ARTICLE UPDATED ON JUNE 21, 2023
Warehouse Racking Safety Guidelines: Satisfying OSHA
The Occupational Safety and Health Administration (OSHA) has an important job — keeping workplaces and workers safe. However, its rules are often nuanced, complex, and hard to follow, making it easy for employers to accidentally violate an obscure rule. Violations usually carry steep penalties — updated in January of 2023, penalty amounts now range from approximately $15,000 to as much as approximately $150,000. The possibility of violation can cause large enterprises to pour resources into ensuring that they’re in compliance, while smaller companies dread the possibility that they may have violated an obscure rule without being aware of it.
Updated in January of 2023, penalty amounts now range from $15,000 to $150,000
The rate of warehouse industry injuries is typically higher than the national average across all industries. According to the U.S. Bureau of Labor and Statistics, in 2021, there were 253,100 injuries and illnesses reported in the transportation and warehousing sector. Therefore, it might be expected that OSHA has created detailed guidelines for the safe operation and use of warehousing equipment. But the truth is, when it comes to warehouse safety, and more specifically warehouse racking safety guidelines, OSHA doesn’t offer much guidance. There are a few applicable rules:
- 1910.176(a) – Discusses the operating space required for warehouse equipment to safely maneuver.
- 1910.176(b) – States that material stored in tiers must be made safe.
- 1910.159 – Covers fire sprinklers and requires 18 inches of clearance between the rack and the sprinkler. These OSHA guidelines may be vague, but by following some basic, commonsense principles and maintaining a maintenance schedule, it is possible to be confident that your facility has satisfied OSHA regulations.
Satisfying Warehouse Racking Safety Guidelines
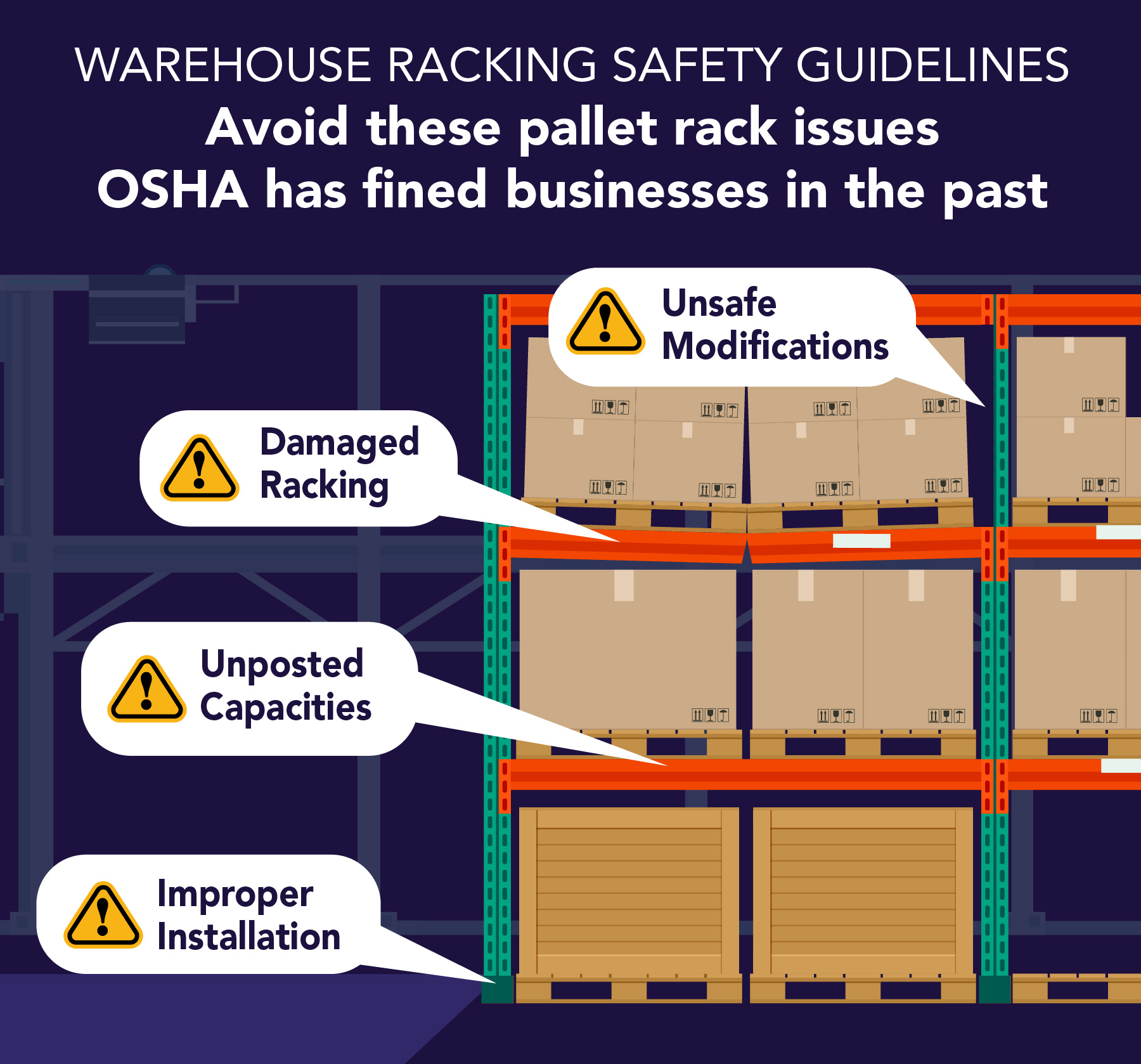
The most common reasons that OSHA cites companies for their pallet racking have to do with basic installation, maintenance, and repair issues. Although OSHA has no specific warehouse racking safety guidelines, they are covered by the general clause of the Occupational Safety Health Act of 1970 that created the agency, which states simply that each employer shall provide a workplace that is free from recognized hazards. In other words, if your pallet racking is not installed correctly or poses an obvious hazard, you can be found in violation of OSHA regulations and fined. OSHA has found various reasons to fine businesses over their pallet racks:
