectly affect us. Every lost product and delayed shipment can lead to treatments stalled and lives possibly endangered.
Planning an Efficient Pharmaceutical Warehouse Layout
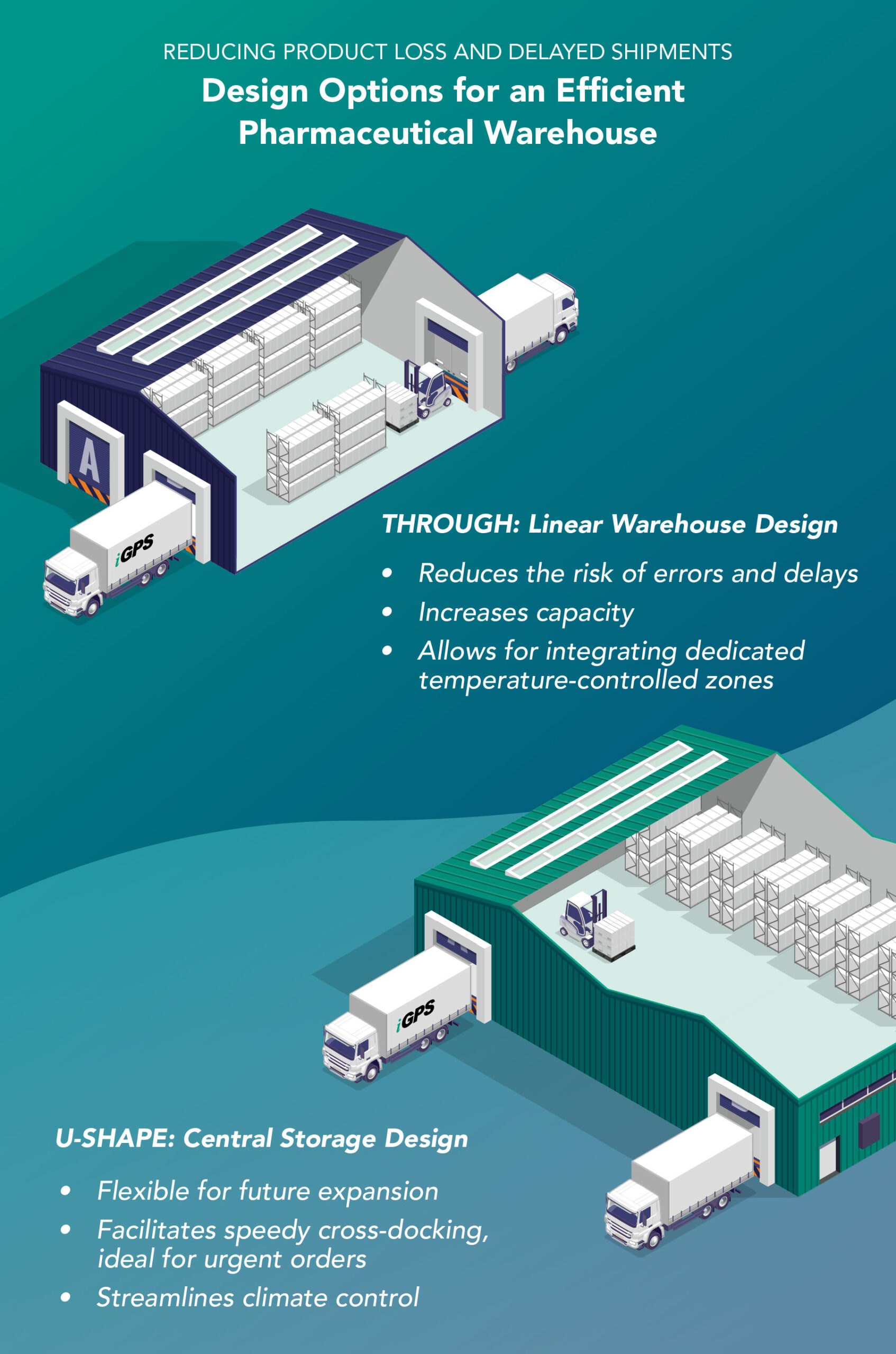
Because pharmaceutical warehouses can be sensitive to external contamination, temperature fluctuations, and even lighting, the storage setup must facilitate a first-in, first-out (FIFO) system, ensuring the safety and security of these valuable products against theft and intentional contamination. This intricate choreography isn’t a mere logistical feat; it’s a lifeline, ensuring samples and medications reach their intended recipients on time.
