Wood shipping pallets have long been the standard in most supply chains purely because there was no viable alternative. While other options are now available, wood pallets are still in wide use simply because many companies aren’t familiar with the alternatives and continuing to use wood is the path of least resistance. However, there are good reasons to consider some of the other options now available. Wood pallets are prone to issues that are likely driving up your Total Cost of Business (TCOB). Maintaining wood pallets in usable condition as well as managing the problems they can cause in production and transportation adds up quickly. High-quality wood pallet alternatives, like plastic pallets, offer cost savings that ultimately go right back into your company’s bottom line.
Why Wood Is a Problem for Pallet Fleets
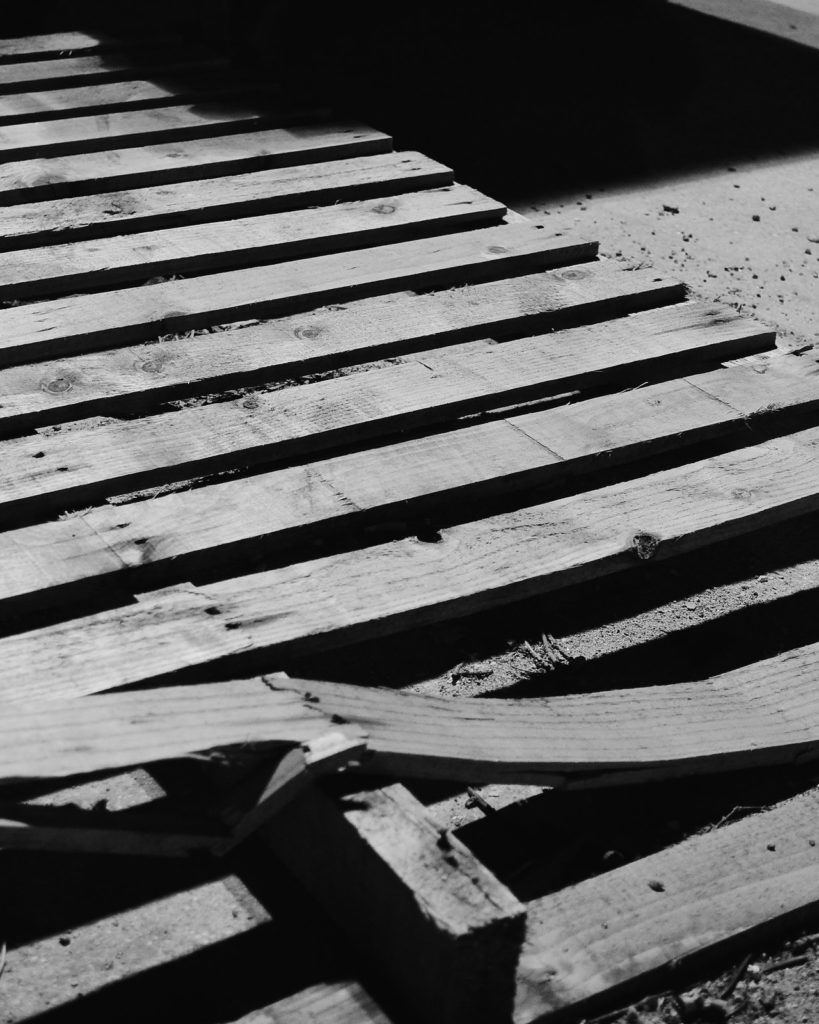
About 80 percent of the world’s commerce is carried on pallets, but these platforms are often overlooked as a way to trim costs and increase efficiency in the supply chain. The idea of changing out a fleet of wood pallets for an alternative platform may not seem cost-effective–until you look at how much wood pallets cost a company. Wood pallets can increase your company’s cost of doing business in the following ways:
- Short lifespan: Wood is a porous material that absorbs moisture, and over time, that moisture will damage the structural integrity of the pallet. Wear and tear can also quickly make a wood pallet unusable by cracking, warping, or loosening pallet boards. While all pallets will eventually require replacement regardless of material, pallets made of materials other than wood–particularly non-porous materials–are much more durable.
