ARTICLE UPDATED ON MAY 22, 2023
What Is Palletizing?
Pallets are a crucial element of the supply chain. Inherently simple in structure, pallets are used to store, protect, and transport materials. Palletization is a term used to describe the process of placing materials and packages onto pallets. Though it may sound simple, palletizing for high-volume operations has advanced over time to increase production efficiency. In fact, the palletizer market is one of the few that has grown rapidly since the onset of the pandemic, prompting investment in automation and robotics to better manage operations.
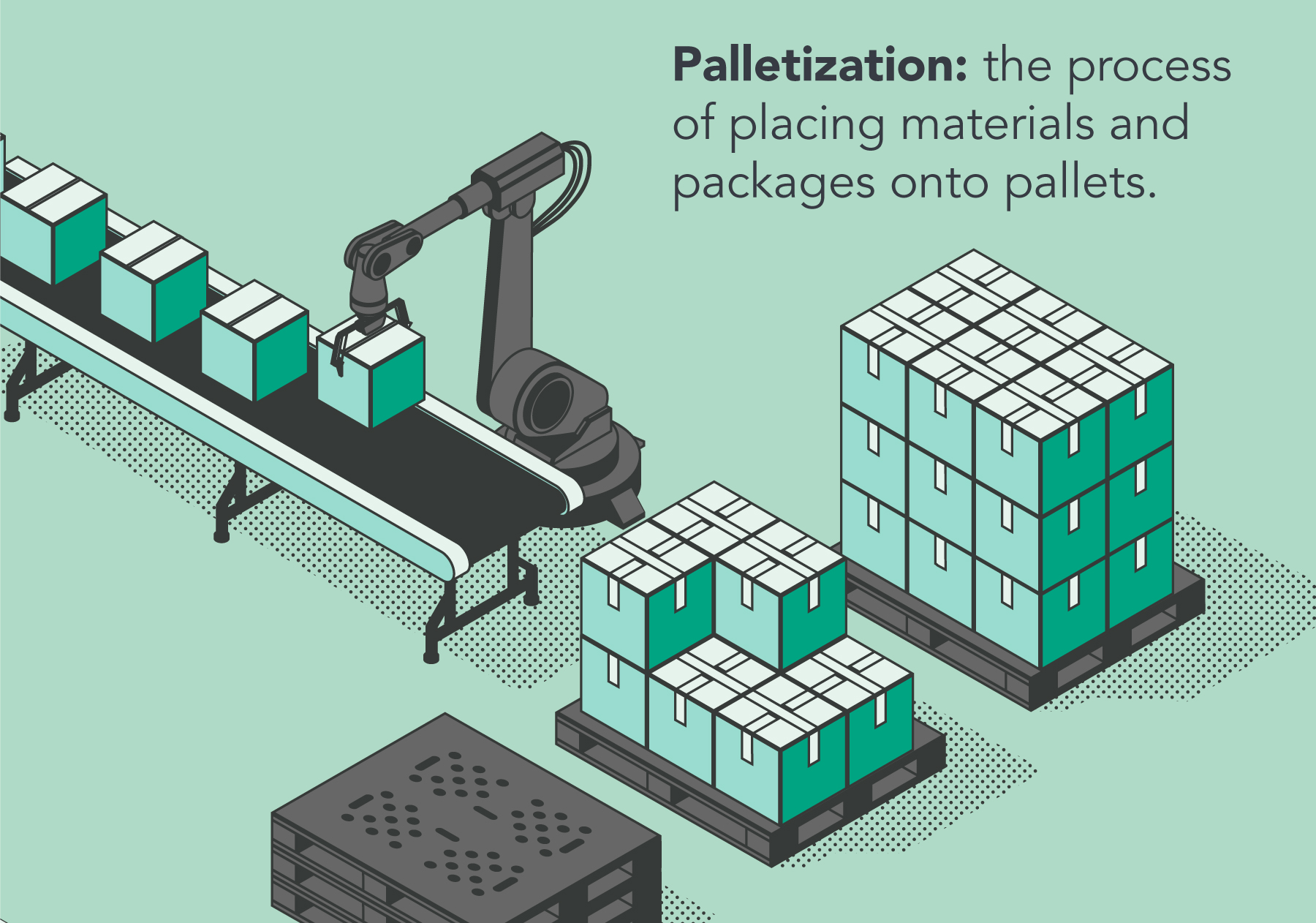
Palletizing Your Products for Safe and Stable Pallets
Palletizing involves converting multiple smaller products into a single load that can be moved as one unit. The goal is to prevent motion among the smaller parts that make up a palletized load by evenly distributing the weight. An improperly stacked load can potentially result in product damage or personal injury. Palletizing originally was accomplished by hand, but today’s automated systems are much more sophisticated.