Two primary designs drive efficiency for pharmaceutical warehouses:
Through patterns guide inventory from entrance to exit, minimizing movement for high-demand medications. U-shape layouts encircle central storage, channeling all traffic through a single point and allowing flexibility for future expansion.
With both designs, items in high demand find their place nearest to the loading dock, while less frequently accessed items rest further away. Ultimately, the ideal layout is tuned to each company’s specific needs.
Through Warehouse Advantages: | Circular Warehouse Advantages: |
---|---|
LINEAR DESIGN Focus on efficiency: The ‘through’ layout excels in first-in, first-out (FIFO) inventory management. Emphasize clarity: The linear route of a ‘through’ layout simplifies picking and packing, reducing the risk of errors and delays. MULTIPLE CHANNELS Highlight increased capacity. Multiple conveyor channels make it easier to handle peak demand for critical medications. DiISCRETE TEMPERATURE AREAS: Focus on flexibility. ‘Through’ layouts allow for integrating dedicated temperature-controlled zones, keeping sensitive medications safe. | COMBINED TRIPS: Forklift efficiency benefits. The U-shape layout lets forklifts deliver new inventory and pick up outgoing orders in a single seamless loop, maximizing efficiency and saving time. CROSS-DOCKING Rush-order ready. The U-shape facilitates speedy cross-docking, allowing incoming orders to be immediately dispatched without storage delays, which is ideal for urgent orders. ENHANCED SPACE CONTROL Streamlined climate control. The U-shape’s single-entry point simplifies climate control, ensuring optimal conditions for sensitive medications throughout the facility. From temperature to access, the U-shape’s closed-loop provides a tightly controlled environment, safeguarding medication integrity and optimizing storage conditions. |
For a pharmaceutical facility, a “through” layout stands out as the most efficient option due to its inherent support for first-in/first-out shipping and straightforward linear product flow, simplifying organization, and accurate picking.