- Load rejections: This is a significant problem with wood stringer pallets, as many retailers will reject loads shipped on these pallets outright due to concerns over damage. Loads shipped on wood block pallets may be rejected as well if the pallets are in poor condition or have damaged product during transportation. Rejected loads lead to product loss, increased transportation costs, production delays, and restocking fees. By switching to a high-quality wood pallet alternative such as a plastic pallet, companies can save as much as $0.70 per pallet turn as a result of reducing pallet-related product damage during transportation and retailer rejection fees.
- Product and equipment damage: Wood pallets have multiple boards which can crack, warp, and come loose. Wood splinters may fall into warehouse machinery and damage it. The nails and screws which hold a pallet together can work loose and puncture–or even get left behind in–product packaging. Switching to a platform that doesn’t have these individual parts, like a plastic pallet, can reduce equipment downtime and maintenance, saving manufacturers as much as $0.60 per pallet turn.
- Increased transportation costs: Every extra pound of pallet weight is a lost opportunity to ship more product. Wood block pallets are more durable than stringer pallets but are generally very heavy, which increases transportation costs by lowering fuel mileage. Heavy pallets also reduce the amount of product can be transported in a single load for products that weigh out. Switching to a lightweight plastic pallet can reduce transport expenses by as much as $2.76 per pallet load.
Wood pallets may be the traditional choice in the supply chain, but they are not the most cost-effective option. There are now many alternatives to wood pallets that address the problems of wood as a pallet material.
The Pros and Cons of Wood Pallet Alternatives
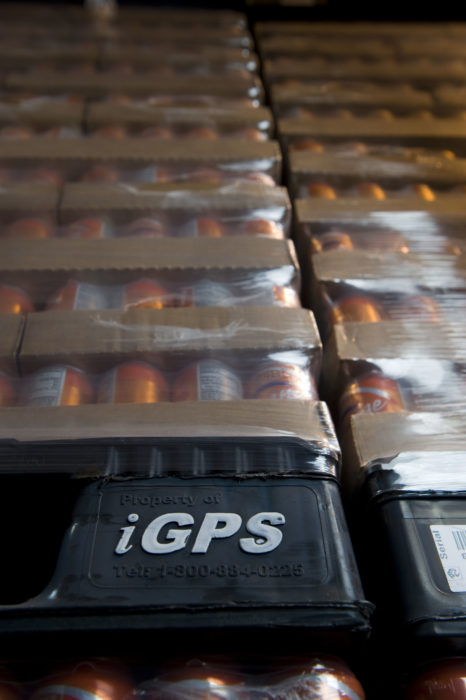
If you’re looking for wood pallet alternatives that can help you improve your business’ operations, there are a number of options, each with its own advantages and disadvantages. The most common types of alternative pallets fall into one of three categories.
Pallet Type | Pros | Cons |
---|---|---|
Cardboard | Corrugated cardboard pallets are lightweight and low cost, allowing manufacturers to save on a cost-per-pallet basis. There are many vendors who offer these pallets, meaning it’s easy to buy a large supply at one time. | The overall costs of cardboard pallets add up quickly. They may be cheaper by the unit but will require near constant replacement. These pallets aren’t as durable or strong as other types and may not be accepted by retailers as they can contribute to product damage. They are usually treated to provide some waterproofing, but cardboard is naturally absorbent and coating damage may affect their integrity. |
Metal | Metal can withstand corrosion, pests, breakage, fire damage and more. They offer top-tier protection, which makes them popular for shipping expensive equipment or fragile products. | Metal pallets are extremely expensive to purchase outright, which makes them appropriate only for a closed-loop system. They also tend to be very heavy, which can lead to high transportation costs. Depending on the type of metal, some metal pallets may also be prone to rust, which can lead to contamination of products. For all of these reasons, metal pallets are not a good choice for high-volume environments. |
Plastic | Plastic is highly durable, easy to clean, and resistant to moisture and pests. It resists breakage and doesn’t leave behind wood debris or loose fasteners. It’s also up to 35% lighter than wood, which reduces transportation costs. Plastic pallets are also sustainable, as they can be reused dozens of times and damaged pallets can be reground and used to make new pallets, minimizing waste. | Plastic pallets can be expensive when purchased outright and it can be challenging to find a vendor who can provide a large supply of plastic pallets for purchase. |
For companies looking to balance durability and cost-effectiveness, plastic pallets are the best solution. However, replacing an internal pallet fleet with plastic can be extremely expensive. That’s why many companies choose to use a pallet pooling provider, which rents pallets and handles their repair and reuse.
