How to Reduce Product Losses in the Supply Chain
When an employee starts an entry-level job in the retail sector, one of the first things they are taught is where to put damaged products. Usually, damaged items are placed in an unused corner of a stockroom until the store manager can ship them back to the distribution center for a credit or exchange. The routine nature of this practice indicates how often product damage occurs. Product damage in manufacturing can cost as much as $1.90 per pallet annually, while product damage during transportation costs up to $0.48 per pallet, and product losses in warehouses and distribution centers cost as much as $3.20 per pallet per year. These losses in the supply chain can add up to substantial lost profits over time.
Finding effective ways to reduce product losses in the supply chain should be a priority for every company. Improvements in packaging, shipping materials, and logistics data collection make it possible to reduce product losses by at least a few fractions of a percentage point, which can make a surprising difference in a company’s bottom line.
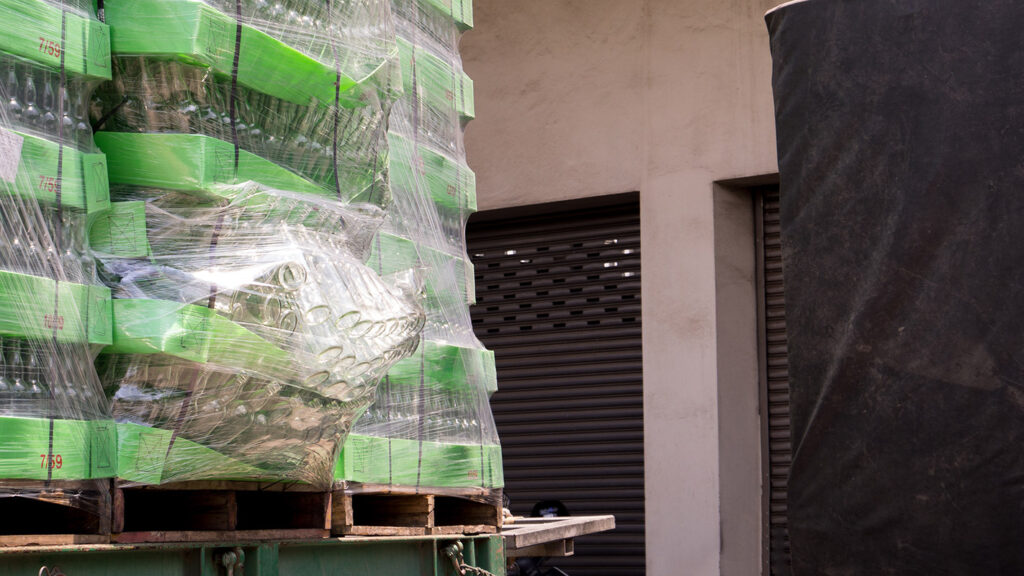
Causes of Supply Chain Product Loss
There are many ways products can be damaged or rejected and many points along the supply chain where this can happen. However, causes of product loss generally fall into the following categories:
- Improper Packing: Many products are damaged during transportation by a failure to pack them into cartons properly or a failure to correctly stack those cartons on a pallet. However, far more are damaged by incorrectly designed packaging. For instance, some products are shipped in cartons that double as shelf displays when a section is torn away. This design compromises the integrity of the carton and makes it more vulnerable to damage as a result of being crushed or shifted during transport.
- Mechanical Failure: Supply chain automation has improved throughput in warehouses and distribution centers by working at a speed manual labor can’t match. However, automated systems aren’t always able to sense when something goes wrong, and may damage products by continuing to work after the point at which a human would stop. This may result in the damage of significant amounts of product if it goes unnoticed.
- Platform Failure: Shipping platforms can themselves be a source of product damage. Wood pallet boards may break, introducing product-puncturing splinters and nails into warehouses and trucks. If the central support of a wood pallet breaks, then the entire load is likely to be damaged. Around 12.5 percent of product damage can be attributed to pallets in some way.
- Improper Storage: Storing pallet loads of products in an improper environment will result in the products having to be disposed of even if the packaging remains intact. Cold chain products, like certain foods and pharmaceuticals, are very sensitive to temperature. A small oversight–like failing to secure a cooler door–can cause temperatures to spike and render a product unsafe and unusable.