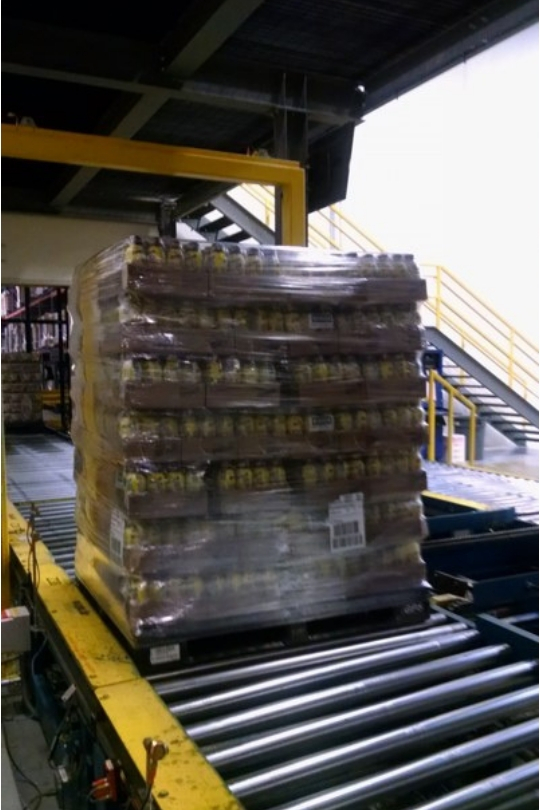
Businesses can reduce product damage during transportation by following some basic rules:
- Fill Boxes Fully: Empty or partially empty boxes can be crushed during handling, and the gaps formed by crushed corners can cause stacks to shift. Safeguard each box with additional packaging if it is not filled with products to prevent damage.
- Distribute Weight: The heaviest boxes should always be placed on the bottom of the stack, and weight should be spread evenly across each pallet.
- Stack Boxes Tightly: It bears repeating that packages must be stacked without gaps to maintain stability. Each box must be aligned to the very edge of the pallet without spilling over the sides. Overhanging boxes are problematic and disrupt the organization and stacking of pallets.
- Fill Gaps: Alternating the pattern of the cartons between layers makes it easier to avoid gaps that can form during transport. Using flat sheets of cardboard between layers can add to the stability of the pallet.
- Wrap Tightly: Once products have been tightly stacked, use three to five layers of plastic wrap to neatly bind them down to the pallet. Cardboard corner protectors can also be used to further stabilize the load. If necessary, smaller boxes can be packed into larger cardboard containers for greater stability.
While many products fit neatly into standard-sized boxes, businesses also need to ship long or awkwardly shaped goods. If these are highly customized single-lot items like machine tools or fabricated frames for industrial equipment, strapping them down tightly to the pallet and padding them may be acceptable. However, when moving high volumes of products such as these, customized cardboard containers should be used for palletizing to ensure the safety of the product and workers.
In highly standardized sectors such as the beverage industry, robotic palletizers have become customary. Automated palletizers can easily handle repetitive work and free up employees for other tasks. This is more important than ever due to ongoing staffing challenges caused in part by the pandemic.
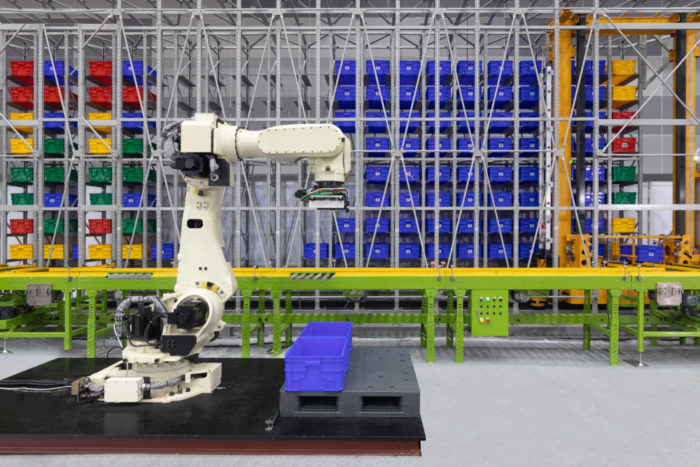
Types of Automated Palletizers
- Inline Palletizers: Automated palletizing was developed in the 1970s, using a combination of conveyor belts and industrial sorting equipment to arrange packages into preset patterns. To stack products, each container layer was clamped into place and lifted off the conveyor belt and onto the pallet. The entire pallet was then rotated before the next layer went into place to alternate the pattern. This type of system is called an inline palletizer. Modern inline palletizers use the same process with more sophisticated high-speed equipment.