Meeting Pharmaceutical Warehouse Requirements with Equipment and Automation
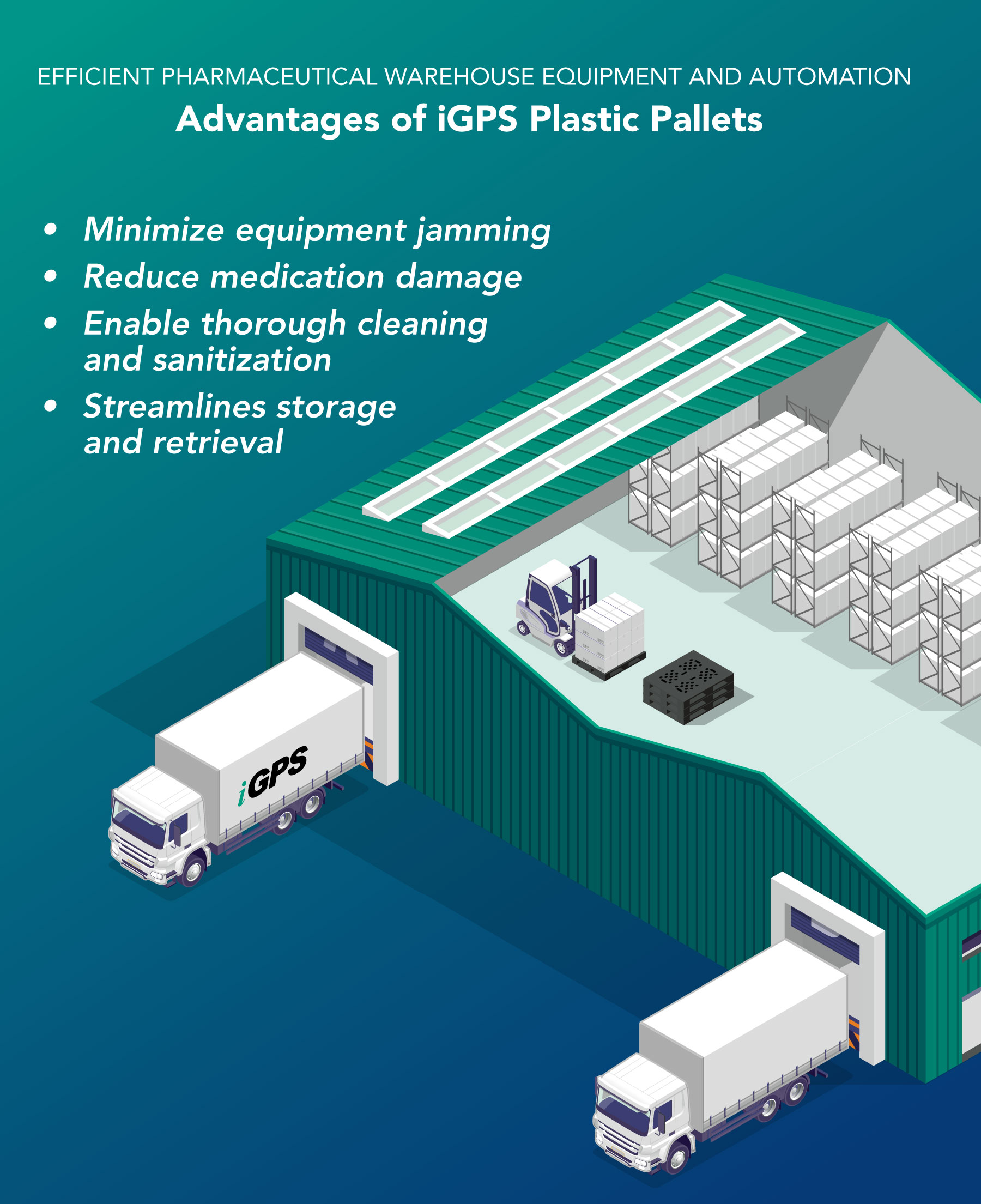
Enhancing warehouse efficiency is achievable through the utilization of pallet racks, a strategy proven to optimize cube utilization and maximize storage capacity. The integration of pallet moles, or pallet shuttles, eliminates the need for aisles, representing a straightforward and cost-effective automation method that operates linearly. Implementing pallet racks and shuttles not only streamlines warehouse layouts but also significantly increases storage space, enhancing overall operational efficiency.
For pharmaceutical warehouses seeking enhanced efficiency, the pallet mole offers a compelling solution. This automated system uses robots on tracks to lift and maneuver pallets within storage racks. This system, operating on a first-in/first-out basis, can enhance shipping accuracy and minimize picking errors.
Plastic pallets are advantageous for warehouse automation, providing uniform weights, dimensions, and strength crucial for seamless operations and product preservation. Their reliability allows for consistent functioning, minimizing disruptions and potential damage.
Unlike their wooden counterparts, they minimize jamming, protect medications from damage, and readily enable thorough cleaning and sanitization, safeguarding vital drugs and sensitive supply chain equipment like racks and pallet moles. Together, these innovative shipping platforms, properly implemented automated systems and processes, and an optimized facility design can help pharmaceutical enterprises streamline their storage and retrieval for maximum efficiency and profitability.
The iGPS pallet pool offers a hygienic and lightweight plastic pallet, perfectly tailored for pharmaceutical warehouses seeking efficient automation solutions. Our lightweight, recyclable plastic pallets are distributed via a pooling model, which reduces carbon emissions. For more information, contact us at 1-800-884-0225, email a specialist at switch@igps.net, or visit our contact page.
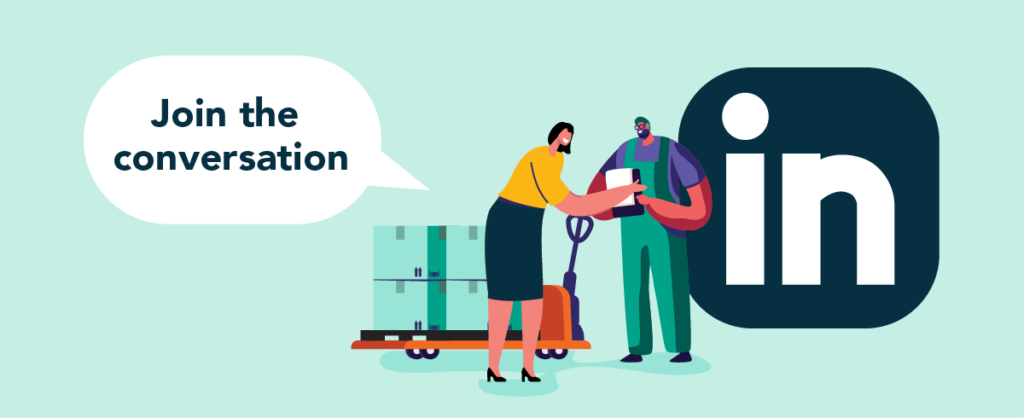