- Contamination: Improper storage and product packaging damage create the potential for product contamination. Lapses in temperature controls can cause the growth of fungi and bacteria, as can the sustained presence of moisture in transport and storage areas. Foreign materials like splinters and fasteners may also cause foreign object contamination. Either type of contaminant can make food or pharmaceuticals unsafe for consumption.
In the food supply chain, estimates suggest that around 26 percent of food waste occurs during post-harvest processing and distribution–before the food gets to the consumer. Globally, supply chain food losses are estimated at approximately a third of the total food produced. Losses in the consumer packaged goods supply chain are heavily dependent on product type, so total losses there are more difficult to calculate.
What is certain is that reducing the most common incidents that cause product damage can substantially reduce product losses in the supply chain. This can add up to substantial savings overall, ultimately reducing a company’s Total Cost of Business (TCOB) and improving its profit margins.
Ways to Reduce Product Losses in the Supply Chain
There are many causes of product loss at multiple points along the supply chain. Significantly reducing overall product loss requires a multipart solution that relies on better materials, platforms, and procedures.
Redesigning Packaging
Possibly the most wide-reaching change a company can make to reduce product losses in all parts of the supply chain is to redesign its product packaging to better protect the product. Replacing cartons that double as shelf displays with ones made to specifically withstand the rigors of the supply chain is one way to reduce product damage during transportation and handling. For products like pet food, replacing bag packaging with stiffer cardboard boxes is another. While redesigning product packaging this way is usually effective, it can be expensive. A similar benefit for less expense can be had by switching to a more reliable shipping platform.
Choosing a Stronger and More Reliable Shipping Platform
Plastic pallets are one tool for reducing product losses that can be easily implemented within a supply chain without much disruption to daily business operations. Plastic pallets are tougher than the wood pallets common in most supply chains, which reduces the amount of product lost due to platform breakage. Reducing the potential for platform failure also eliminates one of the variables that can cause shifting damage to product packaging.
The durable unitized construction of a plastic pallet also results in less packaging damage due to nails and splinters. Fewer fragments and no nails mean there less chance of jammed or damaged machinery due to debris, which eliminates another source of product damage. Finally, the absence of large gaps in the deck of a plastic pallet means that packaging cannot slip through the deck where it can be more easily torn. All in all, plastic pallets are an effective way to reduce product losses in the supply chain without a significant overhead expense. Other methods of reducing product losses are more procedural than mechanical, but here plastic pallets can play a role, too.
Incorporating Tracking Methods
It is currently possible to track a teenager through their phone or a lost pet through a GPS-enabled collar. Yet, if a major consumer goods company were asked to locate a load of their products after they had left the loading dock and before they had arrived at their destination, that company would likely not be able to.
Often, the trick for companies looking to reduce product loss is to identify points where product damage most often occurs. Many times, product loss is due to procedural lapses, and corrective action at the right location would be able to reduce product loss. Pinpointing where these lapses occur has in the past been a major challenge. Today, there are a variety of possible solutions and plastic pallets can easily be embedded with devices that provide the means to enable tracking and data collection. Each iGPS plastic pallet is equipped with a Global Standard (GS1) identification number that can be read by manually scanning a barcode or through a radio frequency identification chip (RFID). When this identifier is collated with the SKUs of the products and the vehicles transporting the pallet, it provides a means to track product damage back to the point where it occurred. This ability to easily track pallets can make the entire supply chain transparent to logistics managers and provide a basis for identifying shortfalls in procedures that may be causing product damage.
Maintaining Procedures and Keeping Exacting Records
Another way to reduce product losses in the supply chain is through the use of better and more consistent procedures. For instance, the procedure for storing cold chain items should ensure not only that items are in the proper location and that their temperature is being maintained correctly, but also that workers are observing the proper measures to keep coolers and freezers at their specified temperatures. This might entail keeping doors locked and providing appropriate maintenance and cleaning for refrigeration systems. In both cases, it’s most important to account for the needed procedures in scheduling and make sure records are kept. The same can be applied to mechanical equipment like palletizers, forklifts, and Automated Storage and Retrieval Systems (ASRS). Many mechanical failures and the resulting product damage can be prevented with proper maintenance.