Using Pooling to Make Wood Pallet Alternatives Cost-Effective
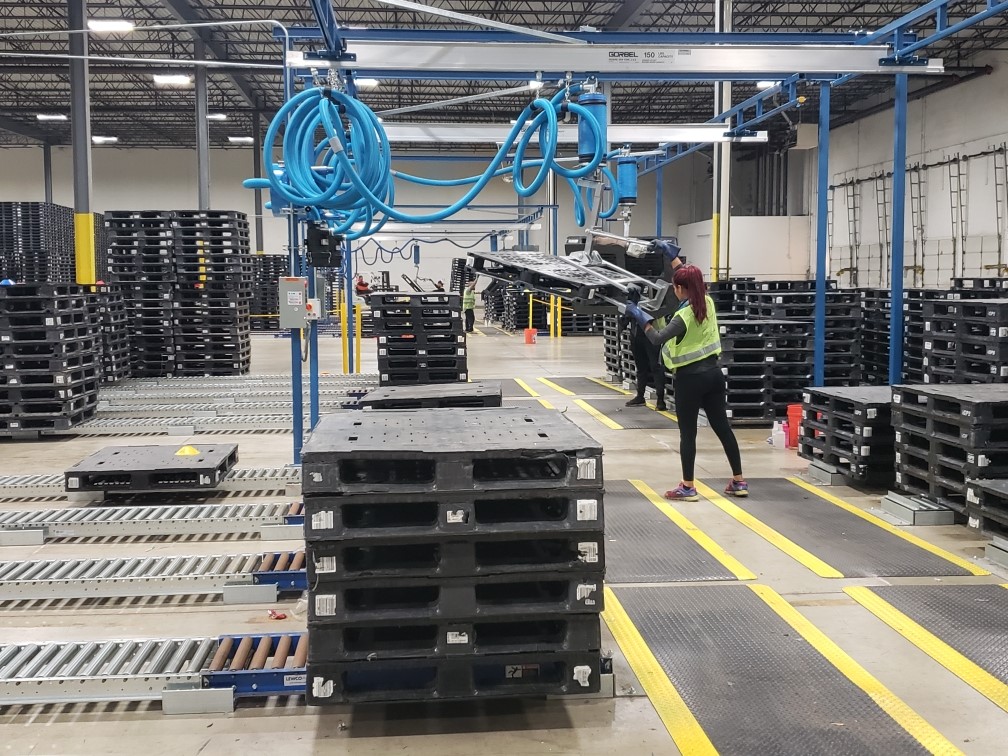
Durable, lightweight wood pallet alternatives can reduce your company’s TCOB by standing the test of time and reducing wear on equipment. Plastic pallet pooling makes switching to a high-quality platform like this easy and cost-effective. It eliminates the cost of purchasing an entire fleet of platforms outright and makes the pallet pooling company responsible for pallet logistics and maintenance.
Pallet pooling is the most effective way to make use of wood pallet alternatives like plastic.
Furthermore, pallet pooling is scalable, allowing manufacturers to adjust their supply to match their needs and making it possible to reclaim warehouse space that might otherwise be used to store quantities of idle pallets needed for peak seasons.
Pallet pooling is the most effective way to make use of wood pallet alternatives like plastic and can add to the advantages of alternative-material pallets by eliminating the hassle and cost of pallet repair and maintenance, transportation, and storage. In other words, a pallet pooling provider does everything necessary to make sure your company has quality pallets in the right quantity, at the right time and place. By choosing a plastic pallet pooling service, your business can do away with the frustrating drawbacks of wood pallets and the high cost of maintaining a pallet fleet.
iGPS plastic pallet pooling helps reduce your business’ TCOB by providing the high-quality pallets you need when you need them, with none of the time and effort it takes to maintain a fleet. To discuss your options and how plastic pallet pooling can impact your bottom line, contact us at 1-800-884-0225, email a specialist at switch@igps.net, or visit our contact page.
Image 2: Flickr CC user Dan Morris