Automated Storage and Retrieval Systems (ASRS) are one of the newest and most impressive innovations among the myriad marvels of the global logistics chain. These automated systems palletize, store, and retrieve products with unmatched speed and precision, vastly increasing throughput and ensuring process controls are consistently followed. The use of these systems and other forms of automation like AGVs (automatic guided vehicles) is rapidly becoming standard in warehouses and logistics systems—but is not without some drawbacks. What is most likely to compromise automated storage and retrieval system safety—and cause accidents that risk injury or damage to machinery and products—is the packaging and pallets that products are shipped on.
Although the technology has dramatically improved over the years, an ASRS still lacks the ability to both spot situations that might cause a safety issue (for products, equipment, or personnel) and enact solutions. Every load of products that passes through an ASRS must be exactly within the system’s specified parameters if it is going to be throughput successfully. If it is not, then the ASRS may be unable to compensate for the variables outside of its pre-programmed settings. Consequences may include spilled loads requiring cleanup, damage to the ASRS that requires repair, or injury to important personnel. The best way to ensure operational safety is to remove variables in product packaging and shipping platforms that can cause interruptions.
Avoiding Automated Storage and Retrieval System Failures
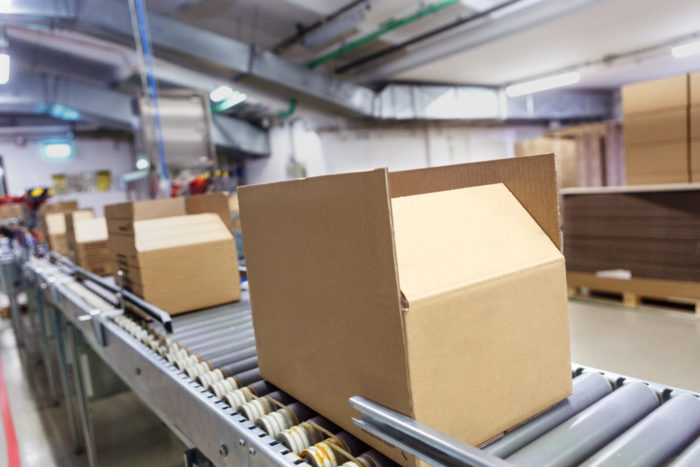
Improper or inadequate packaging can cause operational interruptions in numerous ways. Cartons that are damaged during palletization may stack unevenly; this may cause loaded products to spill off the ASRS, necessitating cleanup. Stray cartons and damaged products may damage other loads, further expanding the problem. ASRS aren’t generally designed to be easily accessed by personnel, so a cleanup operation is likely to take some time. Loose debris can also get caught in tracks, gears, and other pieces of machinery, causing permanent damage. ASRS tend to have a tall footprint that helps improve cube utilization in the warehouse, but since loads and cartons can be quite heavy, falling objects from unstable loads high overhead are a definite hazard for both equipment and personnel.
Product packaging must be of a size that can fit evenly on a pallet without overhanging the edges.
A fundamental factor for ensuring automated storage and retrieval system safety is secure and durable product packaging. Product that has spilled from its packaging while being managed by an ASRS will necessitate stopping the system to clean up the product. It may also mean discarding products that have been compromised, which can cut deeply into margins. For automated storage and retrieval system safety, the boxes and cartons that products are packed in must meet the following criteria:
- Proper Size: Product packaging must be of a size that can fit evenly on a pallet without overhanging the edges, leaving voids between cartons, or fitting awkwardly or unevenly on the pallet, unbalancing the load.
- Stability: Product packaging must also be stacked in such a manner that it does not become unstable when the pallet is moved or in motion. It should remain in place until the pallet arrives at its final destination.
- Durability: The packaging that holds products during transportation should be robust enough to shrug off moderate impacts without being structurally compromised. This is to protect both the product and the structural integrity of the whole load. If a single box is damaged it should not cause the entire load of stacked products to become unstable.
Wood pallets can be a source of parameter-exceeding inconsistencies that can bring an ASRS to a halt.
Most companies incorporate these requirements into their product packaging, at least to some extent. After all, these requirements are not exclusive to ASRS safety and have been a necessary factor in shipping consumer packaged goods for decades. What has lagged behind, however, is the adoption of a durable, uniform shipping platform designed to work smoothly with an ASRS. The majority of logistics chains are in the habit of using wood pallets—and these can be a source of parameter-exceeding inconsistencies that can bring an ASRS to a halt.