Ensuring Pristine Hygiene
Preventing contamination also involves keeping loading docks, warehouses, and vehicles scrupulously clean and dry. This means that any debris that accumulates, such as discarded cardboard, plastic wrap, and tape, needs to be swept up and properly disposed of. It also means that detritus-like splinters and nails that are left behind by aging wood pallets should be picked up and removed routinely or eliminated from supply chain areas. One of the major advantages of plastic pallets is their lack of wood and nails, which means that supply chain facilities using plastic pallets tend to be cleaner than those using wood pallets, and products at these facilities are less likely to become contaminated by foreign objects. Plastic also provides a non-absorbent surface that can be easily cleaned and sanitized, preventing cross-contamination of products, supply chain vehicles, and facilities.
How iGPS Supports Supply Chain Solutions
There is no magic bullet for eliminating product loss in the supply chain, no one single solution that automatically brings product loss to zero. However, iGPS plastic pallets may come close. They provide a myriad of useful advantages over wood pallets that support companies looking to reduce product losses in the supply chain.
Effective solutions to product loss require extensive data collection, careful analysis, and creativity in developing solutions. Nor is reducing product losses something that can be done just once. The supply chain is dynamic and ever-changing, and new problems emerge as old ones are fixed. The iGPS plastic pallet is a consistent and uniform shipping platform that offers intelligent support for products by making product handling more efficient and profitable.
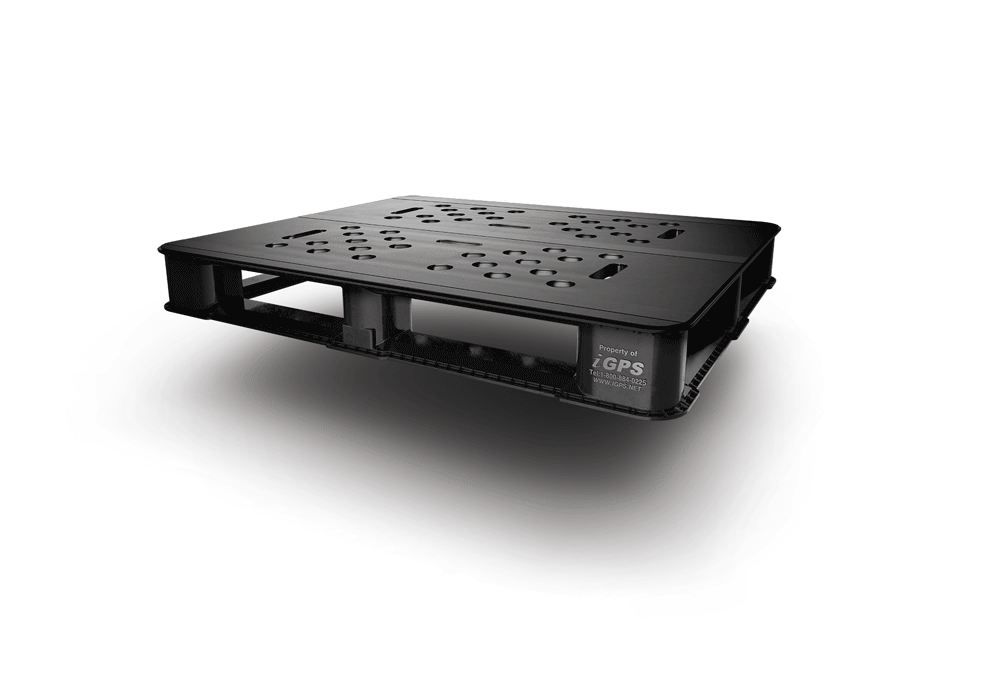
The iGPS Plastic Pallet Supports Supply Chains by:
Maximizing ASRS efficiency by providing a lightweight but strong shipping platform with consistent weight and dimensions.
Improving transparency in the supply chain with track and trace capabilities and support for Warehouse Management Systems.
Improving the hygiene and sanitation of processing, loading, and transportation areas.
The benefits of plastic pallets are further enhanced through the use of a pallet pooling system. Pallet rental provides companies with the pallets they need when they are needed, and eliminates the hassle and expense of managing an in-house pallet supply. It is the most efficient and cost-effective way to use plastic pallets to reduce product losses in the supply chain and lower a company’s Total Cost of Business over time.