- Improper Installation: In order to be used safely, a pallet rack needs to be properly installed. Failure to properly anchor each post and brace to the specifications dictated by the manufacturer is a safety violation.
- Damaged Racking: Equipment damage isn’t unusual in warehouses, and pallet racking is subject to damage from forklifts that bump into the posts or into the horizontal cross braces supporting the pallets. Dings, dents, and bent metal reduce the overall strength of pallet racking, and these issues should be repaired quickly to keep employees safe.
- Unsafe Modifications: When a pallet rack is damaged, occasionally a cross member may be replaced with any piece of steel that is convenient and held in place with fasteners that were handy at the time. As a non-engineered modification, this type of repair can be dangerous and will be found in violation of OSHA requirements.
- Unposted Capacities: It is important that all employees adhere to the load capacities provided by the pallet rack’s manufacturer. To maintain safety, the maximum load should be clearly posted to avoid overloading and prevent damage to the racks or employee injury.
The above issues can be prevented by implementing an inspection and maintenance cycle for your facility racking. Pallet racks should be inspected upon installation and periodically checked for damage. If bent bars or damaged vertical posts are discovered, the affected section should be taken out of use until it can be properly repaired. Parts used in repairs should be provided by the manufacturer or should meet with the manufacturer’s specifications to ensure employee safety.
Rack and Pallet Load Limits
Pallet racking is designed to easily hold pallets loaded to the maximum capacity. The steel framing that makes up most warehouse racking is generally built to accommodate loads carried by the six ISO standard pallet sizes, which includes the standard North American 48” by 40” Consumer Brand Association spec pallet. A typical pallet rack compartment can hold two pallets, each weighing approximately 2,000 lbs., for a total of 4,000 lbs. Exact loads can vary depending on the configuration of the pallet rack and the types of pallets used.