Plastic Pallets Improve Automated Storage and Retrieval System Safety
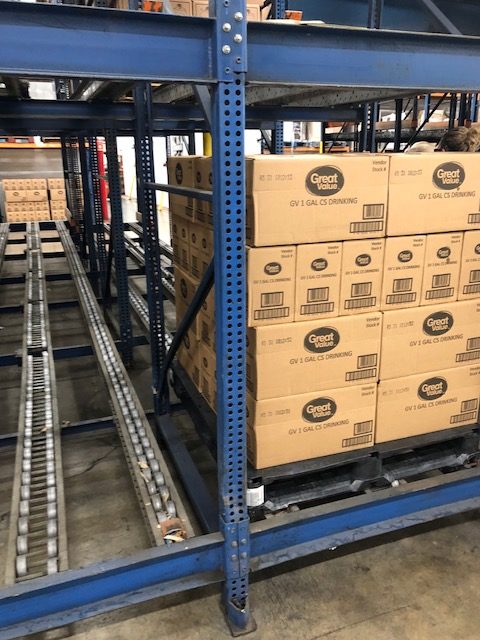
The pallets usually used in an ASRS—like wood block pallets—pose many of the same safety hazards that damaged or unsuitable packaging does:
- Pallet failures can cause falling loads, which may damage other products
- Falling loads as a result of pallet failure can damage the ASRS
- Falling loads as a result of pallet failure can be dangerous for workers
- Pallet failures may require time-consuming cleanup
- Pallet breakages and failures result in loose debris, which can cause damage if caught in the ASRS
Wood pallets also create further issues due to the materials used. Wood is heavier and stiffer than the cardboard used in packaging, which creates a greater potential for injury when pieces fall. Wood pieces and splinters are also more likely than cardboard to do serious mechanical damage to the mechanical systems of an ASRS. The metal nails that hold wood pallets together have even greater potential to do serious damage if they are caught in machinery. The likelihood of these issues happening increases with the wood pallet’s age.
Plastic pallets a consistent weight of less than 50 pounds, which helps to reduce the stress placed on mechanical systems.
The disadvantages of wood pallets are many, but the biggest issue is generally moisture. Wood absorbs water, and this causes many problems, such as:
- Variable Weight: Damp wood pallets can weigh up to 80 pounds, which is a serious issue if an ASRS is programmed to work with their much lower dry weight.
- Variable Dimensions: The expansion of moistened wood fibers changes the overall dimensions of the pallet, which increases the chances of unintended contact with machinery and damage to the pallet and the load.
- Decay: The expansion and contraction of wood when its moisture content changes also causes it to wear faster, and the actions of microbes and fungi on wood are sped up in the presence of water. The resulting degradation of wood over time leads to the splinters, chunks of wood, and loose nails that are a familiar sight in warehouses using wood pallets.
Plastic pallets, in comparison, are superior in all respects for use in an ASRS, supporting and enhancing automated storage and retrieval system safety. They have a consistent weight of less than 50 pounds, which helps to reduce the stress placed on mechanical systems. Since plastic is a nonabsorbent material, its weight and overall dimensions are uniform, requiring the ASRS to account for fewer variables.
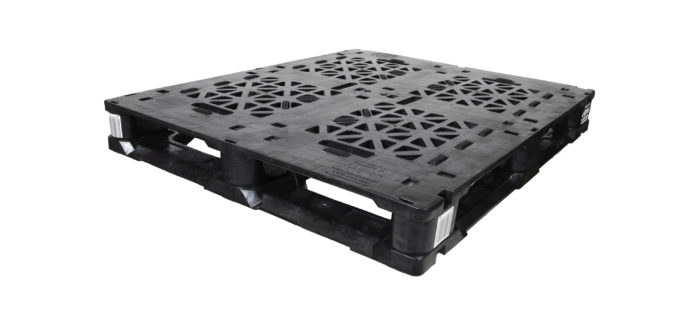
Plastic pallets also have a fastener-free unitized construction without nails or screws that might come loose in an ASRS and get caught in the machinery. (This also has the side benefit of reducing product damage during transportation.) Plastic pallets can improve automated storage and retrieval system safety by removing the variables that cause interruptions to ASRS operation. Using plastic pallets in an ASRS eliminates many of the hazards that pose a risk to valuable machinery and irreplaceable employees, and improves operations and reliability in almost every other area of the logistics chain as well.
iGPS provides dimensionally uniform plastic pallets with consistent weight to its clients. To enjoy the benefits of the best shipping pallet for automated storage and retrieval system safety, give our team a call at 1-800-884-0225, email a specialist at switch@igps.net, or visit our contact page.