- Robotic Palletizers: A decade later, in the 1980s, articulated robot arms like those used in automotive manufacturing were introduced. Robotic palletizers have the advantage of being able to move individual products and can be programmed to arrange goods of various sizes and shapes without altering the physical equipment necessary to complete the task. In fact, robotic palletizers have advanced to the point that they can stack several different types of products on a single pallet. Robotic palletizers are far more efficient for mixed-use pallets than their inline counterparts, which often require the diversion of packages onto an entirely different line to change the layer pattern.
Choosing an Automatic Palletizer
Inline palletizers are generally quicker and work well with high volumes of a single product, such as canned goods. However, they do not work as well for manufacturers producing a variety of goods at the same location. Therefore, many manufacturing and logistics systems are switching to an omnichannel model. When a single production line handles many types of products, it is common for manufacturers to use both types of palletizers in one facility. For example, an inline palletizer may have a robotic arm next to it to take over when atypical products are being palletized. This enables the speedy handling of high volumes of goods as well as the efficient palletization of specialty loads.
Whether you choose a robotic or inline system, consistency is key. Packages must have precisely the right dimension and weight for the conveyor’s belts to position them correctly. A package of goods with a different shape from the others can disrupt the pattern created by the robotic arm and throw the system out of alignment.
While it’s vital that your products maintain a consistent weight and shape when working with automated palletizers, it’s equally essential that your pallets themselves don’t vary in weight or dimension. Since wood is an organic material that can expand, contract, absorb moisture, and splinter, it does not make an ideal partner for automated palletizers. Reusable plastic pallets, such as those manufactured by iGPS, pair well with automated systems due to their durability and uniformity. Each plastic pallet has set dimensions and does not expand or contract, allowing automated palletizers to stack and organize goods quickly and efficiently.
Plastic pallets can help businesses streamline supply chain automation, whether working with palletizers, depalletizers, or Automated Storage and Retrieval Systems (ASRS). They also are easily paired with RFID (Radio-frequency Identification) tracking throughout the supply chain.
Companies committed to the latest supply chain automation technologies use plastic pallets from iGPS, which are lightweight, recyclable, and help streamline your supply chain. For more information, contact us 1-800-884-0225, email switch@igps.net, or visit our contact page. We also invite you to follow us on LinkedIn.
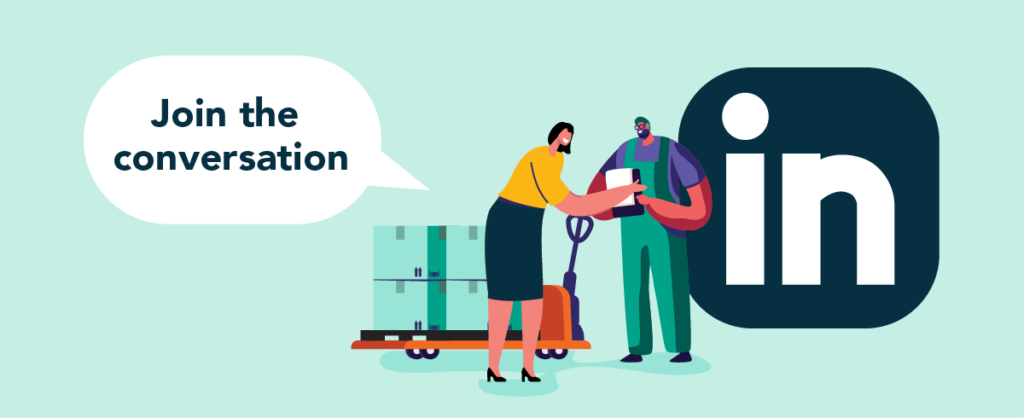
Image 1: Previously published: www.ocme.com [GFDL (http://www.gnu.org/copyleft/fdl.html) or CC BY-SA 3.0 (https://creativecommons.org/licenses/by-sa/3.0)], via Wikimedia Commons