Ideally, only wood block pallets and pallets made of sturdy alternative materials such as plastic and metal should be stored on pallet racks. Low-cost stringer pallets are more flimsy and become unreliable after a few trips through the supply chain. While OSHA doesn’t take issue with storing stringer pallets in racks, if a pallet failure in a rack leads to injury, they may. High-quality plastic pallets are able to hold more weight than wood block or stringer pallets and may be the best way to keep employees safe and avoid potential OSHA violations.
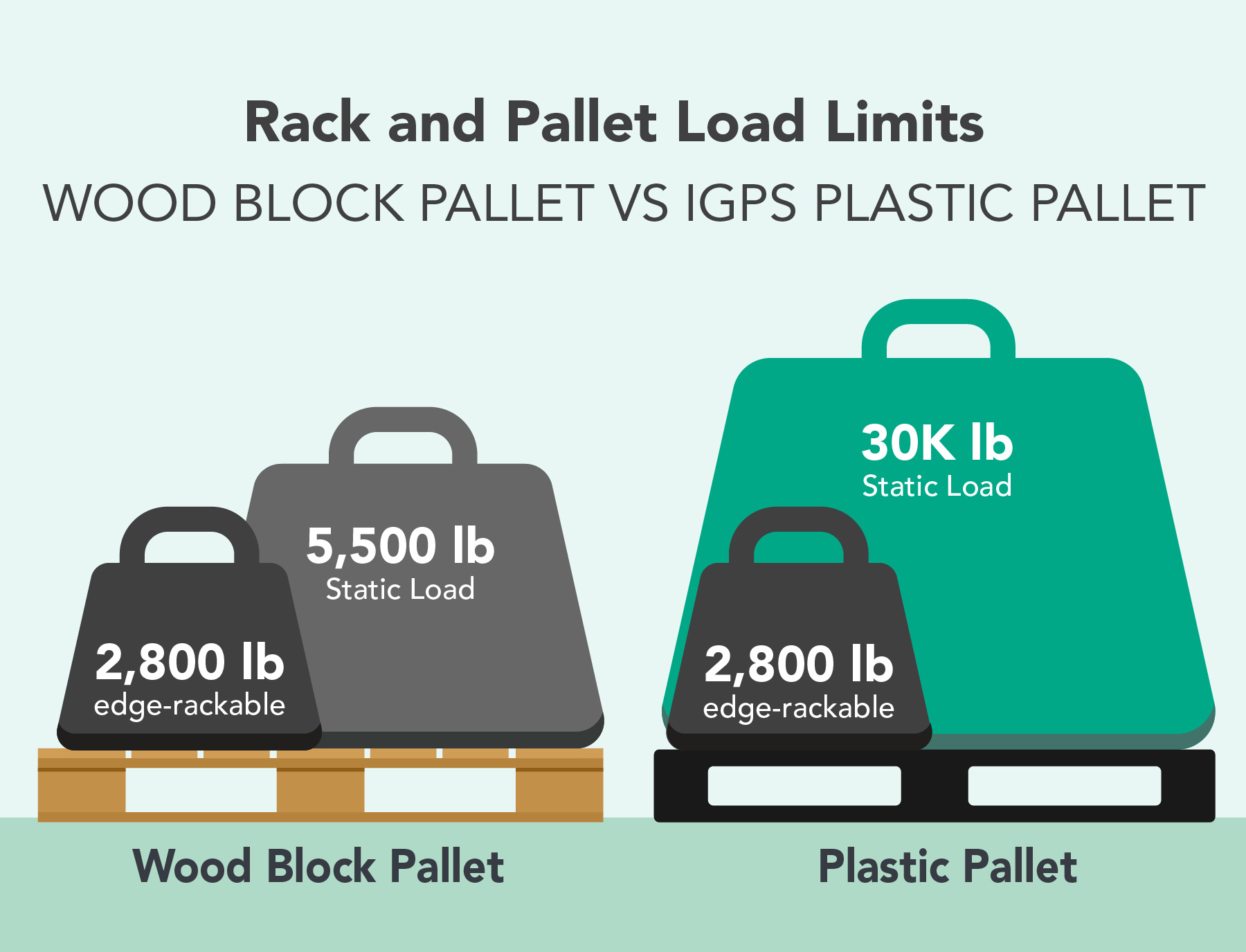
However, the strength of plastic pallets — some high-quality plastic pallets can support 2,800 pounds, edge-rackable — can also tempt employees to load pallets with more product than the racking can bear. Unless a facility is equipped with racking that can support the extra weight, it is not advisable to load a pallet to its maximum capacity. For this reason, it’s important to clearly communicate the rack loads in your facility by labeling them.
Because plastic pallets can have a higher load-bearing capacity than most other types of pallets, it’s especially vital to communicate their maximum load and the load they are currently bearing. A plastic pallet that is loaded to its maximum capacity might be shipped from a facility equipped with racks that will hold the weight, to one that has less capable racking. Adding the load weight to a pallet license plate is one solution, but these labels can be lost in transit. A more desirable option is to associate the data with a permanent feature. Some plastic pallets are equipped with GS1-compliant tracking features through barcodes or embedded RFID transmitters. Data associated with these tracking numbers, which can include SKU types, quantities, or the weight of the pallet, can let facility receiving staff know whether it is safe to put a fully loaded pallet in their racks.
Keeping OSHA satisfied and workers safe often comes down to clearly communicating information — whether through labeling facility racking load limits, or using pallets that can provide data about their product loads. Not only is it the best course of action for our business, but it’s also the right thing to do for our employees.
The iGPS plastic pallet is able to hold heavier static and dynamic loads than a reusable wood block pallet and is equipped with GS1-compliant tracking. For more information, contact us at 1–800-884-0225, email switch@igps.net, or visit our contact page. We also invite you to follow us on LinkedIn.
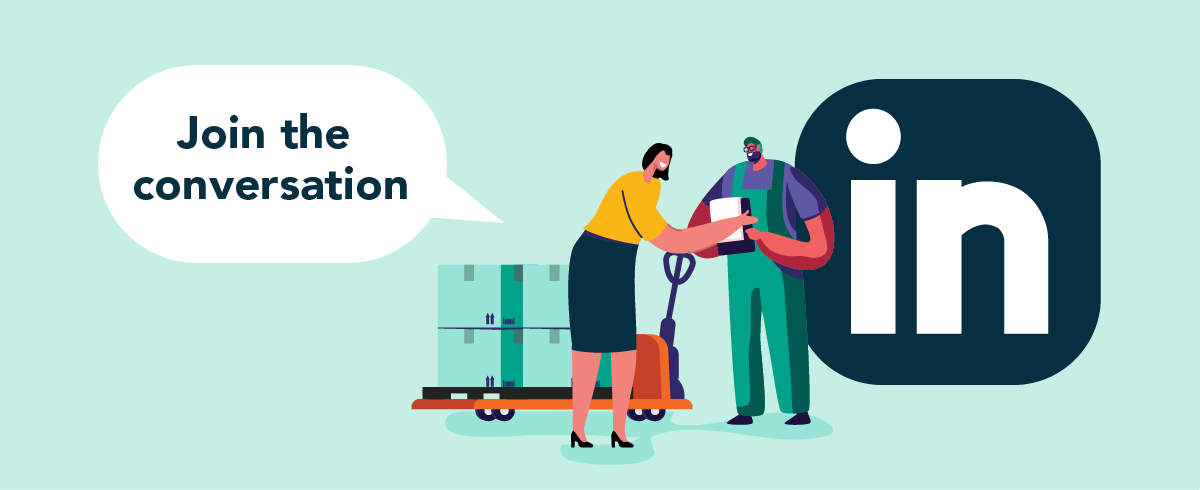